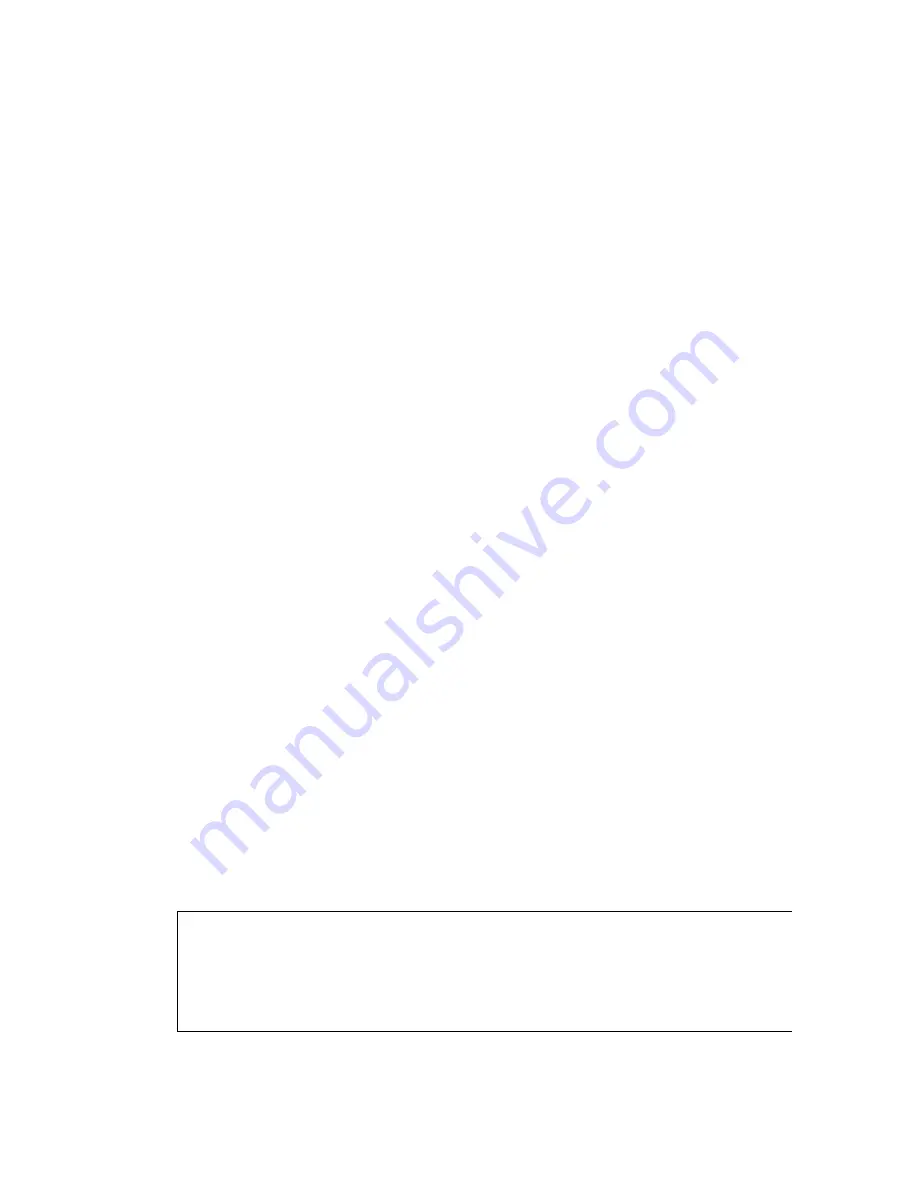
14.
You are then required to check the strength of the flame sensing device
by removing the link on the burner, which connects the flame probe to
the control box and put your multi-meter in series, which should give
you a reading in uA. The signal strength should be a least 70uA for U.V.
and 6uA on flame rectification.
15.
After running the unit for a period of one hour you will be able to get a
running temperature from the fan limit side of the stat. When you have
this you must set the over heat to 20°C above the running temperature.
The supply fans should be shut down once, when the burner is running
to try the overheat device and the fans must be switched on as soon as it
locks out on overheat.
16.
All gas nipples are to be replaced and checked for tightness and checked
with leak detection fluid.
17.
A leak detection test is to be done with leak detection fluid and
electronic leak detector on the gas train while the burner is running to
see if there are any leaks in the burner gas train and a soundness test is to
be done on all gas work.
18.
Finally make a full record of combustion data on commissioning sheet
provided; a copy is to be presented to the customer and to BMM Heaters
on completion of work. The commissioning sheet should include the
following:
(a)
Model and Serial Numbers.
(b)
Heater running temperature and overheat settings.
(c)
Full thermal input.
(d)
Governor pressure setting (pilot for start gas and main for full fire).
(e)
Gas flow rates for full fire.
(f)
Burner damper setting and pressure switch settings.
(g)
Flame signal strength on full fire.
(h)
Exhaust gas O², CO², CO and temperature.
After setting all air pressure switches and valves etc, you must mark the
position or lock off if possible.
TYPICAL FLUE GAS READINGS
O² - 4% to 5%
CO² - 9.5% to 10%
CO – up to 100 PPM (Typical approx 20 PPM)
Flue Stack Temperature – Up to 330°c Nett
28