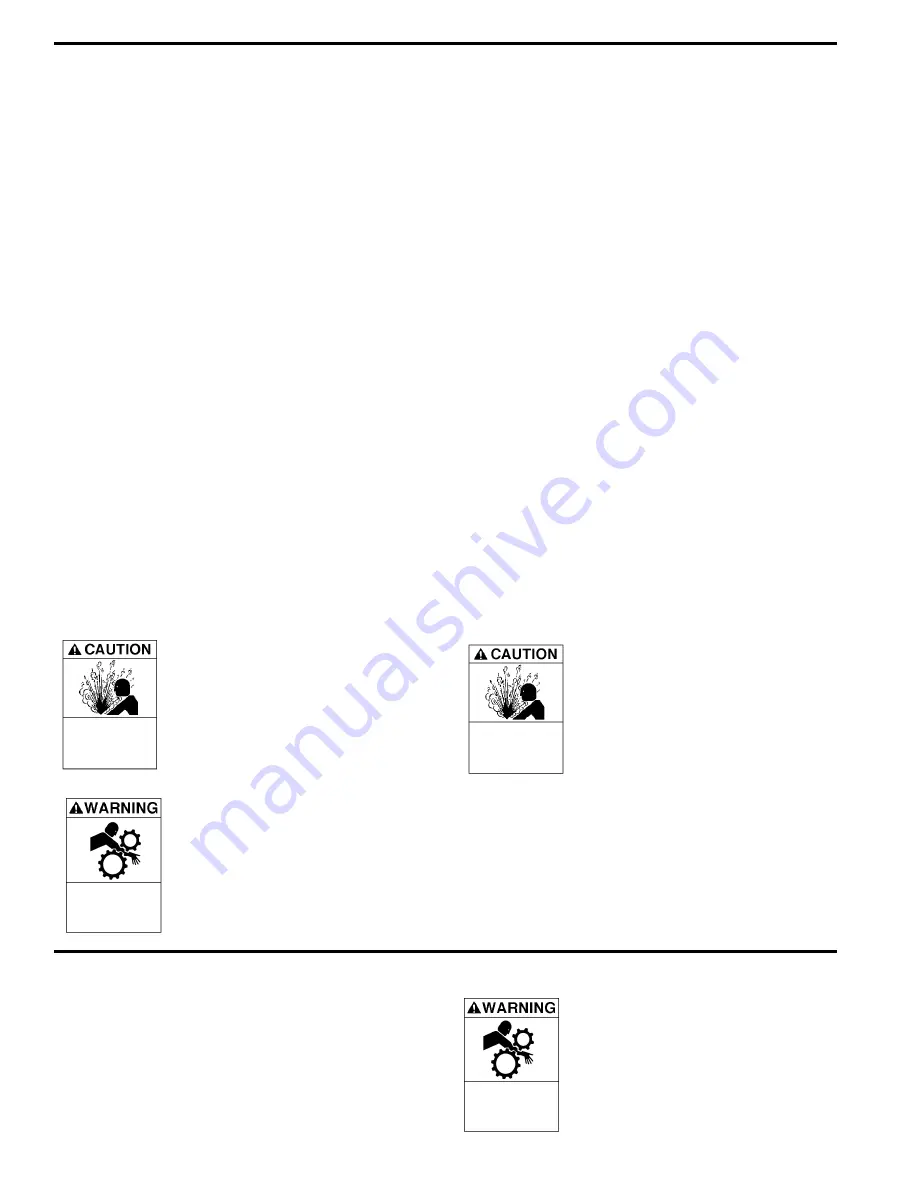
4
PUMP ROTATION
NOTICE:
CONFIRM CORRECT PUMP ROTATION BY CHECKING THE
PUMP ROTATION ARROWS RESPECTIVE TO PUMP DRIVER
ROTATION.
TO CHANGE PUMP ROTATION
To reverse pump rotation, remove both bearing covers (27,
27A) and locknuts/lockwashers (24A, 24B). Remove the
outboard head (20) and reverse the rotor and shaft (13). The
vanes (14) must also be reversed so that the relief grooves
face in the direction of rotation. Refer to “Pump Disassembly”
and “Pump Assembly” sections of this manual for parts
removal and replacement instructions.
OPERATING PUMP AGAINST A
CLOSED VALVE CAN CAUSE
SYSTEM COMPONENT FAILURE,
PERSONAL INJURY AND PROPERTY
DAMAGE.
Hazardous pressure
can cause personal
injury or property
damage.
PRE-START UP CHECK LIST
1. Inspect complete piping system and supports to ensure
that no piping loads are being placed on the pump.
2. Install pressure gauges in the
1
/
4
" NPT intake and
discharge ports located on the pump casing to check pump
performance after start-up.
3. Ensure all valves and fittings in piping system are in the
start-up or operating positions.
4. Jog the pump motor to verify proper pump rotation.
START UP PROCEDURES
NOTICE:
CONSULT THE "GENERAL PUMP TROUBLESHOOTING"
SECTION OF THIS MANUAL IF DIFFICULTIES DURING START
UP ARE EXPERIENCED.
OPERATION
1. Start the motor. Priming should occur within one minute.
2. Check the pressure gauges to ensure the system is
operating within expected parameters. Record the gauge
readings in the "Initial Start Up Information" section of this
manual for future reference.
3. Inspect piping, fittings, and associated system equipment
for leaks, noise, vibration and overheating.
4. Check the flow rate to ensure the pump is operating within
the expected parameters. Record flow rate in the “Initial
Start Up” section of this manual.
5. Close the discharge valve and check the differential
pressure across the pump. It should not exceed the
pressure setting of the external bypass valve.
6. With the discharge valve still closed, momentarily close the
manual shut-off valve in the bypass return line to check the
pump relief valve. The pressure should be at least 25 psi
(1.7 bar) higher than the maximum system operating
pressure or the system pressure control valve setting. If
adjustments need to be made, refer to “Relief Valve Setting
and Adjustment” section of this manual.
7. The external bypass valve must always be set at least 25
psi (1.7 bar) lower than the internal pump relief valve.
NOTE: The normal operating pressure should be at least 5
- 15 psi (0.3 -1.0 bar) less than the external bypass setting.
Pump speeds which result in higher pressures (nearing the
valve setting) forces the liquid to be recirculated, creating
excessive wear on the pump and equipment.
RELIEF VALVE SETTING AND ADJUSTMENT
The factory relief valve pressure setting is marked on a metal
tag attached to the valve cover. It is recommended the relief
valve be set at least 25 psi (1.7 bar) higher than the maximum
system operating pressure or the system pressure control
valve setting.
Hazardous pressure
can cause personal
injury or property
damage.
I
NCORRECT SETTINGS OF THE
PRESSURE RELIEF VALVE CAN CAUSE
SYSTEM COMPONENT FAILURE,
PERSONAL INJURY AND PROPERTY
DAMAGE.
Relief Valve Adjustment Procedure:
1.
To INCREASE the pressure setting
, remove the relief
valve cap (1), loosen the locknut (3), and turn the adjusting
screw (2) inward, or CLOCKWISE.
2.
To DECREASE the pressure setting
, remove the relief
valve cap (1), loosen the locknut (3), and turn the adjusting
screw (2) outward, or COUNTERCLOCKWISE.
Refer to corresponding Blackmer Pump Parts List for
relief valve spring pressure ranges.
NOTICE:
MAINTENANCE SHALL BE PERFORMED BY QUALIFIED
TECHNICIANS ONLY, FOLLOWING THE APPROPRIATE
PROCEDURES AND WARNINGS AS PRESENTED IN
THIS MANUAL.
MAINTENANCE
Hazardous
machinery can
cause serious
personal injury.
FAILURE TO DISCONNECT AND
LOCKOUT ELECTRICAL POWER
BEFORE ATTEMPTING MAINTENANCE
CAN CAUSE SERIOUS PERSONAL
INJURY OR DEATH.
Hazardous
machinery can
cause serious
personal injury.
OPERATION WITHOUT GUARDS IN
PLACE CAN CAUSE SERIOUS
PERSONAL INJURY, PROPERTY
DAMAGE OR DEATH.