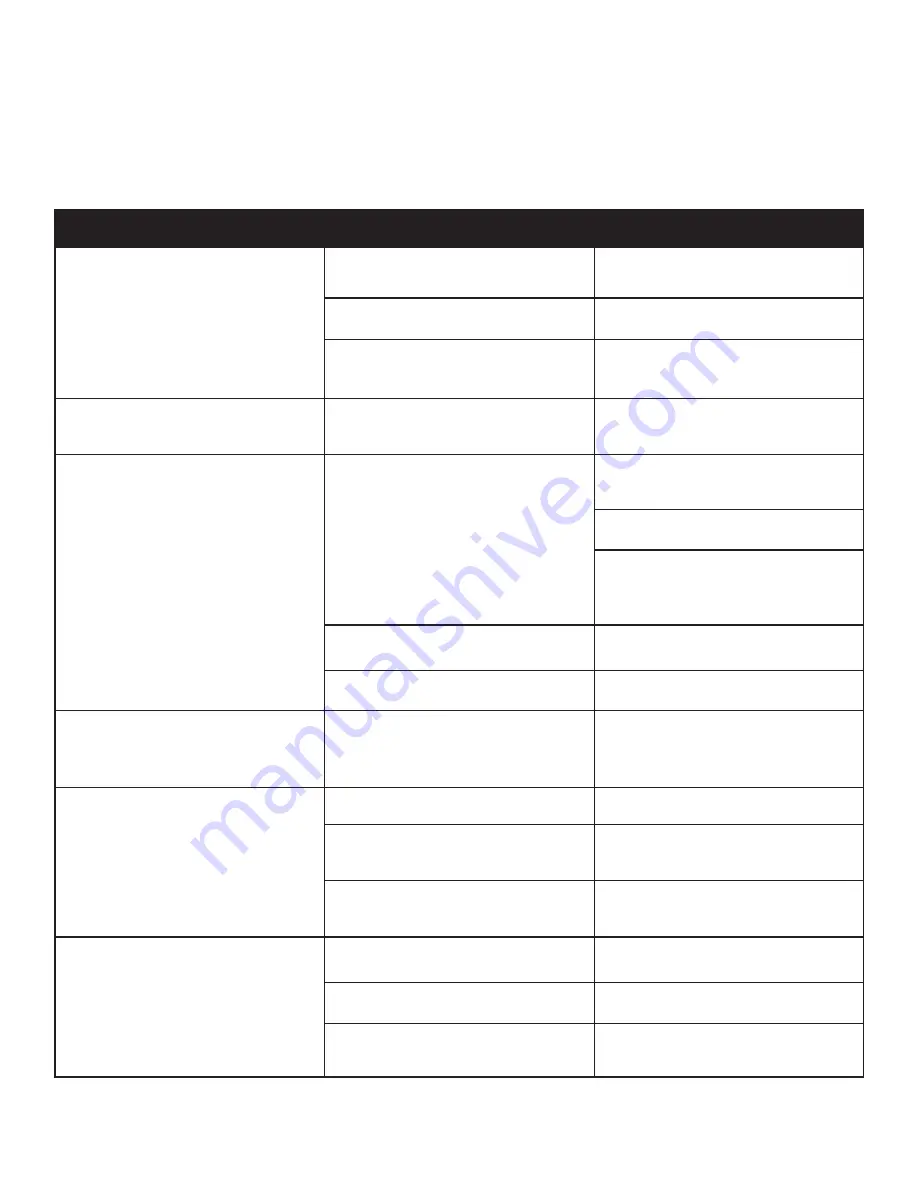
IDP1010 • Owner’s Manual
17
Problem
Possible Cause
Solution
Insufficient flow of cooling water or
no cooling water at all
The pump draws air
Fill the container with water
Filter clogged
Clean the filter of the pump
Pump wheel of the immersion pump
blocked by dirt
Disassemble the immersion pump
and clean
Irregular run of the saw blade
Poor tension in the blade material
Return the saw blade to the manu-
facturer
Saw blade wobbles when running
Saw blade is damaged or bent
Have the saw blade aligned /
flattened
Clean the receiving flange
Solder the diamond segments of the
old blade onto another saw blade or
use a new blade
Flange of the saw blade is damaged
Replace the saw blade flange
Shaft of the motor is bent
Replace the electric motor
Diamond segment becomes loose
Overheating of the saw blade; cool-
ing water not sufficient
Have the diamond segment soldered
on the blade again; ensure optimum
flow of cooling water
Excessive wear
Wrong type of saw blade
Use harder saw blades
Shaft of motor causes wobbling
Have bearings of the motor or the
motor replaced
Overheating
Ensure optimum flow of cooling
water
Cracks in or near the diamond seg-
ment
Saw blade too hard
Use a softer blade
Fixed flange is worn out
Replace the fixed flange
Motor shaft bearing
Replace the bearing of the motor
shaft