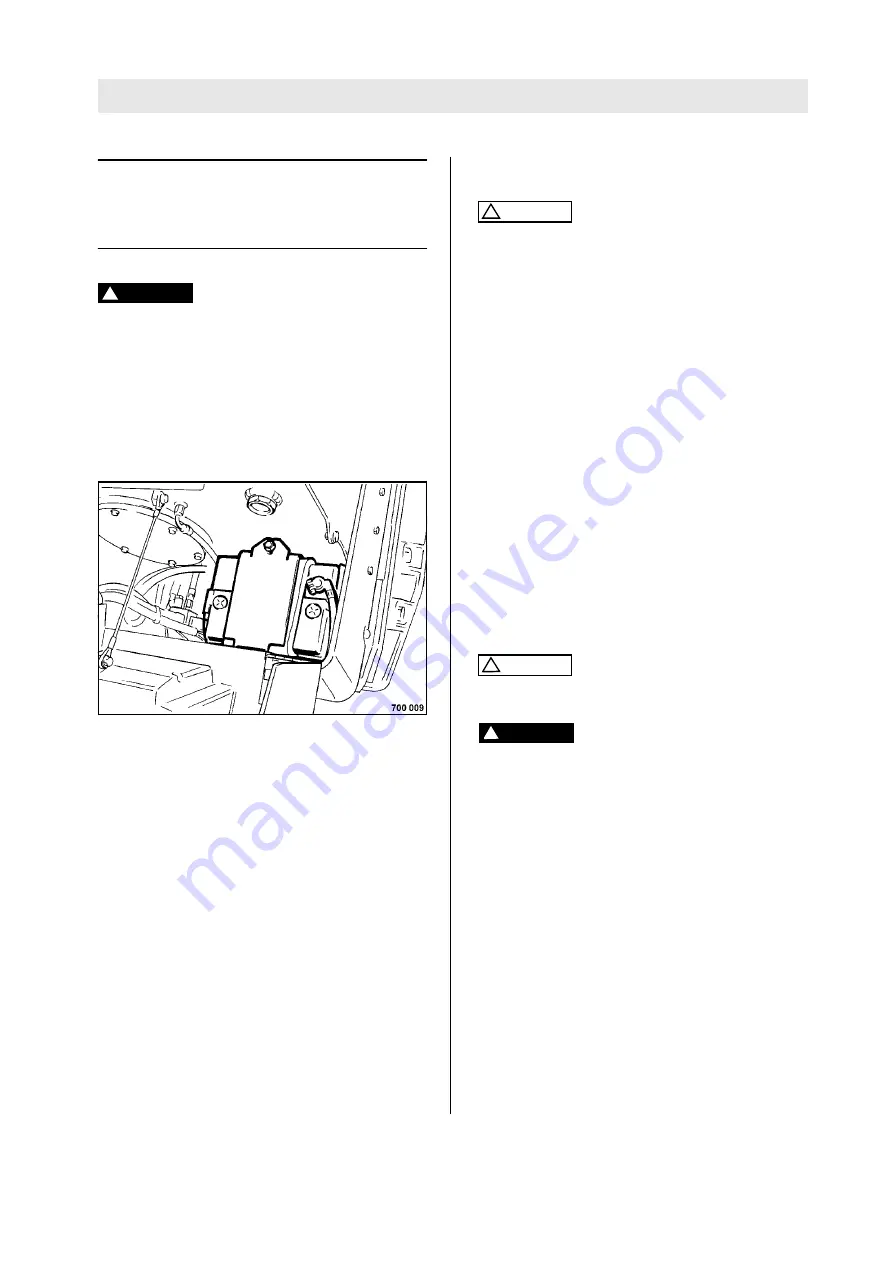
Maintenance every month
BOMAG
39
BPH 80/65
Maintenance every m onth
4.11 Checking the condition of
the battery
*
, greasing the
poles
!
Danger
Danger of injury!
When working on the battery do not smoke, do
not use open fire.
Do not let skin and clothes come in contact
with acid.
Wear protective goggles.
Do not place any tools on the battery.
Fig. 38
l
Open the rear hood.
l
Take the vibration insulation mats off.
l
Take the battery (Fig. 38) out and clean the
battery compartment.
l
Clean the outside of the battery.
l
Clean the battery poles and pole clamps and
cover them with acid free grease (vaseline).
l
Check the fastening of the battery.
l
Check the condition of the vibration insulation
mats, replace if necessary.
l
Close the front hood again tightly after having
serviced the battery.
Non-maintenance free batteries
!
Caution
Top up missing fluid with distilled water.
l
Open the plugs and check the acid level, if
necessary top up with distilled water.
With control inserts:
The acid level must reach the bottom of the control
inserts.
Without control inserts
Acid level 10 to 15 mm above the upper edge of
the lead plate, measure with a clean wooden stick.
With transparent battery housing:
Acid level up to the mark on the housing.
Maintenance free batteries
Perform only the following points:
l
Check the battery for cleanliness.
l
Clean the poles.
l
Tighten the terminal clamps.
!
Caution
Dispose of old batteries environmentally.
!
Danger
Development of gas!
If possible remove the plugs when recharging
the battery, to avoid an accumulation of highly
explosive gases.
*
Option
Summary of Contents for BPH 80/65
Page 2: ......
Page 6: ...Table of Contents BOMAG 6 BPH 80 65 ...
Page 7: ...BOMAG 7 BPH 80 65 1 Technical Data ...
Page 11: ...BOMAG 11 BPH 80 65 2 Safety regulations ...
Page 16: ...Safety regulations BOMAG 16 BPH 80 65 ...
Page 17: ...BOMAG 17 BPH 80 65 3 Operation ...
Page 28: ...Operation BOMAG 28 BPH 80 65 ...
Page 29: ...BOMAG 29 BPH 80 65 4 Maintenance ...
Page 53: ...BOMAG 53 BPH 80 65 5 Trouble shooting ...
Page 57: ......
Page 58: ......