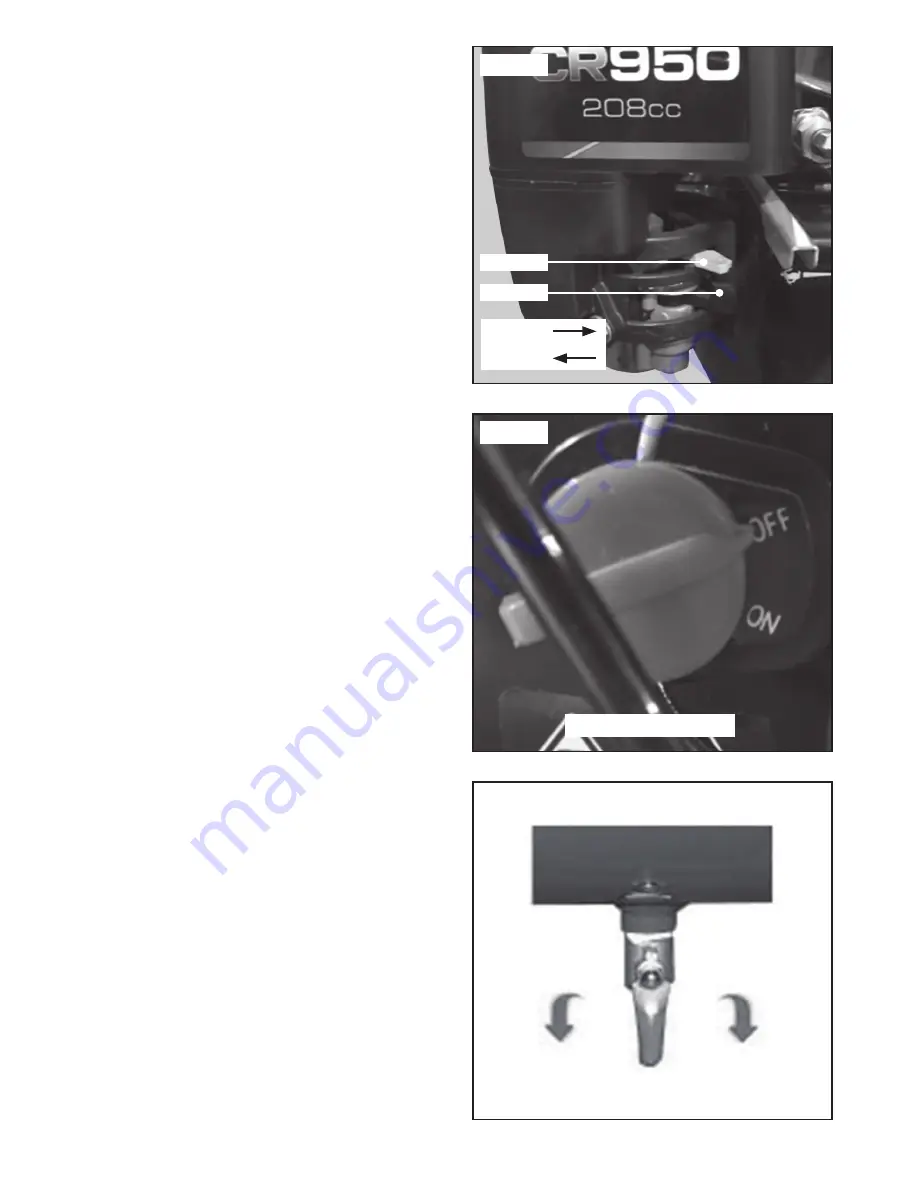
18
USING YOUR AIR COMPRESSOR
With your Briggs and Stratton engine running, you can now
start using your air compressor.
To use you air compressor;
1. Close the unloading valve, Pic. 14, rotate the silver
aluminium lever so that it is hanging down “loose”. This
will allow the pump to start filling your tank.
2. Allow the tank to fill completely.
3. Once the tank is full (115PSI/8Bar) the Briggs and
Stratton engine will slow to an idle.
4. You can now start using your air tools. See the
“Connecting Air Tools” section, for information on how to
attach your air hose and tool.
NOTE: Your Briggs and Stratton engine will automatically
go to full speed once the tank pressure drops to about
85PSI/6Bar.
Once the tank is full (115PSI/8Bar) the Briggs and Stratton
engine will slow to an idle.
This will continue automatically until you turn the engine
OFF.
Stopping Your Air Compressor
To stop your Briggs and Stratton powered air compressor;
1. Turn the fuel tap lever OFF, Pic. 15, this moves to the left.
2. Turn the engine switch to OFF, Pic, 16, this rotates up.
3. Open the drain valve, Pic. 17.
Connecting Air Tools
This Briggs and Stratton powered air compressor has a
maximum pressure of 8 bar. Always regulate the outlet air
pressure to match your air tool. Different air tools require
different operating pressures. Always check with the tool
manufacturer if unsure.
The configuration of tools and accessories can be varied to
suit your particular requirements. A basic recommended set
up is shown in Pic.18.
When connecting your air hose and or air tool:
1. Lift up the regulator cap and turn anti-clockwise.
2. This will reduce the, outlet pressure, continue winding
anti-clockwise till the outlet pressure gauge is showing
0PSI/0Bar. This will allow easy connection.
3. Connect your air hose the longer the air hose the better.
4. Connect your air tool.
a. Always check your air tool manual to find out the tools
recommended operating pressure.
5. To adjust the pressure turn regulator cap clockwise.
6. This will increase the, outlet pressure, continue winding
clockwise till the outlet pressure gauge is showing the
correct pressure for the selected tool.
7. Push regulator cap down to ensure it does not change
position with vibration.
PIC. 15
Choke lever
Fuel lever
Choke OFF
Fuel OFF
PIC. 16
Turn engine switch to OFF
PIC. 17
Open drain valve, lever pointing to the ground