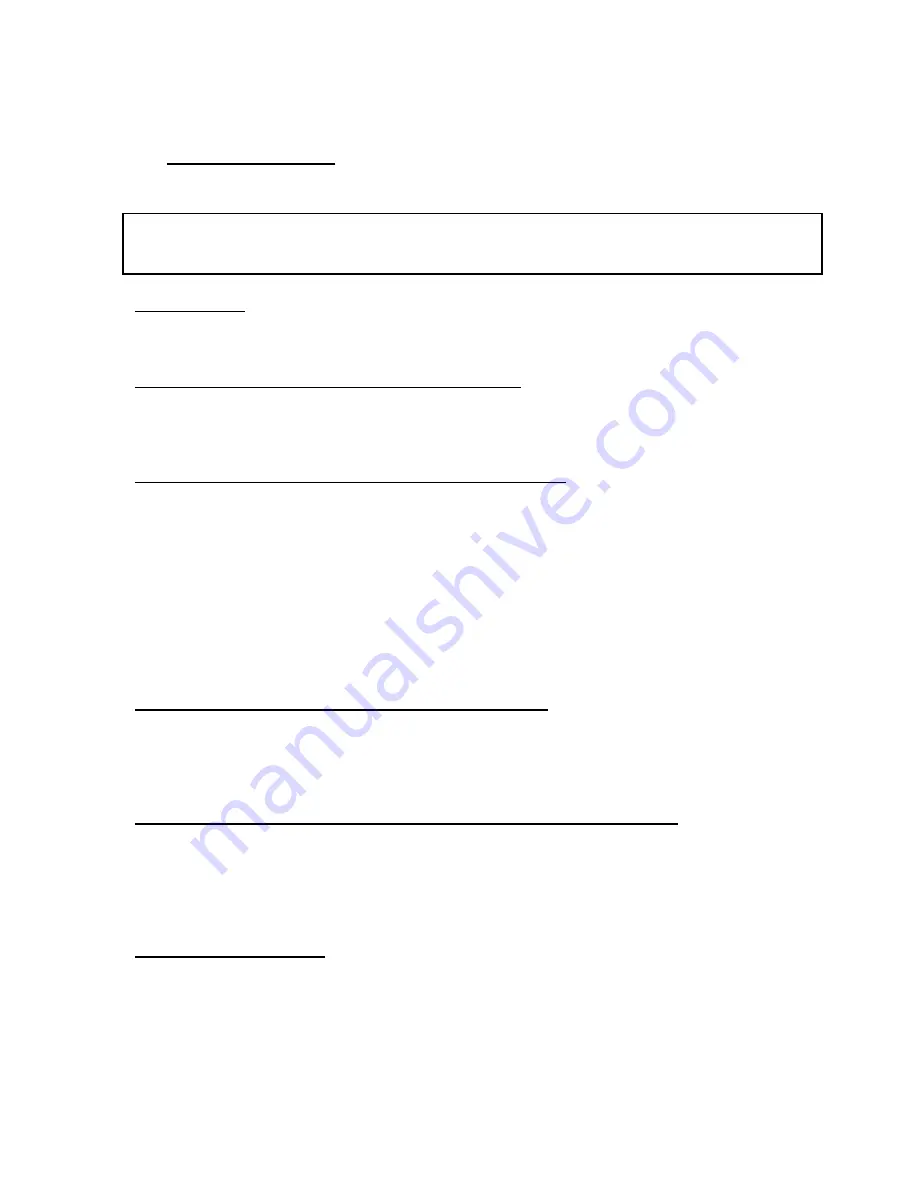
16
6.0 TROUBLESHOOTING
DOOR LEAKS
1. Check for damage to door gasket.
WATER ACCUMULATES IN THE COMPARTMENT
1. Compartment drain screen clogged. Remove and clean thoroughly and then
replace.
WATER NOT BEING SUPPLIED TO HEAT EXCHANGER
1. Water supply is “OFF”.
2. Defective water fill solenoid.
3. Water level control clogged or defective, unable to operate fill valve.
4. Check drain valve is closed. Also check that water level control valve is closed.
5. Supply water pressure too low.
AUTOMATIC BLOWDOWN VALVE DOES NOT DRAIN
1. Defective Blowdown valve.
2. Heat exchanger build up of scalant clogging drain lines and valve.
HEAT EXCHANGER ACHIEVES PRESSURE SLOWER THAN NORMAL
1. Heavy build up of lime on heat exchanger tubes.
2. Steam supply pressure too low.
SAFETY VALVE BLOWS
1. Defective safety valve.
2. Pressure too high. Pressure switch requires adjustment (lower) or may be defective.
NOTICE: Contact the factory, the factory representative or local service
company to perform maintenance and repairs.
Refer to warranty terms.