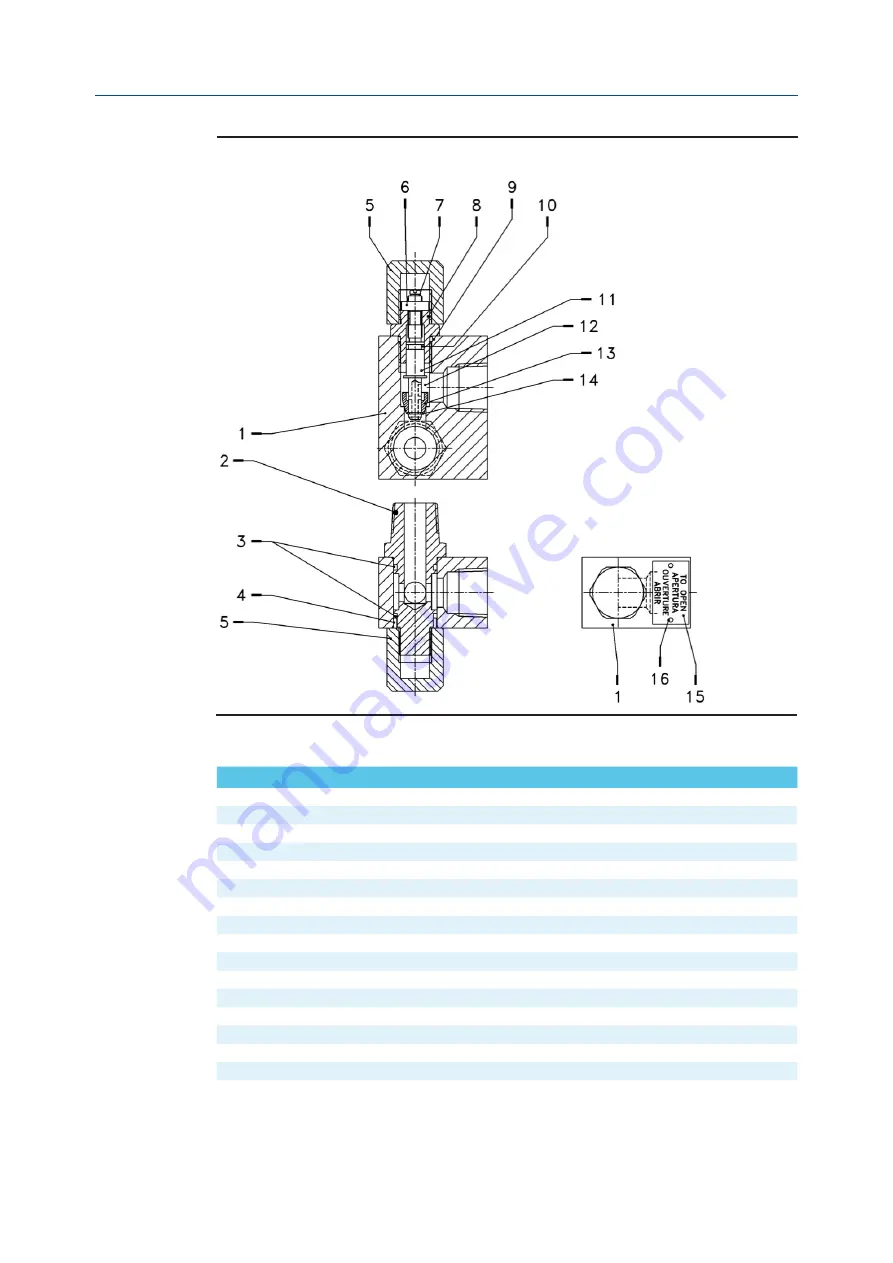
50
September 2020
Installation, Operation and Maintenance Manual
MAN 571_EAC Rev. 1
Layouts
Section 7: Layouts
Item
Qty
Description
Material
1
1
Body
Carbon steel
2
1
Body
Carbon steel
3
1
O-ring
* NBR rubber
4
1
Seal ring
* PTFE + graphite
5
2
Nut
Carbon steel
6
1
Nut
Carbon steel
7
1
Retainer ring
Spring steel
8
1
Flow control valve flange
Carbon steel
9
1
O-ring
* NBR rubber
10
1
O-ring
* NBR rubber
11
1
Flow control valve setting screw
Stainless steel
12
1
Spring
Spring steel
13
1
Plug
Stainless steel
14
1
Retainer ring
Spring steel
15
2
Data plate
Stainless steel
16
4
Rivet
Aluminium
Figure 40
Hydraulic Flow Control Valve
Table 15.
Parts List
NOTE:
* Recommended spare parts