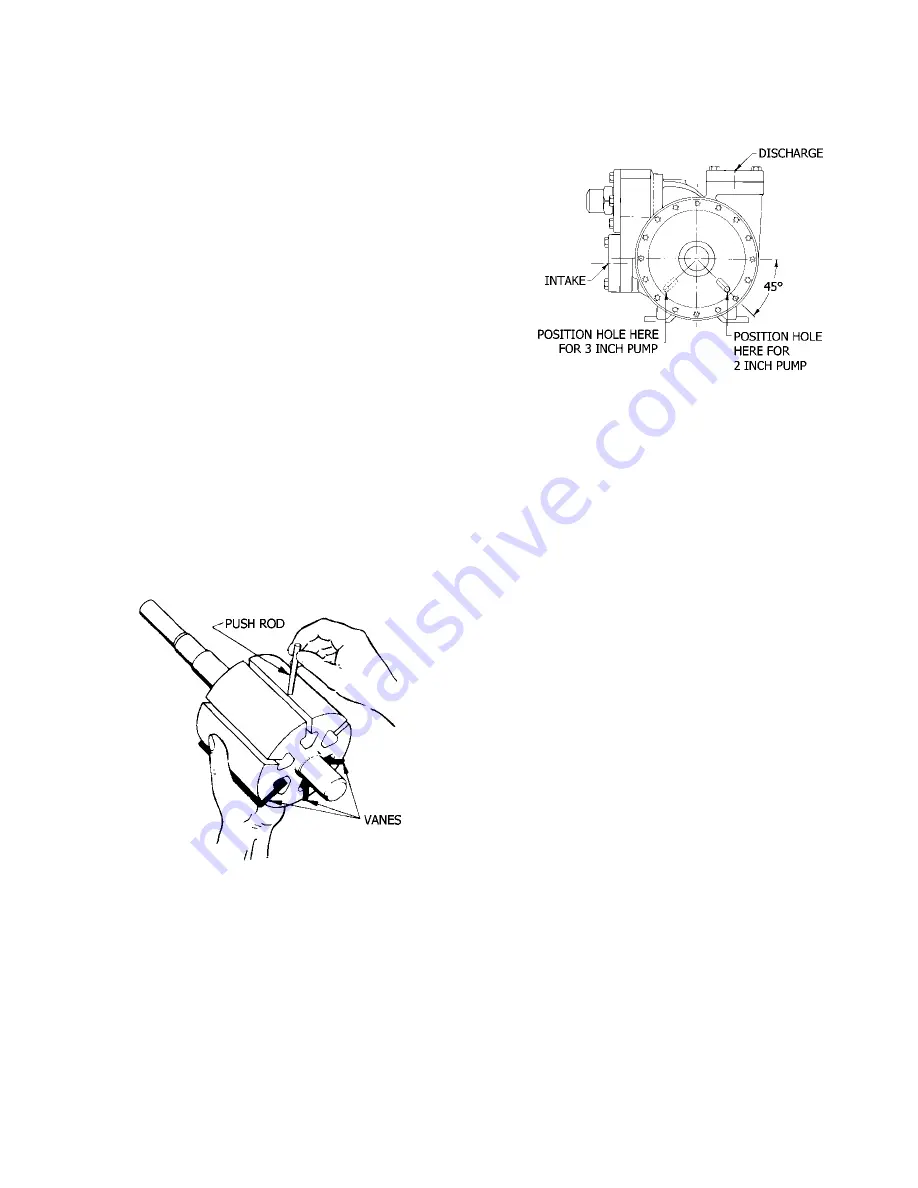
107-B00 Page 9/16
PUMP ASSEMBLY
Before reassembling the pump, inspect all component
parts for wear or damage, and replace as required. Wash
out the bearing/seal recess of the head and remove any
burrs or nicks from the rotor and shaft.
Reassemble the OUTBOARD side of the pump first:
For a CLOCKWISE rotation pump, position the pump
cylinder with the INTAKE port to the
left
.
For a COUNTERCLOCKWISE rotation pump, position
the pump cylinder with the INTAKE port to the
right
.
1. Install the liner key (74) in the slot located in the top of the
liner. Align the key with the notch in the top of the pump
casing and start the liner into the casing.
The word “INTAKE” cast on the liner must face the intake
port of the pump casing. Uniformly tap the outer edge of
the liner with a rubber mallet to fully insert into the casing.
2. On 2 and 3-inch models, place the disc (71) against the
liner with the seal cavity outward.
3. On 4-inch models, attach the disc to the outboard head
without the mechanical seal components. Install disc
machine screws (71A) and lockwashers (71B)
4. Without installing the head O-ring or mechanical seal
components, temporarily attach the outboard head and
bearing to the casing. Install and hand-tighten two head
capscrews, 180 degrees apart. This head will be used to
hold and align the rotor and shaft while the inboard side
of the pump is assembled.
5. Turn the pump around to begin assembly on the inboard
side. Before installing the rotor & shaft assembly, the
direction of pump rotation must be determined as
indicated under the “Pump Rotation” section of this
manual.
Figure 5 – Pushrod Installation
6. Remove the vanes (14) and push rods (77) from the rotor
and shaft assembly. Inspect for wear and damage, and
replace as follows:
a. Insert the vanes into the bottom three rotor slots with
the relief grooves facing in the direction of pump
rotation, and with the rounded edges outward. See
Figure 4.
b. Hold the three bottom vanes in place while inserting
the three push rods (77). See Figure 5.
c. After the bottom vanes and push rods are installed,
carefully insert the non-driven end of rotor and shaft
into the casing.
d. Install the remaining vanes into the top positions of
the rotor.
7. DISC – 2 and 3-inch Models
Install the disc (71) on the inboard side of the pump with
the seal cavity facing outward and the disc relief hole
located as shown in Figure 6.
Figure 6 – Disc Relief Hole Location
2 and 3-inch Models
8. MECHANICAL SEAL – 2 and 3-inch Models
Rotating Assembly
a. Apply a small amount of motor oil on the shaft
between the shaft threads and the rotor.
b. Slide the seal jacket assembly (153C) over the shaft
and into the disc cavity with the drive tangs of the
jacket towards the rotor. Rotate the jacket assembly
to engage the drive tangs in the rotor slots.
c. Install a new rotating O-ring (153E) in the rotating seal
face (153B). Align and insert the rotating assembly
into the the seal jacket with the polished face outward.
Clean the polished face with a clean tissue and
alcohol.
Stationary Seat
a. Apply a small amount of motor oil in the seal access
of the head.
b. Install a new stationary O-ring (153D) in the stationary
seat (153A). Clean the polished face with a clean
tissue and alcohol. Align the pin in the stationary seat
with the slot in the head recess and push the seat
fully into the seal recess with the polished face
outward.
9.
DISC and MECHANICAL SEAL – 4-inch Models
a. Before attaching the disc, apply a small amount of
motor oil in the recess of the head.
b. Install a new stationary O-ring (153D) in the
stationary seat (153A). Align the pin in the stationary
seat with the slot in the head recess and push the
seat fully into the seal recess with the polished face
outward. Clean the polished face with a clean tissue
and alcohol.
c.
Install a new rotating O-ring (153E) in the rotating
seal face (153B). Clean the polished face with a
clean tissue and alcohol. Place the polished face of
the rotating seal against the face of the stationary
seat in the head.
d. Align and install the seal jacket assembly (153C)
over the rotating face with the drive tangs outward.
e. Carefully place the disc on the head with the seal
cavity inward. The drive tangs of the seal jacket
should protrude through the center hole of the disc.