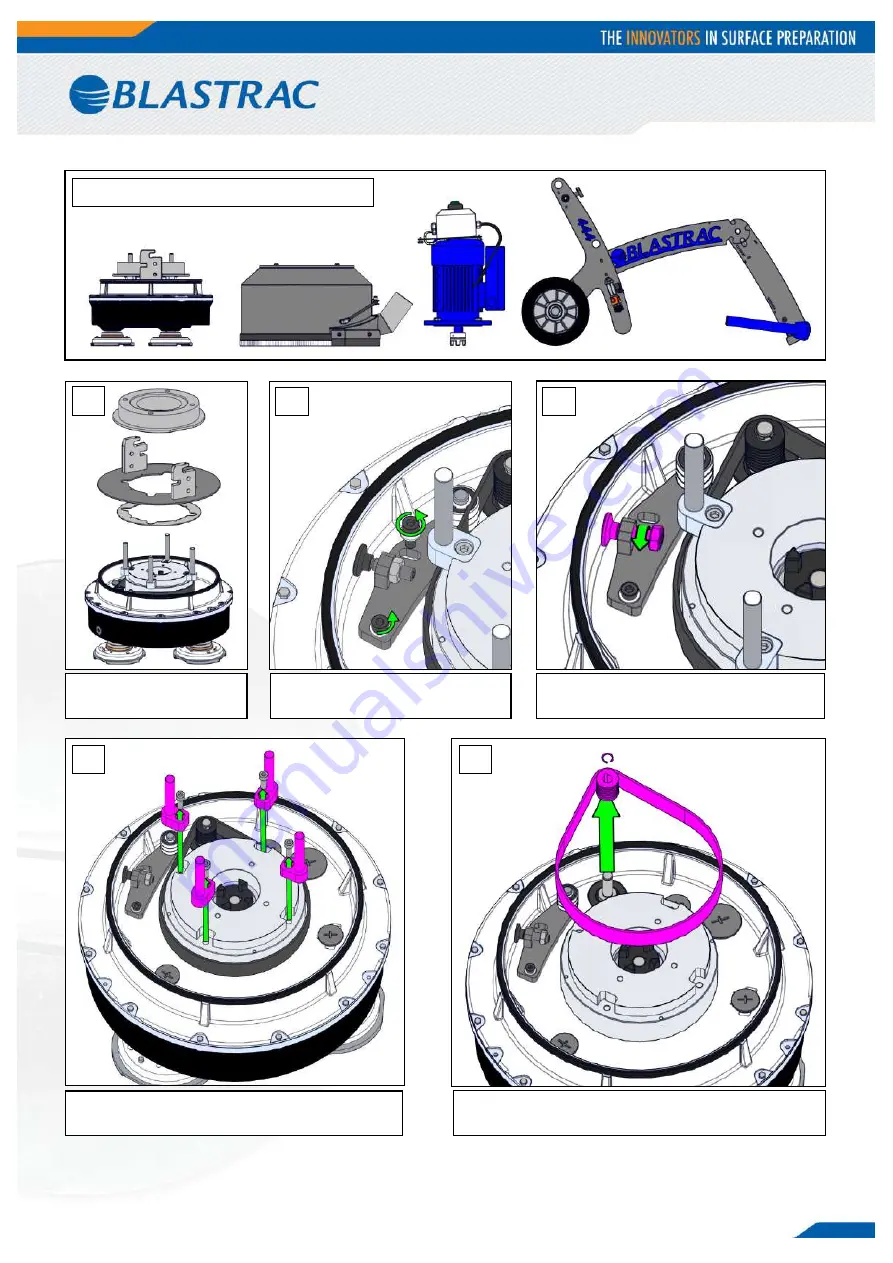
27
6.3
Replacing the upper belt
NOTE
: When mounting the upper belt, tension the upper belt at 220-240 Hz.
1. Dismount the machine in 4 pieces:
2
3
4
Remove the Block,
Plate and Spacer.
Loosen the bolts of the
tensioning slideplate.
Loosen the pressure piece.
Remove the mounting cams.
5
Remove the circlip above the contra pulley.
Slide the belt + contra pulley off.
6
Summary of Contents for BMG-444
Page 1: ...Original Instructions OPERATING INSTRUCTIONS BMG 444 VERSION 1 0 ...
Page 13: ...13 4 4 Adjust the steering height ...
Page 14: ...14 Adjust the steering handle ...
Page 28: ...28 6 4 Tensioning the lower belt 1 2 3 4 5 ...
Page 33: ...33 8 2 Dimensions of the BMG 444 1310 mm 982 mm 940 mm 824 mm 507 mm ...