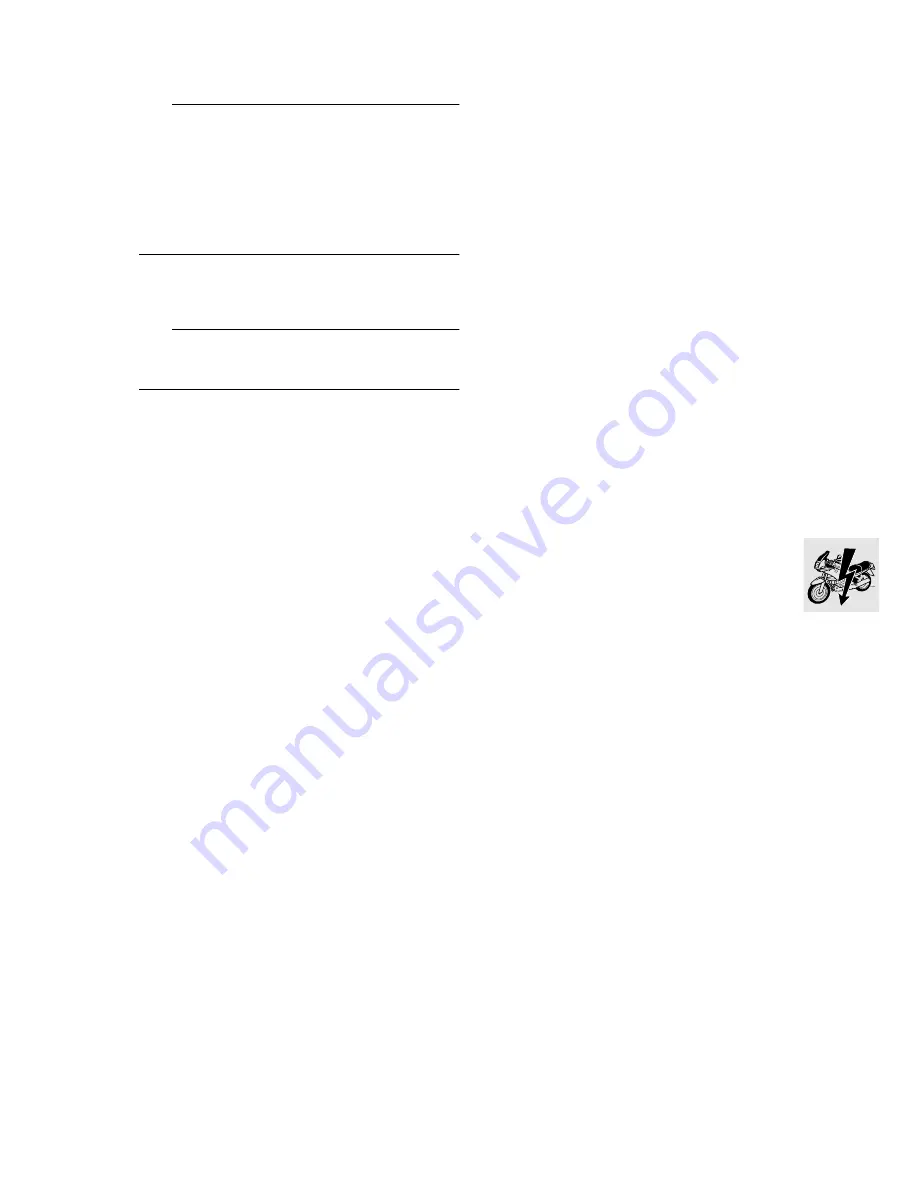
61.7
Frame wiring harness
e
Caution:
Use (yellow) galvanized bolts for the ground (earth)
connection to the engine.
Screws with unsuitable corrosion proofing can
cause the electrical resistance to rise as high as
80
Ω
.
Run wiring without kinking and avoid risk of abra-
sion.
Note the number and position of the cable straps.
•
Apply a thin coating of contact grease, e.g.
CENTOPLEX 3 CU
to the central earth (ground)
point, which must be cleaned to bright metal
first.
L
Note:
When removing the wiring harness, take out the
central electrical equipment box at the same time.
X
Tightening torque:
Ground (earth) connection to engine .............. 7 Nm
Summary of Contents for R 1200 C
Page 1: ...BMW AG Motorcycle Division After Sales R 850 C R 1200 C Repair Manual ...
Page 4: ......
Page 18: ...00 10 ...
Page 40: ...11 4 ...
Page 47: ...11 11 Sectioned drawing of engine ...
Page 48: ...11 12 Lubricating oil circuit ...
Page 49: ...11 13 Coolant circuit ...
Page 50: ...11 14 ...
Page 61: ...11 25 Removing cylinder head RS110110 M6 x 30 M6 x 30 M6 x 30 M10 x 70 ...
Page 100: ...11 64 ...
Page 102: ...12 2 ...
Page 104: ...12 4 ...
Page 112: ...12 12 ...
Page 114: ...13 2 ...
Page 116: ...13 4 ...
Page 120: ...13 8 ...
Page 122: ...16 2 ...
Page 124: ...16 4 ...
Page 128: ...16 8 ...
Page 130: ...18 2 ...
Page 132: ...18 4 ...
Page 134: ...21 2 ...
Page 136: ...21 4 ...
Page 140: ...21 8 ...
Page 142: ...23 2 ...
Page 144: ...23 4 ...
Page 166: ...23 26 ...
Page 168: ...31 2 ...
Page 170: ...31 4 ...
Page 180: ...32 2 ...
Page 182: ...32 4 ...
Page 188: ...33 2 ...
Page 190: ...33 4 ...
Page 206: ...33 20 ...
Page 210: ...34 4 ...
Page 226: ...34 20 Removing and installing brake lines Removing and installing front brake line C340020 ...
Page 227: ...34 21 Removing and installing rear brake line C340030 ...
Page 230: ...36 2 ...
Page 232: ...36 4 ...
Page 240: ...36 12 ...
Page 242: ...46 2 ...
Page 244: ...46 4 ...
Page 254: ...51 2 ...
Page 257: ...52 1 Contents Page 52 Removing and installing seat 3 52 Seat ...
Page 258: ...52 2 ...
Page 260: ...52 4 ...
Page 262: ...61 2 ...
Page 263: ...61 3 61 Technical data R 850 C R 1200 C Battery Amp h 19 ...
Page 264: ...61 4 ...
Page 268: ...61 8 Wiring harness View from left C619020 1 2 3 ...
Page 269: ...61 9 1 C619021 ...
Page 270: ...61 10 2 C619022 ...
Page 271: ...61 11 3 C619023 ...
Page 272: ...61 12 Wiring harness View from right 1 2 3 C619030 ...
Page 273: ...61 13 1 C619011 ...
Page 274: ...61 14 2 C619012 ...
Page 275: ...61 15 3 C619013 ...
Page 276: ...61 16 ...
Page 278: ...62 2 ...
Page 280: ...62 4 ...
Page 282: ...62 6 ...
Page 284: ...63 2 ...
Page 286: ...63 4 ...
Page 288: ...63 6 ...