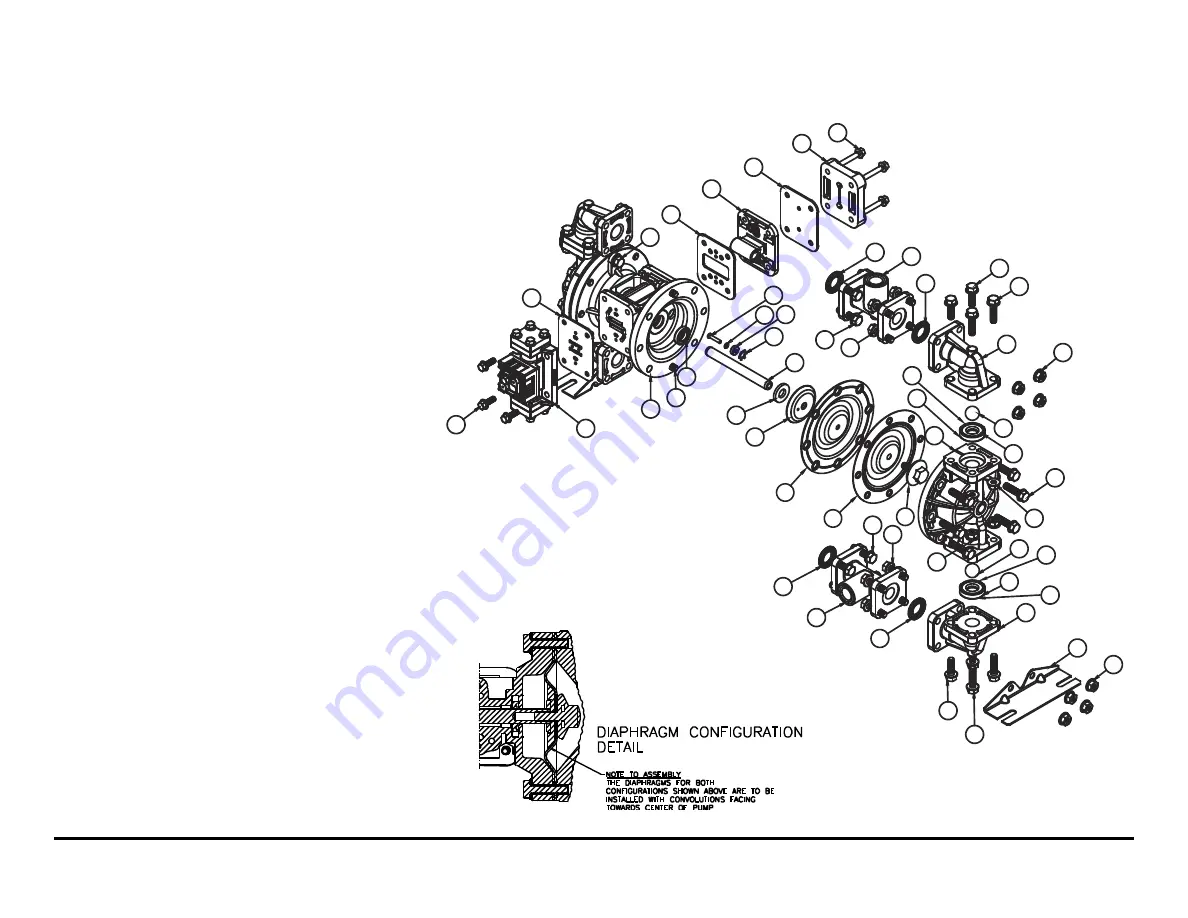
B41-818836conductiveacetal-rev0416
Model 41-818836 Conductive Acetal Ball Valve Pump Page 8
Composite Repair Parts Drawing
Available Service Kits
41-718850
AIR MOTOR REPAIR KIT
O-rings, Gaskets, Bumpers, Bushings,
Retainers, and Seals
41-718853
DIAPHRAGM KIT
Santoprene Backup Diaphragm,
PTFE Overlay Diaphragms,
PTFE Manifold O-rings, and
FEP-Encapsulated FKM O-rings for metal
check valve seats
41-718854
BALL AND SEAT KIT
316 Stainless Steel Check Balls,
316 Stainless Steel Check Valve Seats
FEP-Encapsulated FKM O-rings for metal
check valve seats
14
15
26
4
9
31
21
9
20
6
27
32
22
32
10
10
24
5
10
9
16
33
24
2
35
35
35
35
24
10
33
13
2
24
17
10
9
32
22
32
10
10
30
29
7
25
28
11
8
19
3
12
1