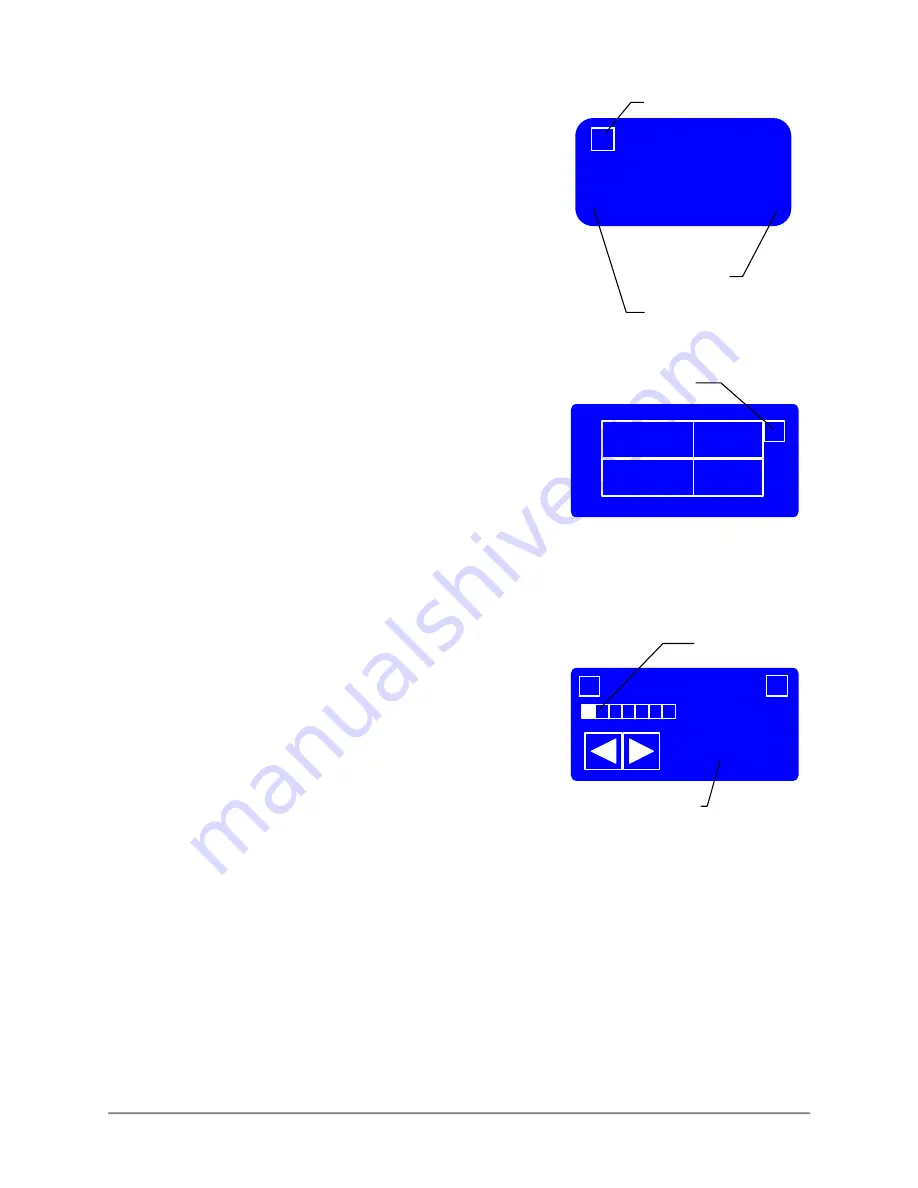
6
Software Controls - Default Screen
The Default Screen appears on the touchscreen during normal
operation. The screen shows the menu button and the heating
status of the unit.
When the unit is first powered up, “Warming” will be displayed.
When the unit reaches operating temperature, “Ready” will be
displayed as shown at the right.
If the display does not change from “Warming” to “Ready” after
45 minutes there is a problem with the unit. A qualified BKI
service representative should be contacted.
Default Screen
Software Controls - Viewing Settings
The current heater settings can be viewed by touching the Menu
Button
[M]
on the Default Screen. The Menu Screen will then be
displayed.
To view the current settings for either Well Temp or Upper Heater
touch the appropriate button on the Menu Screen. The View
Setting Screen for the selected heaters will be displayed.
To return to the Default Screen, touch the Exit Button
[X]
.
If the controller is configured to control each well position
independently the View Setting Screen as shown at right will be
displayed. Use the left and right arrows to display the heater
setting for the various well positions of the unit. The progress bar
gives a visual representation of the well location for which the
setting is being displayed.
The current heater setting is displayed on the right side of the
screen. The setting is a numeric value between 1 and 10 where
10 is the hottest setting.
If the controller is configured to control all of the well positions at
the same setting, the progress bar will be solid and the left and
right arrows will not be displayed. The setting shown will be for
the heaters at all of the well positions.
To return to the Menu Screen, touch the Menu Button
[M]
. To
return to the Default Screen, touch the Exit Button
[X]
.
Touching
[Set Clock]
on the Menu Screen will display the time
and date. To return to the Menu Screen, touch the Menu Button
[M]
. To return to the Default Screen, touch the Exit Button
[X]
.
SET WELL
TEMP
SET UPPER
HEATER
SET
CLOCK
SAVE
TEMPS
X
Menu Screen
Well Heater 1
3
X
M
View Setting Screen
Software Controls - Programming the
Ready
M
Lower Right
Lower Left
Menu Button
Exit Button
Progress Bar
Current Setting
Summary of Contents for WDCG Series
Page 1: ...Series WDCG Operation Manual Hot Case Series ...
Page 22: ...20 Wiring Diagrams ...
Page 23: ...21 ...
Page 24: ...22 ...
Page 25: ...23 ...
Page 26: ...24 ...
Page 27: ...25 ...
Page 28: ...26 ...
Page 29: ...27 ...
Page 30: ...28 ...
Page 31: ...29 ...
Page 32: ...30 ...
Page 33: ...31 ...
Page 34: ...32 ...
Page 35: ...33 ...
Page 36: ...34 ...