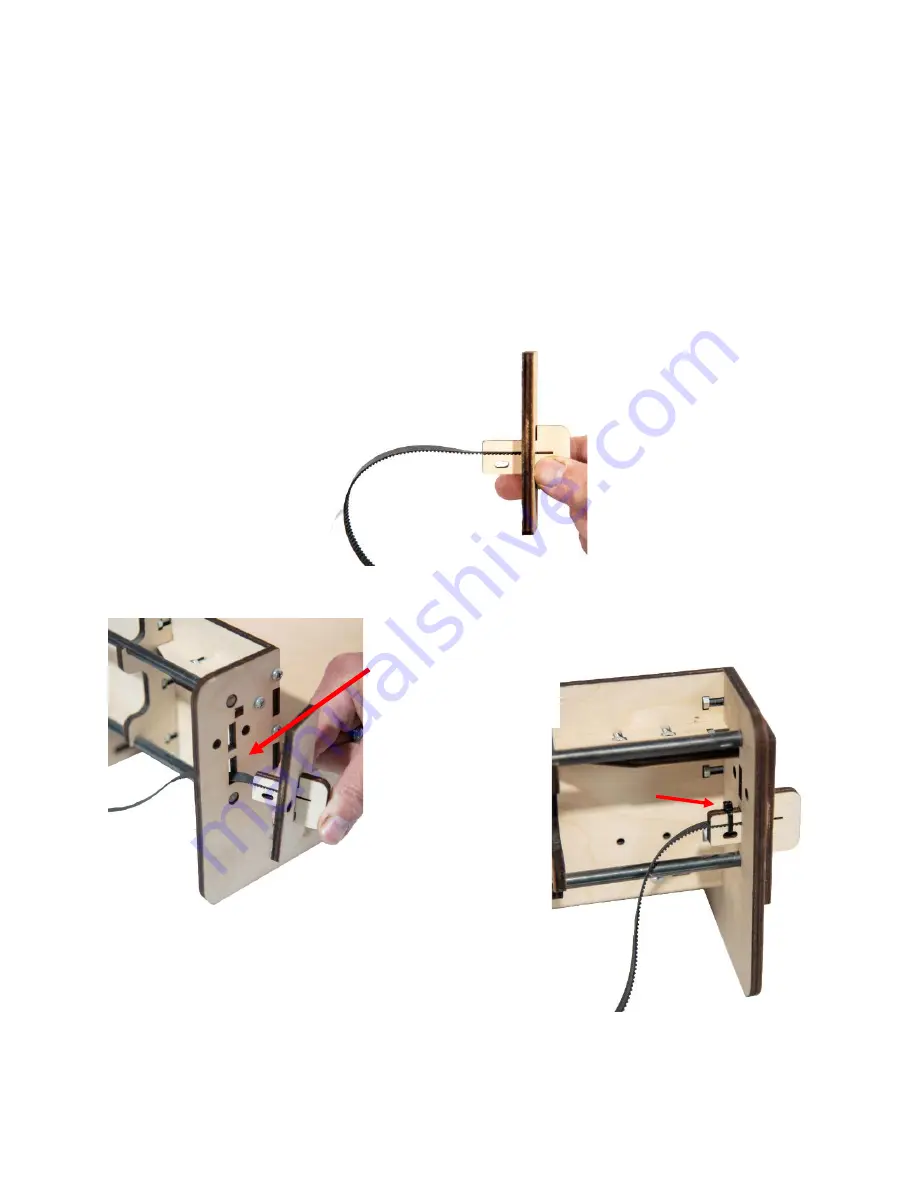
31
10d
Insert the Belt Retainer and Belt into and through the
Rail Stop. Then insert the Assembly into the bottom
slot at the back of the X Frame Assembly.
NOTE: Using a Zip Tie, snug the belt in the
Retainer. Make sure the square lock of the Zip Tie
is located on the top of the Belt Retainer.
Right Side Rear View
Zip Tie
Be sure to insert
in the lower slot
at the rear of the
machine.