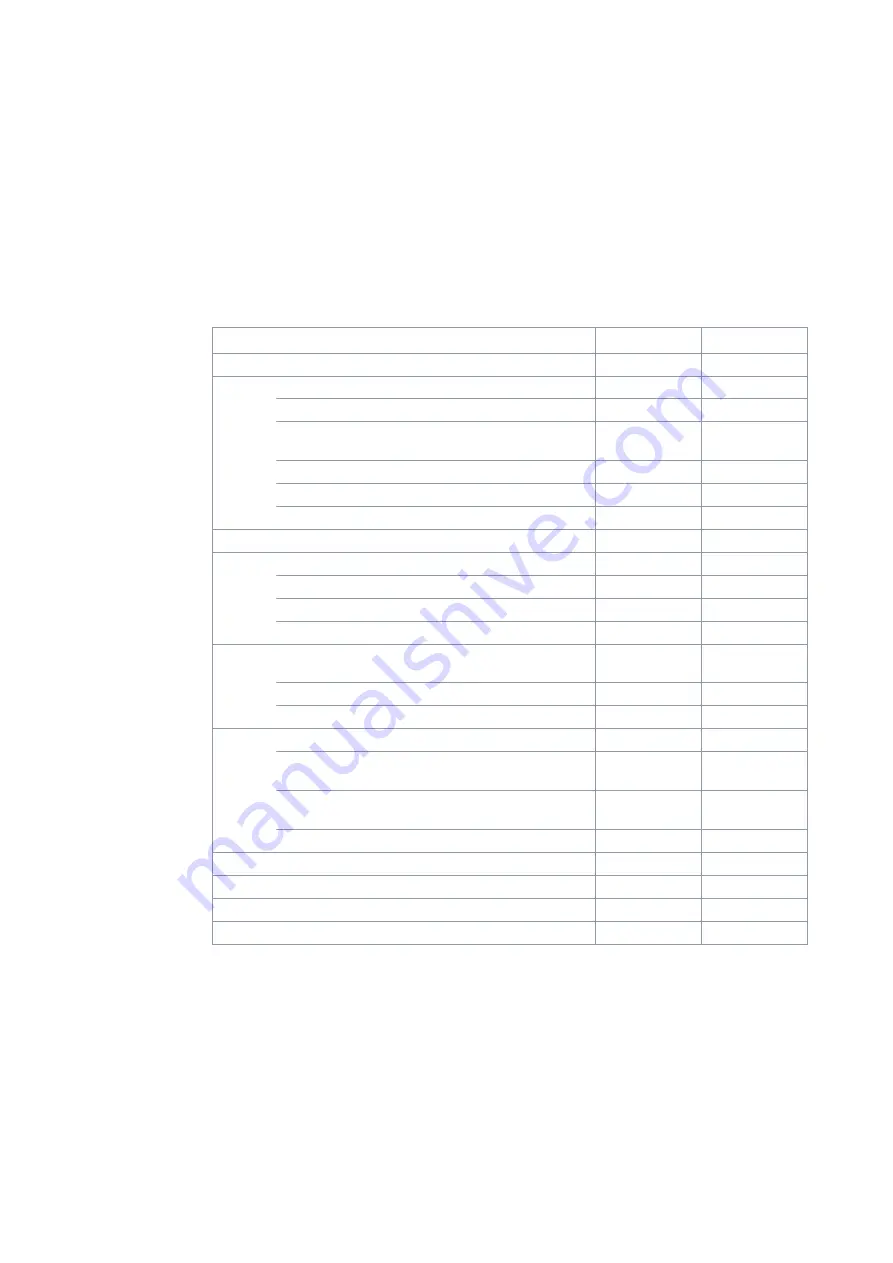
Control system
Model series of the control system
The table that follows shows the differences between the two control system models,
CTR101 and CTR201.
The CTR201 control system can use the vehicle speed and direction information
through the tractor ISOBUS implement-connector to control the driving functions.
CTR101
CTR201
Connection to tractor ISOBUS implement-connector
-
●
Drive activation functions:
Automatic, when the tractor starts to move
-
●
Automatic, when the system goes back to the
working speed range
-
●
Manual drive activation
●
●
Automatic drive direction selection (ISOBUS)
-
●
Manual drive direction selection
●
●
*M)
Tractive power cut-off during braking
●
●
Switching to freewheeling:
Automatic, based on low pressure
●
●
Automatic, based on speed (ISOBUS)
-
●
Manual freewheeling
●
●
Shifting between low and high-speed range (2-speed
function):
Manual shift
●
●
*M)
Automatic shift
-
●
Assisting traction control modes (ATC):
Automatic mode, activation and deactivation
based on speed
-
●
Activated after forward drive activation for a set
time
●
-
Continuous operation
●
●
4WD valve control
O
O
HDC valve control
*)
●
●
Auxiliary valve output function
*)
●
●
External alarm input
*)
●
●
- = not available,
●
= available, O = option
M)
Available when you operate the CTR201 in the manual mode.
*)
Refer to the “Control system connections” for the necessary cables (see chapters
HDC / AUX valve cable (optional accessory)
AUX valve (optional accessory)
on page 26 and
External alarm input cable (optional
on page 27).
5
5.1
Control system
18
Product manual