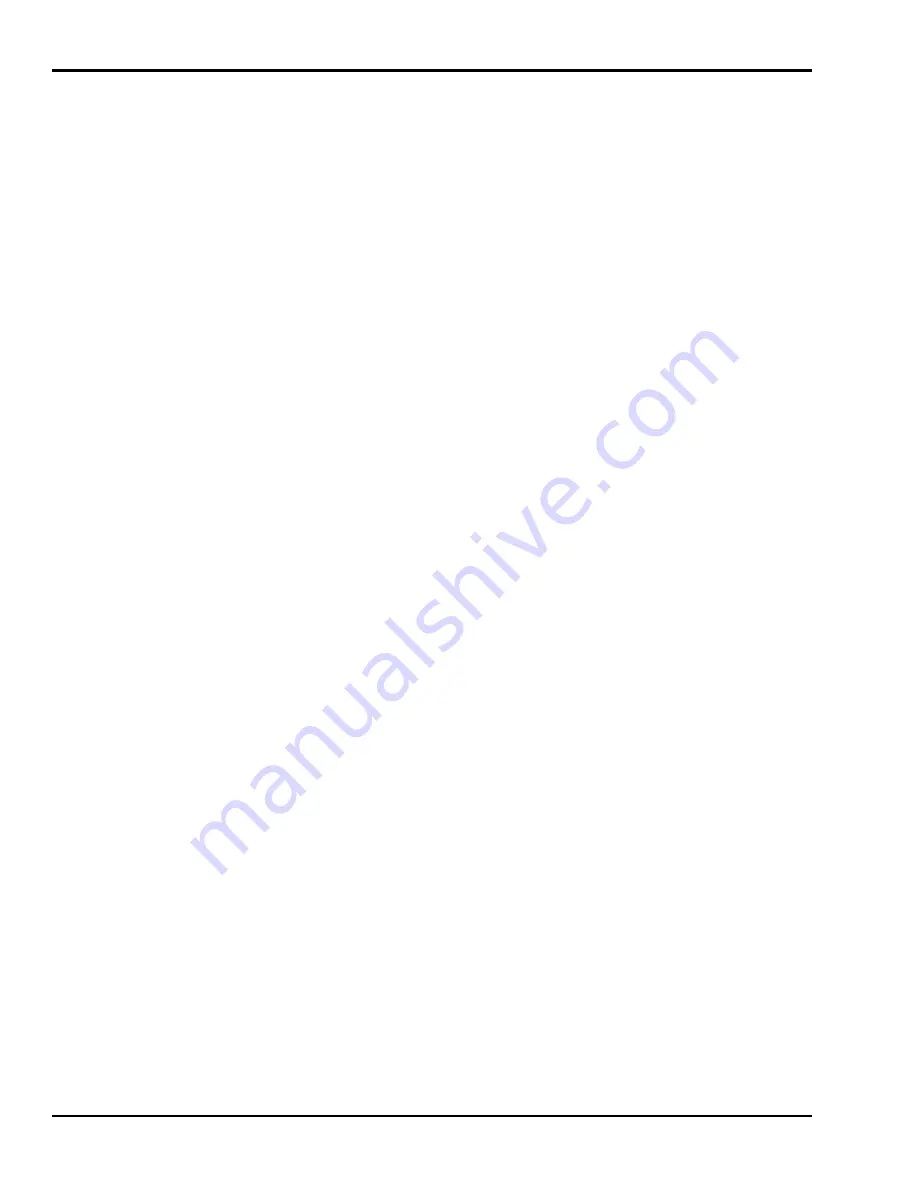
BIL-JAX 3632T
12
WARRANTY
Bil-Jax, Inc. warrants this product for one year, beginning on the date of delivery,
to be free from defects of material and workmanship provided the unit is operated
and maintained in compliance with the guidelines established in the Operations
and Maintenance Manuals. Major structural components, including trailer tongue
and boom weldments, are warranted for five years against defects due to
material or workmanship. Bil-Jax will, at its option, repair or replace any unit or
component part that fails to function properly during normal use.
The warranty does not apply if the lift and/or its components have been altered,
changed, or repaired without the consent of Bil-Jax. Repairs, damage, or defects
resulting from the following are not covered under the terms of the warranty:
negligence, misuse, accidental damage, inadequate or improper maintenance,
acts of nature, damage caused by chemicals or abrasive materials, and normal
wear and tear, such as rust or corrosion. Components not covered under this
warranty include tires, filters, covers, and routine maintenance items.
Components not manufactured by Bil-Jax are covered by their respective
manufacturer’s warranties. A list of those components and their warranties is
available upon written request to Bil-Jax.
Bil-Jax shall not in any event be liable for the cost of any special, indirect, or
consequential damages to any person, product, or thing. Bil-Jax’s maximum
liability under this warranty is limited to the amount paid to Bil-Jax for the product.
This warranty is in lieu of all other warranties expressed or implied. Bil-Jax
neither assumes nor authorizes any or other entity to assume on its behalf any
other liability in connection with the sale, rental, or use of this product.
Warranty Claims Process
In order to qualify for warranty coverage, the following conditions must be met:
1. Return of completed “Warranty Registration” form to Bil-Jax within 15 days of receipt
of product;
2. Notification to Bil-Jax within 72 hours of any claimed defect, injury, or damage
resulting from the claimed defect; and
3. Warranty is limited to parts that are determined to be defective. This does not include
parts worn out due to normal use.
4. Bil-Jax authorized dealers or distributors are responsible for filing claims
under warranty. Listed below is the warranty claims procedure.
5. Contact Bil-Jax Service Department at 800-537-0540 to report the claim and verify
warranty coverage. Machine serial number must be provided.
6. Identify the components to be claimed under warranty along with description of
failure. A Returned Merchandise Authorization (RMA) number will be issued by Bil-
Jax.
7. Replacement parts will then be sent by Bil-Jax to the dealer or distributor. All parts
are invoiced at dealer/distributor list price. Credits will be issued when defective parts
are returned to Bil-Jax and found to be defective under warranty.
8. After completing repairs, submit warranty claim form and defective parts to Bil-Jax.
Warranty claim form and parts must be received within 30 days of claim in order to be
eligible for credit. RMA number must be referenced on warranty claim form. Returned
parts are to be sent prepaid and will be credited when part is received and verified.
Warranty labor rate will be paid at current rate set by Bil-Jax. The amount of labor
hours reimbursed will be determined by Bil-Jax and will be limited to 4 hours unless
approved by Bil-Jax.
Failure to follow the warranty claims process may result in delay in processing
claim or denial of the claim. Bil-Jax reserves the right to limit or adjust warranty
claims with regard to parts, labor and travel time. Components purchased from
suppliers other than Bil-Jax are not covered under the terms of this warranty.
Summary of Contents for 3632T
Page 1: ...OPERATOR S MANUAL T 134 98 B33 01 0089 3632T ...
Page 42: ...BIL JAX 3632T 40 ...
Page 46: ...BIL JAX 3632T 44 ...