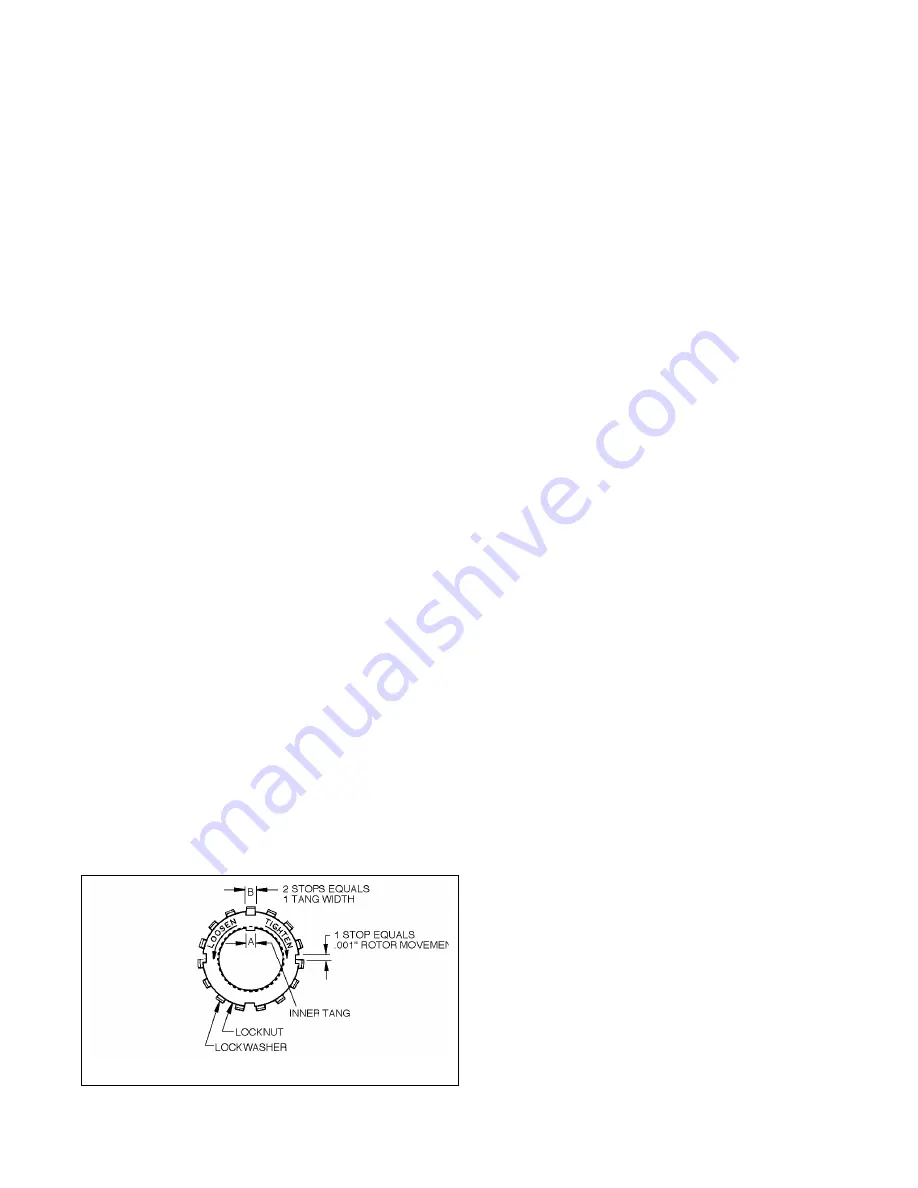
MAINTENANCE
7
8.
MECHANICAL SEAL INSTALLATION
Rotating Assembly -
a. Apply a small amount of motor oil on the shaft between
the shaft threads and the rotor.
b. Slide the seal jacket assembly (153C) over the shaft
and into the disc cavity with the drive tangs of the jacket
towards the rotor. Rotate the jacket assembly to
engage the drive tangs in the rotor slots.
c. Install a new rotating O-ring (153E) in the rotating seal
face (153B). Align and insert the rotating assembly into
the the seal jacket with the polished face outward.
Clean the polished face with a clean tissue and alcohol.
Stationary Seat -
a. Apply a small amount of motor oil in the seal recess of
the head (20).
b. Install a new stationary O-ring (153D) in the stationary
seat (153A). Clean the polished face with a clean
tissue and alcohol. Align the pin in the stationary seat
with the slot in the head recess and push the seat fully
into the seal recess with the polished face outward.
9. Carefully install the inboard head assembly (20) over the
shaft. Do not contact the end of the shaft with the polished
face of the stationary seat. Center the head on the pump
casing (12). Install and uniformly tighten four head
capscrews (21) 90
o
apart, torquing to 30 lbs ft (47 Nm).
NOTE: It is a good practice to attach pump heads to
the same ends they were removed from.
10. Hand pack the ball bearing (24) with grease. Refer to the
"Lubrication" section for the recommended grease.
11. Install the bearing (24) into the head recess. The bearing
balls should face outward, with the grease shield inward.
The bearing must be fully and squarely seated in the head
(20).
12. Turn the pump casing around and remove the outboard
head (20) previously installed.
13. Install the outboard head (20), mechanical seal (153) and
bearing (24) as instructed in steps 6 through 11.
14. Rotate the shaft by hand to engage the mechanical seal
drive tangs, and to test for binding or tight spots. If the
rotor does not turn freely, lightly tap the rims of the heads
(20) with a soft faced mallet until the correct position is
found. Install all of the remaining head capscrews (21) for
each head and uniformly torque to 30 lbs ft (47 Nm).
16.
LOCKNUT ADJUSTMENT
It is important that the bearing locknuts (24A) and
lockwashers (24B) be installed and adjusted properly.
Overtightening locknuts can cause bearing failure or a
broken lockwasher tang. Loose locknuts will allow the rotor
to shift against the discs (71), causing wear. See Figure 6.
a. On both ends of the pump shaft, install a lockwasher
(24B) with the tangs facing outward, followed by a
locknut (24A) with the tapered end inward. Ensure the
inner tang "A" of the lockwasher is located in the slot in
the shaft threads, bending it slightly, if necessary.
b. Tighten both locknuts (24B) to ensure that the bearings
(24) are bottomed in the head recess. DO NOT
overtighten and bend or shear the lockwasher inner
tang.
c. Loosen both locknuts (24A) one complete turn.
d. Tighten one locknut (24A) until a slight rotor drag is felt
when turning the shaft by hand.
e. Back off the nut the width of one lockwasher tang "B".
Secure the nut by bending the closest aligned
lockwasher tang into the slot in the locknut. The pump
should turn freely when rotated by hand.
f. Tighten the opposite locknut (24A) by hand until it is
snug against the bearing (24). Then, using a spanner
wrench, tighten the nut the width of one lockwasher
tang. Tighten just past the desired tang, then back off
the nut to align the tang with the locknut slot. Secure
the nut by bending the aligned lockwasher tang into the
slot in the locknut. The pump should continue to turn
freely when rotated by hand.
g. To check adjustment, grasp the nut and washer with
fingers and rotate back and forth. If this cannot be
done, one or both locknuts are too tight and should be
alternately loosened one stop at a time (.001" - 25
microns). Begin by loosening the locknut (24A)
adjusted last.
16. Inspect the grease seal (104) for wear or damage and
replace as required. Grease the outside diameter of the
grease seal and push it into the inboard bearing cover (27)
or bracket mount (108) with the lip of the seal inward
(towards the pump).
17. Attach a new bearing cover gasket (26) and the inboard
bearing cover (27) to the inboard head (20). Install the
outboard bearing cover (27A) and a new gasket to the
outboard head. Make sure the grease fittings (76) on the
bearing covers are accessible. Install and torque the
bearing cover capscrews (28) to 30 lbs ft (47 Nm).
18. On flange mounted pumps, the bracket mount takes the
place of the inboard bearing cover (27). To attach the
bracket mount to the head, install a new bearing cover
gasket (26) and the four mounting screws (28A).
19. Reinstall coupling, shaft key, and coupling guards.
20. Refer to “Pre-Start Up Check List” and “Start Up
Procedures” sections of this manual prior to restarting
pump operation.
Figure 6 - Locknut Adjustment