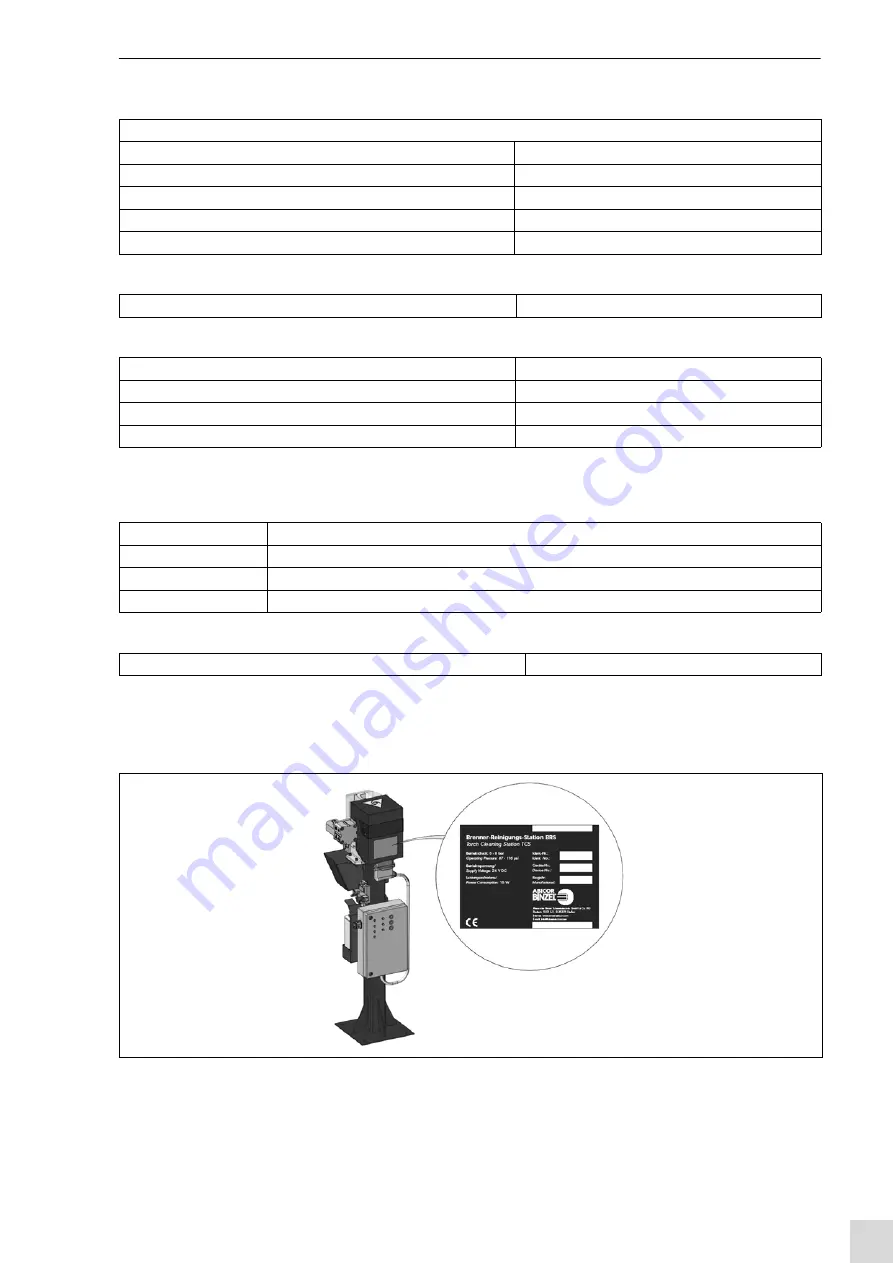
BRS-LCi SPS
3 Produktbeschreibung
DE - 9
3.2 Abkürzungen
3.3 Typenschild
Die Brennerreinigungsstation
BRS-LCi SPS
ist mit einem Typenschild am Gehäuse gekennzeichnet.
Beachten Sie für alle Rückfragen folgende Angaben:
• Gerätetyp, Identnummer, Seriennummer, Baujahr
Induktive Näherungsschalter Schließer (pnp)
Betriebsspannung
10 - 30 V DC
Zulässige Restwelligkeit
Vss < 10 %
Dauerstrom
max. 200 mA
Stromaufnahme
ca. 4 mA (24 V)
Spannungsabfall
ca. 1,2 V (200 mA)
Tab. 7
Elektrik Klemmblock
Einsprühvorrichtung
Behälterinhalt: 1 Liter
Tab. 8
Einsprühvorrichtung
Schnittleistung bei 6 bar
Massivdraht
bis 1,6 mm
Fülldraht
bis 3,2 mm
Schneidezeit
0,5 Sekunden
Tab. 9
Drahtabschneidevorrichtung DAV
BRS-LCi SPS
Brennerreinigungsstation
VI
Einsprüheinheit
DAV
Drahtabschneidevorrichtung
TCP
Werkzeugmittelpunkt (Tool Center Point)
Tab. 10
Abkürzungen und Begriffserklärung
Maßangaben in Zeichnungen oder Diagrammen
Millimeter [mm]
Tab. 11
Maße
Abb. 3
Typenschild Reinigungsstation BRS-LCi SPS
Summary of Contents for BRS-LCi SPS
Page 4: ...DE 4 1 Identifikation BRS LCi SPS ...
Page 34: ...EN 4 1 Identification BRS LCi PLC ...
Page 64: ...FR 4 1 Identification BRS LCi API ...
Page 94: ...ES 4 1 Identificación BRS LCi PLC ...
Page 123: ...BRS LCi PLC Notas ES 33 Notas ...