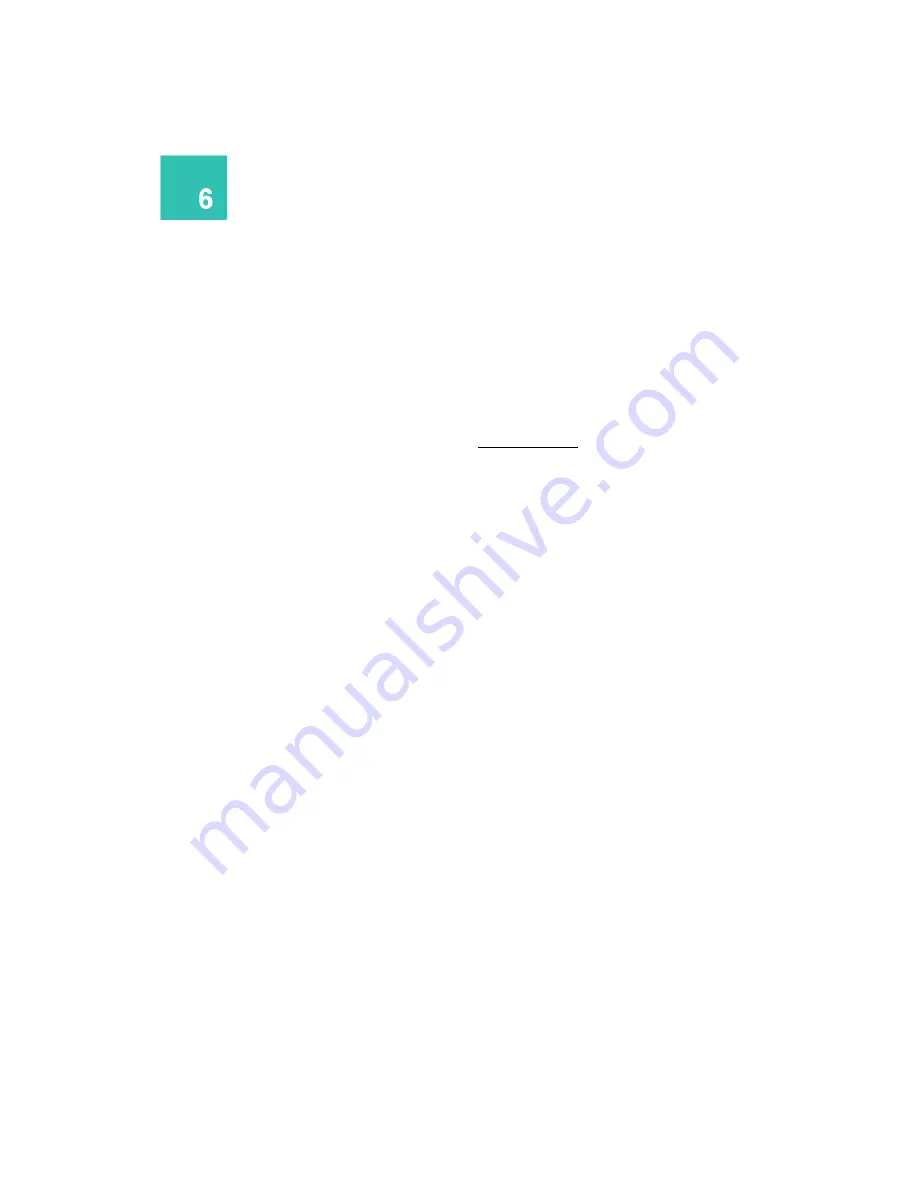
Maintenance
Maintenance UK
It is a legal requirement, under regulation 9 of the COSHH
regulations that all local exhaust ventilation systems are
thoroughly examined and tested at least once every 14
months (typically carried out annually). The approved code
of practice recommends that a visual check should be
carried out at least once a week.
COSHH requires the annual inspection and testing to be
carried out by a competent person and specifies that
documentation results are recorded in a log.
Contact the seller for more information about inspection
and certification.
Maintenance General
User maintenance is limited to cleaning the unit and filter
replacement, only the manufacturers trained maintenance
technicians are authorised to carry out component testing
and replacement. Unauthorised work or the use of
unauthorised replacement filters may result in a potentially
dangerous situation and/or damage to the extractor unit
and will invalidate the manufacturer’s warranty.
Cleaning the unit
The powder coat finish can be cleaned with a damp cloth
and non-aggressive detergent, do not use an abrasive
cleaning product as this will damage the finish.
The cooling inlets and outlets should be cleaned once a year
to prevent build-up of dust and overheating of the unit.
Filter Information
A log of filter changes should be maintained by the user.
The filters require attention when the display shows the
configuration shown on the next page or when the extractor
no longer removes fume efficiently.
It is recommended that a spare set of filters are kept on site
to avoid prolonged unit unavailability. Part numbers for
replacement filters can be found on the filters fitted in your
system.
To prevent overheating, units should not be run with a
blocked filter condition, or with dust obstruction of Inlets /
Outlets.
Fire Risk Warning
In the very rare event that a burning ember or spark is
drawn into the fume extraction unit, it may be possible that
the filters will ignite.
Whilst any resultant fire would typically be retained within
the fume extraction unit, the damage to the extractor
could
be significant.
It is therefore essential to minimise the possibility of this
occurring by undertaking an appropriate Risk assessment to
determine:-
a). Whether additional fire protection equipment should be
installed.
b). Appropriate maintenance procedures to prevent the risk
of build-up of debris which could potentially combust.
This unit should not be used on processes where sparks
could occur, with explosive dusts and gases, or with
particulates which can be pyrophoric (can spontaneously
ignite), without implementation of additional precautions
It is essential that nozzles or other extraction/ fume capture
devices and hoses/pipework are cleaned regularly to prevent
the build-up of potentially ignitable debris
01
Summary of Contents for V600
Page 1: ...V600 Issue 2 Jan 2017 ...
Page 2: ......