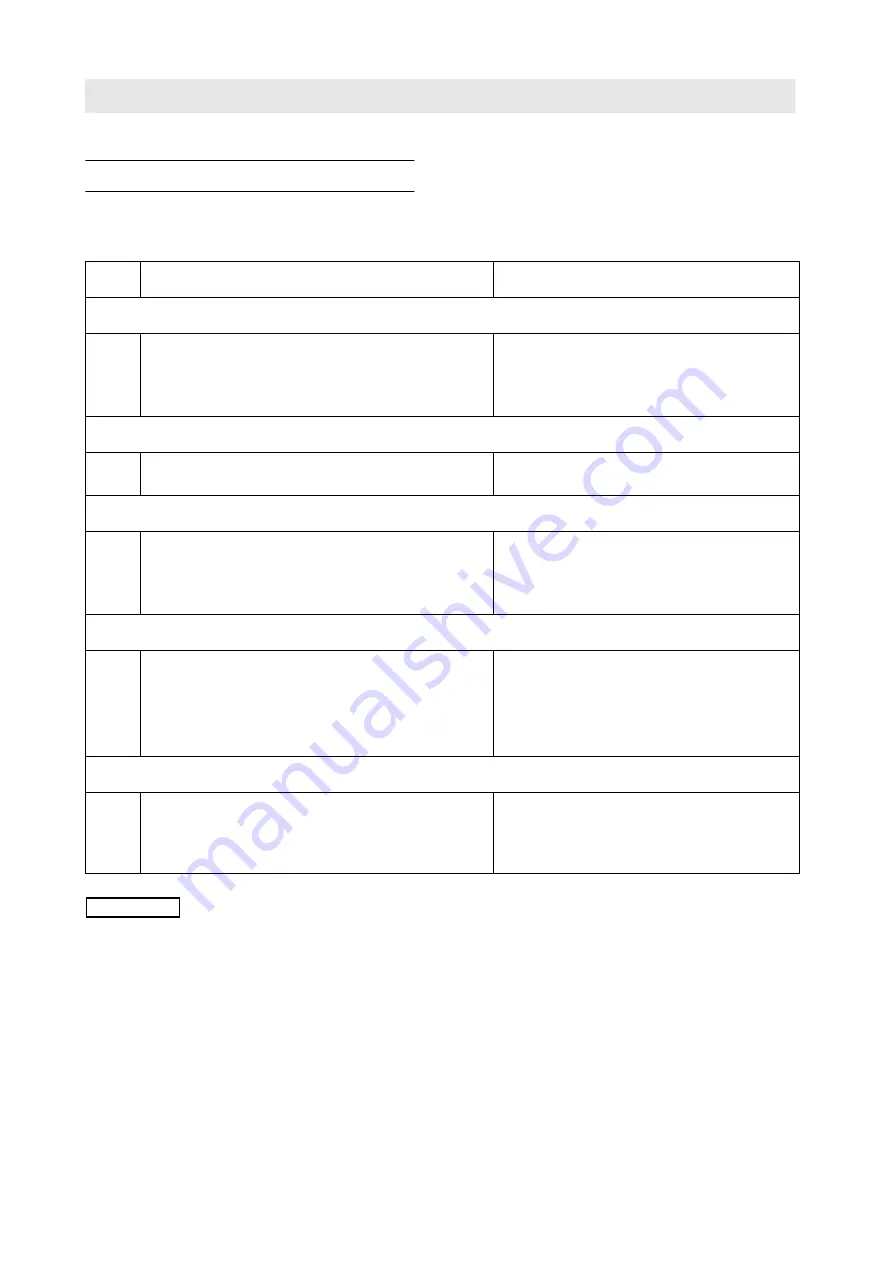
0DLQWHQDQFH
%20$*
30
BPR 25/32 - BPR 25/40
4.5
Maintenance table
With all maintenance tasks perform also the
work for shorter preceding service intervals.
L
Note
With all maintenance tasks perform also the work
for shorter preceding service intervals.
Pos.
Description
Note
Maintenance every day
4.6
Clean machine/engine
4.7
Check the engine oil level
to bottom edge of filler opening
4.8
Check the fuel level
4.9
Check/clean the air filter
Maintenance every month
4.10
Clean cooling fins and cooling air intake
4.11
Check the oil level in the vibrator shaft housing
to bottom edge of filler opening
Maintenance every 6 months
4.12
Change the engine oil
4.13
Check, clean the spark plug
4.14
Clean the fuel sludge filter
4.15
Check, tension, change the V-belt
Dim. mm (inch)
4.16
Clean, change the air filter
4.17
Check, adjust the valve clearance
4.18
Clean the fuel screen
4.19
Change the oil in the vibrator shaft housing
4.20
Check the rubber buffers
As required
4.21
Tightening torques for screws with metric unified
thread
Observe the tightening torques
4.22
Tighten all bolted connections
4.23
Engine conservation
Go
to
Discount-Equipment.com
to
order
your
parts