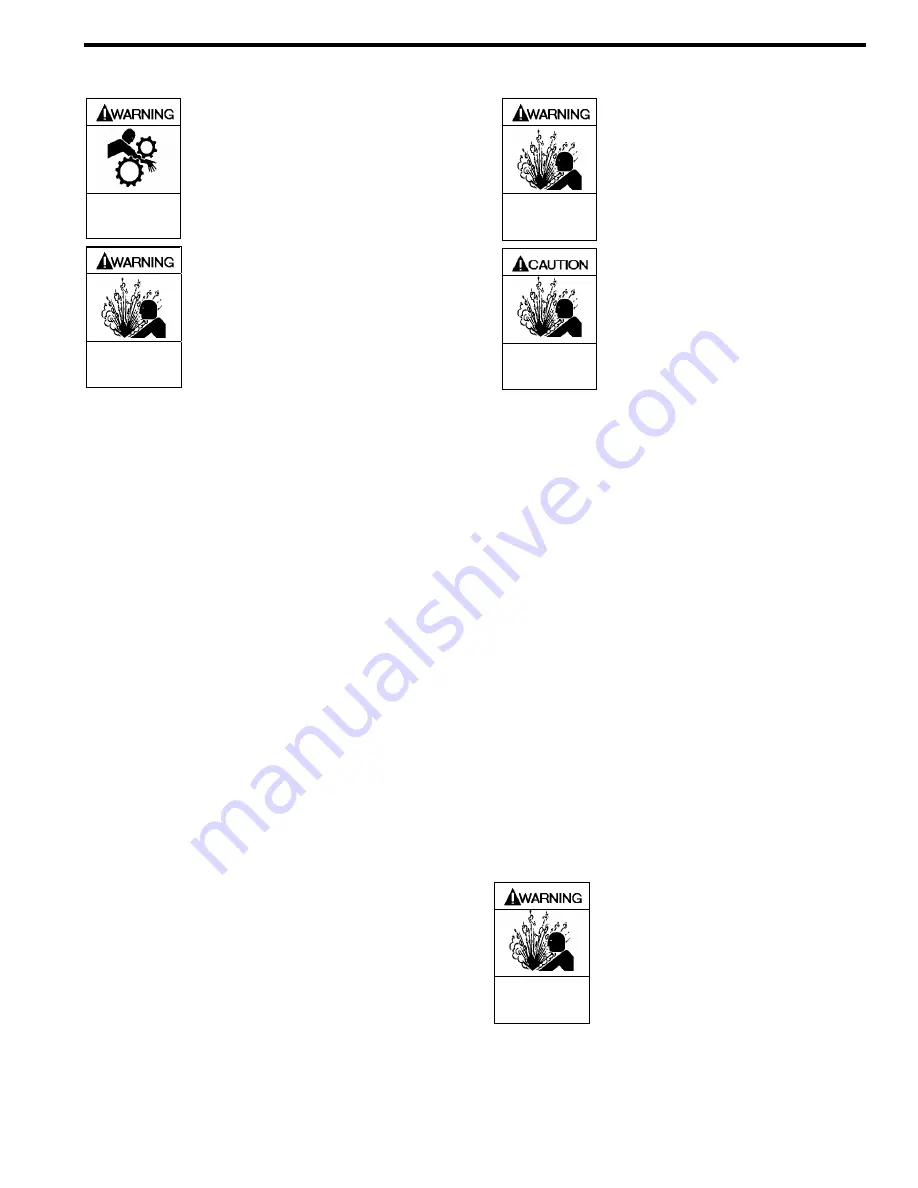
501-F00 Page 5/12
OPERATION
Do not operate
without guard
in place
OPERATION WITHOUT GUARDS IN
PLACE CAN CAUSE SERIOUS
PERSONAL INJURY, MAJOR
PROPERTY DAMAGE, OR DEATH.
Hazardous pressure
can cause serious
personal injury or
property damage
FAILURE TO RELIEVE SYSTEM
PRESSURE PRIOR TO PERFORMING
PUMP SERVICE CAN CAUSE SERIOUS
PERSONAL INJURY OR PROPERTY
DAMAGE.
SYSTEMS WITH METERS
WILL STILL BE PRESSURIZED EVEN
AFTER THE HOSE IS EMPTIED
Hazardous pressure
can cause serious
personal injury or
property damage
DISCONNECTING FLUID OR PRESSURE
CONTAINMENT COMPONENTS DURING
PUMP OPERATION CAN CAUSE
SERIOUS PERSONAL INJURY OR
PROPERTY DAMAGE.
Hazardous pressure
can cause personal
injury or property
damage
PUMPS OPERATING AGAINST A
CLOSED VALVE CAN CAUSE SYSTEM
FAILURE, PERSONAL INJURY AND
PROPERTY DAMAGE
PRE-START UP CHECK LIST
1. Check the alignment of the pipes to the pump. Pipes
should be supported so that they do not spring away or
drop down when pump flanges or union joints are
disconnected.
2. Check the entire pumping system to verify that the proper
inlet and discharge valves are fully open, and that the
drain valves and other auxiliary valves are closed.
3. Install suction and discharge pressure gauges on the
pump in the threaded connections provided. These can
be used to check actual suction and discharge conditions
after pump start-up.
4. Check the wiring of the motor.
5. Briefly start the pump to verify proper rotation direction.
START UP PROCEDURES
NOTICE:
CONSULT THE "GENERAL PUMP TROUBLESHOOTING"
SECTION OF THIS MANUAL IF DIFFICULTIES DURING
START UP ARE EXPERIENCED.
1. SLOWLY build pressure in the pump.
2. Start the pump. Priming should occur within one minute.
3. Check the suction and discharge pressure gauges to see
if the pump is operating within the expected conditions.
4. Check for leakage from the piping and equipment.
5. Check for excessive noise, vibration or overheating of the
pump, reducer, and motor.
6. If possible, check the flow rate.
7. With the manual valve in the bypass line OPEN, check
the
pressure setting of the relief valve by slowly closing a
valve
in the discharge line and reading the pressure
gauge. As
the valve in the discharge line is closed, the
pump
discharge pressure will rise to a maximum value,
then drop
back slightly. Use the maximum pressure to
determine the
valve setting. This pressure should be 10 -
20 psi (0.7 -1.4
bar) higher than the maximum system
operating
pressure. If adjustments need to be made,
refer to the
"Relief Valve Setting and Adjustment" section
of this
manual.
8. The external bypass valve must be set at least 25 psi
(1.7 bar) lower than the internal pump relief valve. NOTE:
The normal operating pressure must be at least 5 - 15 psi
(0.3 -1.0 bar) less than the external bypass valve setting.
NOTE:
If the pump is operated with both the discharge
line
and bypass line closed, the pump will recirculate fluid
through
the internal relief valve, causing cavitation and
excessive
wear on the pump. The pressure gauge may
also read lower
than with normal operation.
RELIEF VALVE SETTING AND
ADJUSTMENT
The relief valve pressure setting is marked on a metal tag
attached to the valve cover. Generally, the relief valve should
be set at least 10 - 20 psi (0.7 - 1.4 Bar) higher than the
operating pressure, or the external bypass valve setting.
DO NOT adjust the relief valve pressure setting while the
pump is in operation.
1.
To INCREASE the pressure setting,
Loosen the locknut,
and turn the adjusting screw
inwar
d, or clockwise.
Retighten the locknut
2.
To DECREASE the pressure settin
g, Loosen the
locknut, and turn the adjusting screw
outwar
d, or
counterclockwise. Retighten the locknut
Hazardous pressure
can cause serious
personal injury or
property damage
INCORRECT SETTINGS OF THE
PRESSURE RELIEF VALVE CAN CAUSE
PUMP COMPONENT FAILURE,
PERSONAL INJURY, AND PROPERTY
DAMAGE.
Summary of Contents for LDF1A
Page 11: ...501 F00 Page 11 12 NOTES ...