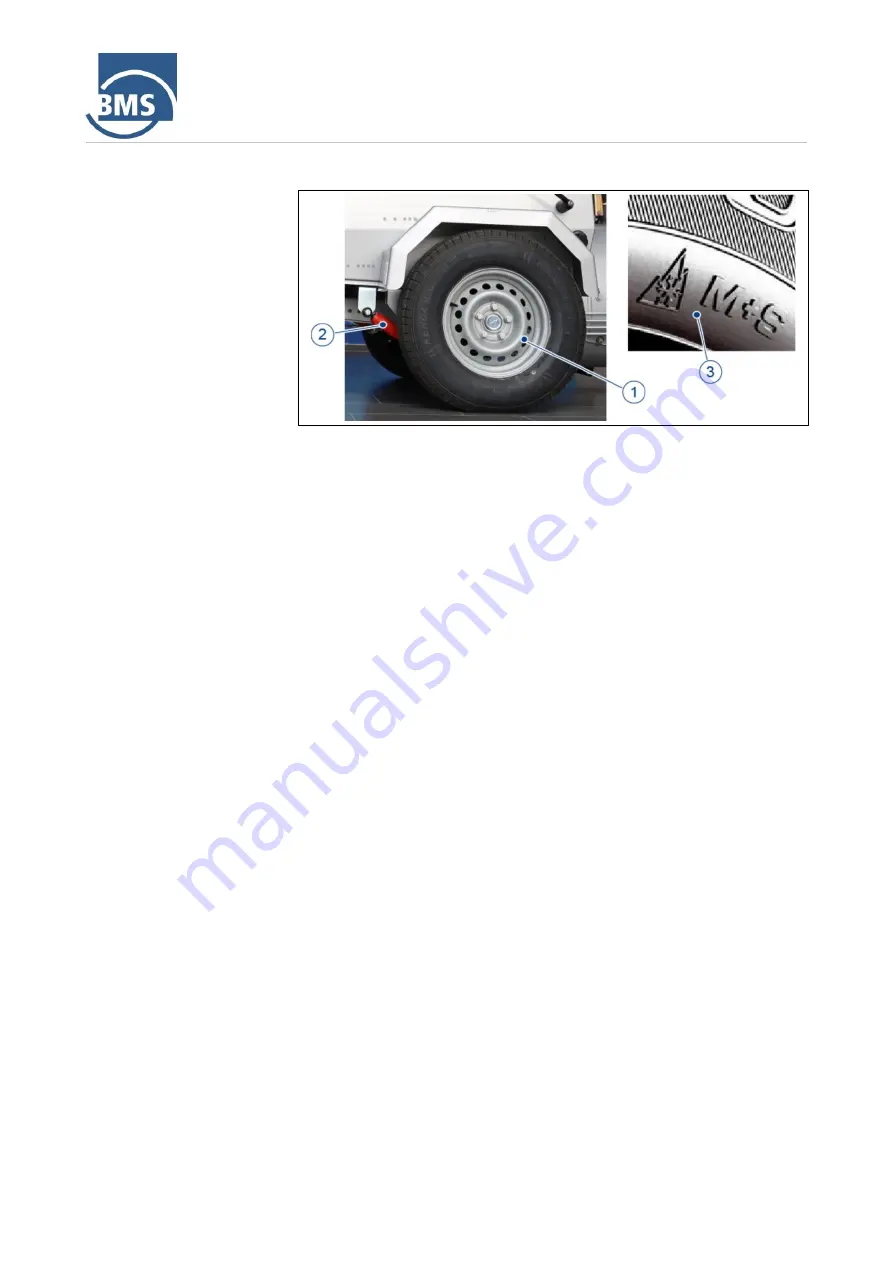
Layout and function
4
Chassis
4.3
41
Axle with wheels
Figure 11: Axle with wheels
The Euro axle is mounted with rubber bodies. The two wheels (1) are
located on the axle. Shock absorbers (2) cushion the trailer. In driving mode
the trailer is braked by the wheel brakes. These comply with the pollutant
ordinance and EC directive.
Only the wheels listed in the vehicle documents (registration certificate part
I) may be fitted. When changing wheels, the hub and wheel connection,
wheel type and wheel type must correspond exactly to the specifications in
the vehicle registration document.
When using the
BMS
alpha
CR
in winter, we recommend using M&S tires or
all-season tires with the properties shown in the figure (3).
➢
Winter tyres are not mandatory (status 10/2011). However, in the event
of an accident or getting stuck, the tyres, which may not be suitable for
the weather conditions, can be criticised.
Legal changes are possible at any time.
Please inform yourself regularly about the relevant regulations and
laws.
Summary of Contents for alpha CR
Page 6: ...Contents ...
Page 180: ...14 Appendix 14 1 Declaration of conformity 180 14 1 Declaration of conformity ...
Page 181: ...Appendix 14 Drawings 14 2 181 14 2 Drawings 14 2 1 BMS alpha CR standard ...
Page 182: ...14 Appendix 14 2 Drawings 182 14 2 2 BMS alpha CR B feeder ...
Page 183: ...Appendix 14 Drawings 14 2 183 14 2 3 BMS alpha CR B S feeder scraper ...
Page 185: ...Appendix 14 Circuit diagrams 14 3 185 ...
Page 186: ...14 Appendix 14 3 Circuit diagrams 186 ...