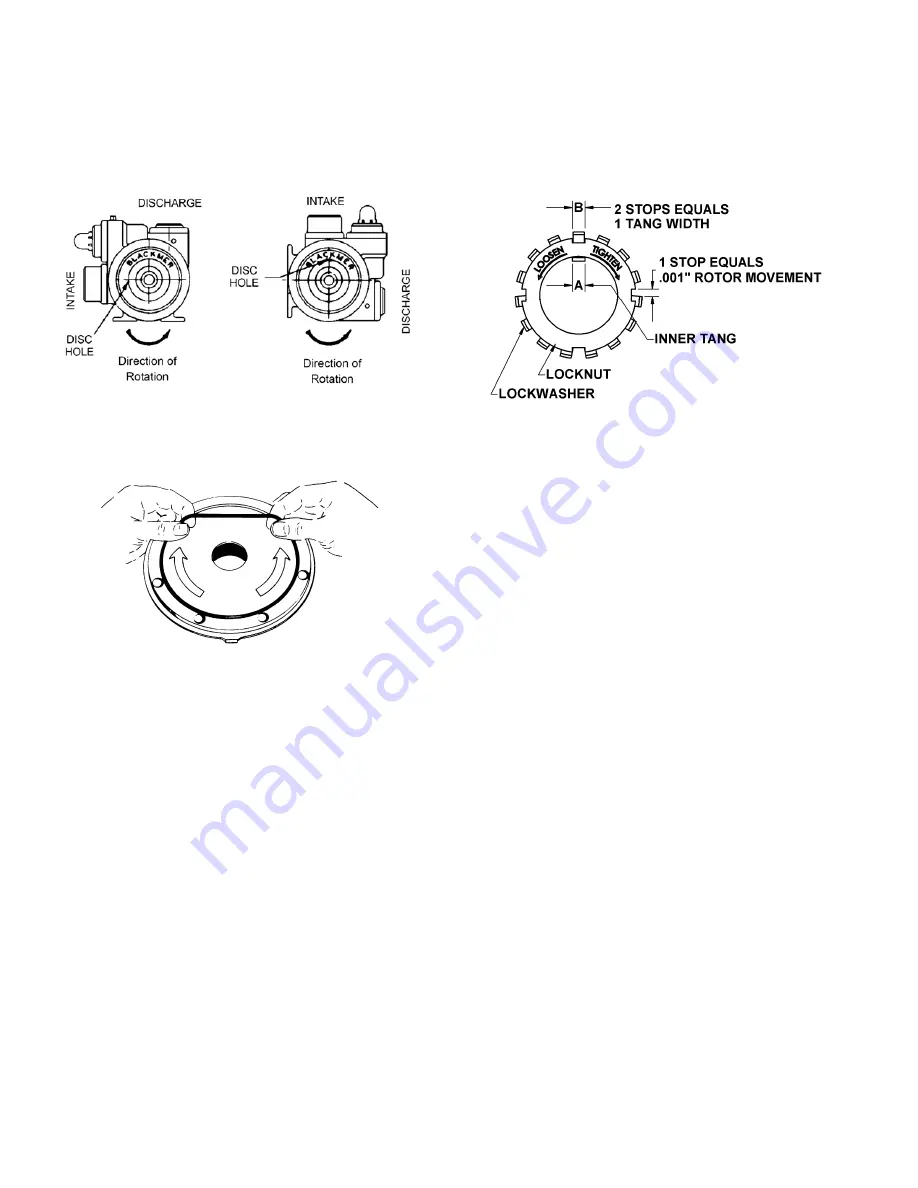
107-B00 Page 10/16
MAINTENANCE
f.
Position the disc relief hole so that when the head is
mounted on the pump with the “Blackmer” name in
an upright position, the disc hole will be towards the
INTAKE side of the pump. See Figure 7.
g.
Install the disc machine screws (71A) and
lockwashers (71B).
Figure 7 – Disc Relief Hole Location (4-inch Models)
10. Install a new head O-ring (72) in the groove on the inside
face of the head. Lay the O-ring flat and start in on one
side of the groove, stretching ahead with the fingers, as
shown in Figure 8.
Figure 8 – Head O-Ring Installation
11. Carefully install the head assembly (20) over the shaft.
Do not contact the end of the shaft with the mechanical
seal. Position the head with the small weep hole towards
the bottom of the pump. Install and partially tighten four
head capscrews (21) 90° apart. The remaining capscrews
will be installed in step 18.
On 4-inch models, make sure the head is mounted with
the “Blackmer” name upright and the disc relief hole
towards the intake side of the pump. The seal jacket drive
tangs must be engaged in the rotor slots.
12. Hand pack the ball bearing (24) with grease. Refer to the
"Lubrication" section for the recommended grease.
13. Install the bearing into the head recess. The bearing balls
should face outward, with the grease shield inward. The
bearing must be fully and squarely seated in the head.
14. Turn the pump casing around and remove the outboard
head and disc previously installed.
15. Install the mechanical seal and disc in the outboard head
as instructed in steps 7 through 8 for the 2 and 3-inch
models or step 9 for the 4-inch models.
16. Finish assembling the outboard side of the pump as
instructed in steps 10 through 13.
17. Rotate the shaft by hand to engage the mechanical seal
drive tangs, and to test for binding or tight spots. If the
rotor does not turn freely, lightly tap the rims of the heads
with a soft faced mallet until the correct position is found.
18. Install and partially tighten the remaining head capscrews
19. Uniformly torque the head capscrews to 30 lbs ft (40.7
Nm), alternating between one side of the head and the
other. Frequently check that the shaft still turns freely. If
tight, loosen the capscrews and repeat the procedure. If
the shaft continues to bind, check for grease or dirt on the
mechanical seal faces.
Figure 9 – Locknut Assembly
20. LOCKNUT ADJUSTMENT
It is important that the bearing locknuts (24A) and
lockwashers (24B) be installed and adjusted properly.
Overtightening locknuts can cause bearing failure or a
broken lockwasher tang. Loose locknuts will allow the
rotor to shift against the discs, causing wear. See Fig. 9.
a. On both ends of the pump shaft, install a lockwasher
(24B) with the tangs facing outward, followed by a
locknut (24A) with the tapered end inward. Ensure the
inner tang "A" of the lockwasher is located in the slot
in the shaft threads, bending it slightly, if necessary.
b. Tighten both locknuts to ensure that the bearings are
bottomed in the head recess. DO NOT overtighten
and bend or shear the lockwasher inner tang.
c. Loosen both locknuts one complete turn.
d. Tighten one locknut until a slight rotor drag is felt
when turning the shaft by hand.
e. Back off the nut the width of one lockwasher tang "B".
Secure the nut by bending the closest aligned
lockwasher tang into the slot in the locknut. The pump
should turn freely when rotated by hand.
f. Tighten the opposite locknut by hand until it is snug
against the bearing. Then, using a spanner wrench,
tighten the nut the width of one lockwasher tang “B”.
Tighten just past the desired tang, then back off the
nut to align the tang with the locknut slot. Secure the
nut by bending the aligned lockwasher tang into the
slot in the locknut. The pump should continue to turn
freely when rotated by hand.
g. To check adjustment, grasp the nut and washer with
fingers and rotate back and forth. If this cannot be
done, one or both locknuts are too tight and should be
alternately loosened one stop at a time 0.001"
(0.025mm). Begin by loosening the locknut adjusted
last.
21. Inspect the grease seal (104) for wear or damage and
replace as required. Grease the outside diameter of the
grease seal and push it into the inboard bearing cover
(27A) with the lip of the seal inward (towards the pump).