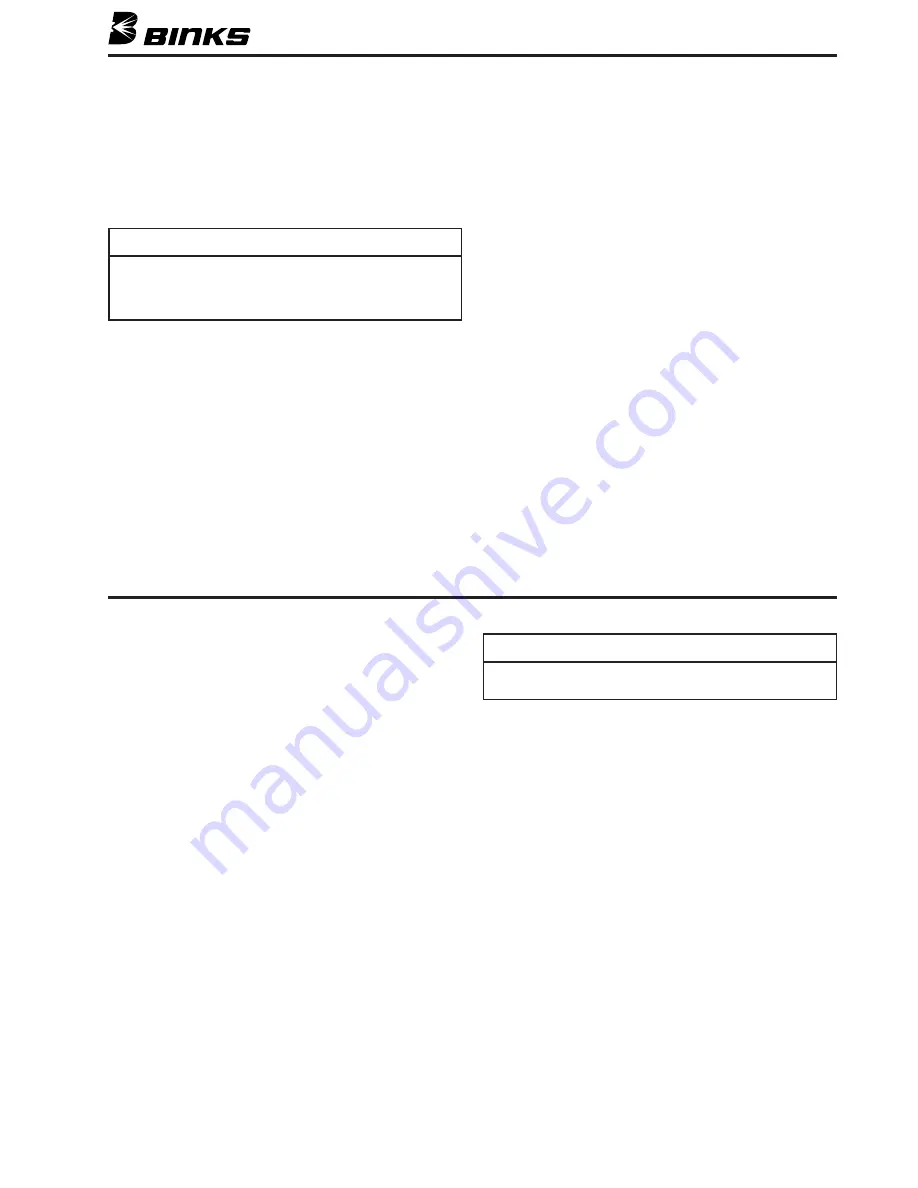
13
CLEANING THE SPRAY TIP
1. Lock the trigger (62) by rotating the locking block (68) in its
upward position.
2. Shut off pumps and air supply.
3. Release fluid pressure in entire system.
4. Unscrew air/catalyst cap retainer ring (1) and remove the air/
catalyst cap (2) and the tip assembly (5).
5. Remove the tip seal (6) from the tip body.
6. Submerge tip in solvent to remove dry or hardened material.
7. Blow air through tip from front to back to remove stuck par-
ticles. Hold tip to light to inspect orifice to assure it is clear.
CATALYST INLET/FILTER ASSEMBLY
1. Shut off pumps and air supply.
2. Bleed pressure from entire system.
3. Remove catalyst hose from gun.
4. Using a 9/16" wrench and a 7/16" wrench unscrew the
material inlet (47) from the tube assembly (43), revealing
the filter screen (45).
5. Inspect the filter screen for build-up or damage.
6. If the filter screen needs to be cleaned or replaced, unscrew
the filter support (46) with your fingers and slide the filter
screen off of it, clean or replace.
7. Inspect o-ring (44) on the tube assembly for cuts or tears and
replace if necessary.
8. Reassemble in reverse order.
OVERNIGHT SHUT-DOWN
1. Shut off pumps (in down position) and air supply.
2. Bleed pressure from entire system.
3. Remove the air/catalyst cap retainer ring (1) and remove the
air/catalyst cap (2), and the spray tip assembly (5). Inspect
the tip seal (6) and replace if worn or damaged.
4. Remove the two o-rings (7 & 8) from the grooves of the gun
head (74). Inspect o-rings for cuts or tears and replace if nec-
essary.
5. Wipe off face of the gun head with a solvent dampened rag.
6. Replace o-rings onto the front of the gun head and place the
night cap (67) onto the gun head so that the larger face of
the night cap traps the o-rings against the gun head in the
same way as the air/catalyst cap does. In many cases, lubri-
cant will provide protection for o-rings and head during
shutdown.
7. Screw the air/catalyst cap retainer ring back onto the gun
head snugly against the night cap. Do not over-tighten.
8. Clean the air/catalyst cap with solvent dampened rag or place
in solvent. Be very careful to not scratch the bottom surface
of the air/catalyst cap as this will cause it to leak catalyst into
the air passages when in service.
For Start-Up & Shut-Down details, see:
Part Sheet 77-2485 (Super Slave Units)
Part Sheet 77-2800 (Unison Units)
REPLACEMENT OF WORN PARTS
PRECAUTIONARY NOTE
Do not disassemble or work on the Binks Century gun without
first doing the following:
1. Shut off the fluid pumps and air supply.
2. Release the fluid pressure in the gun and the entire system.
3. Remove the gun from fluid hoses.
If you do not follow these steps you may injure yourself and/or
nearby personnel.
REPLACING THE CATALYST NEEDLE PACKING
1. Using two standard screwdrivers, remove the trigger stud
(60), the trigger screw (61), the trigger (62), and the chopper
trigger assembly (54).
2. Unscrew the catalyst packing nut (23) with a 3/8" wrench
and pull the catalyst needle assembly (19) straight back until
it comes out of the gun head. Be sure to pull the needle out
without bending it up or down or side to side as this will
cause the needle to bend, thus ruining the needle.
3. Clean the needle assembly so that you may be able to clear-
ly identify the packing (21).
4. The packing is the only non-metal piece of the needle
assembly and is white in color. Note its location and orien-
tation on the wire of the needle. Cut the worn packing away
with a sharp knife being sure not to scratch or deform any
nearby parts.
5. Carefully spread the new packing apart, about 3/64" at the
edge (this can be done easily with an X-acto type knife) and
press the packing onto the wire of the needle assembly in
the same location and orientation as noted in step 4. Gently
squeeze the packing closed with fingers.
6. Slide the packing forward and back with your fingers to
assure a proper fit onto the wire.
7. Reassemble in reverse order.
REPLACING THE CATALYST SEAT
1. Repeat steps 1 thru 4 from section
“Replacing the Resin Seat”
.
2. Unscrew the catalyst packing nut (23) with a 3/8" wrench
and pull the catalyst needle assembly (19) straight back until
it comes out of the gun head. Be sure to pull the needle out
without bending it up or down or side to side as this will
cause the needle to bend, thus ruining the needle.
3. Place gun head on a flat clean surface with the back of the
gun head against the surface. This will require a hole or
recess in the surface such that the alignment cone on the
back of the gun head does not rest against anything.
4. Align a 5/64" dowel pin (69) (available in Repair Kit
106-1171) with the hole in the center groove of the gun
head. Move the dowel pin straight down into the hole until
it seats against the catalyst seat (18), this will be about 3/16"
from the surface of the gun head with the three large
grooves. Press the seat out. This is most easily done on a
drill press or arbor press.
5. Now place the front of the gun head against a flat clean sur-
face such that the surface of the gun head that has the three
large grooves seats against the flat surface. (See section
“Replacing the Resin Seat”
, step 8, for the size of the hole
needed to accomplish this orientation.)
(Continued)
GENERAL MAINTENANCE
(continued)
NOTE
The cone face of the packing should point towards the
needle point of the needle assembly.
NOTE
Use care when handling the tip to avoid dropping it, or if
cleaning the tip with sharp tool be careful to avoid dam-
age. The tip is made of brittle material which is susceptible
to cracking upon contact.