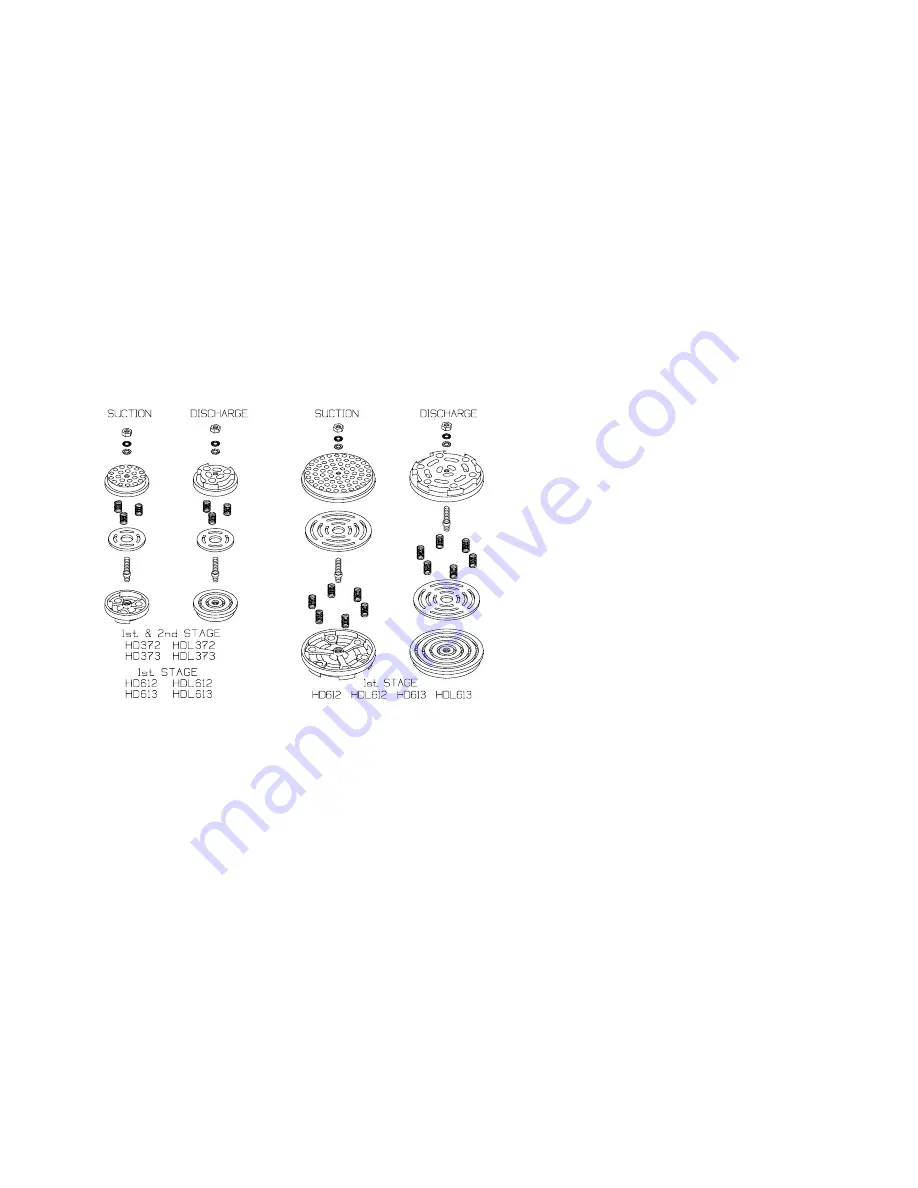
CB-9A-040 page 16
MAINTENANCE
VALVE REPLACEMENT
(sizes 372, 373, 612 and 613)
1.
Remove the valve cap (or unloader assembly) and O-ring from each valve.
2.
Remove
the valve hold down screw with a spanner wrench (such as Blackmer PN 790535).
3.
Valve Removal and Disassembly
a.
Remove the valve cover plate capscrews then lift off the cover plate and O-ring.
b.
Remove the valve cage (and unloader plunger).
c.
Remove the valve assembly and the valve gasket.
d.
Inspect the valve for wear or breakage.
e.
Valve
Repair
1
Remove hex nut from valve (after removing the unloader actuator retaining ring, the actuator,
spring, and post.)
2
Separate the valve halves and remove springs and plate.
3
Inspect and replace worn components.
4
Reassemble valves as shown in the drawing and tighten the valve assembly nut according to
the Bolt Torque Table.
5
(Reassemble the unloader post, spring, actuator and retainer ring.)
Typical Valve Assemblies
4.
To reinstall valves:
a.
Install a new valve gasket into the cylinder head (remove any old gaskets).
b.
Install the valve assembly in the cylinder head. Make sure the valve's orientation and location are
correct.
c.
Center the valve cage on the valve assembly.
d.
Applies only to suction valves with unloaders.
Install the unloader plunger in the cage.
e.
Make sure the valve hold down screw is removed from the cover plate, then install the valve cover
plate with a new O-ring. Tighten the cover plate capscrews according to the Bolt Torque Table.
f.
Install the hold down screw and tighten according to the Bolt Torque Table.
g.
Install the valve cap (or unloader assembly) and O-ring. (A little oil or grease on the O-ring will help
hold it in place during installation.)
5.
After replacing the valves, rotate the flywheel by hand to check for interference between the pistons and
the valves.
6.
After 60 minutes of running time, remove the valve cap (or unloader assembly) and retorque the hold
down screw. Replace the valve cap and O-ring.
Summary of Contents for HD172A
Page 23: ...CB 9A 040 page 23 NOTES...