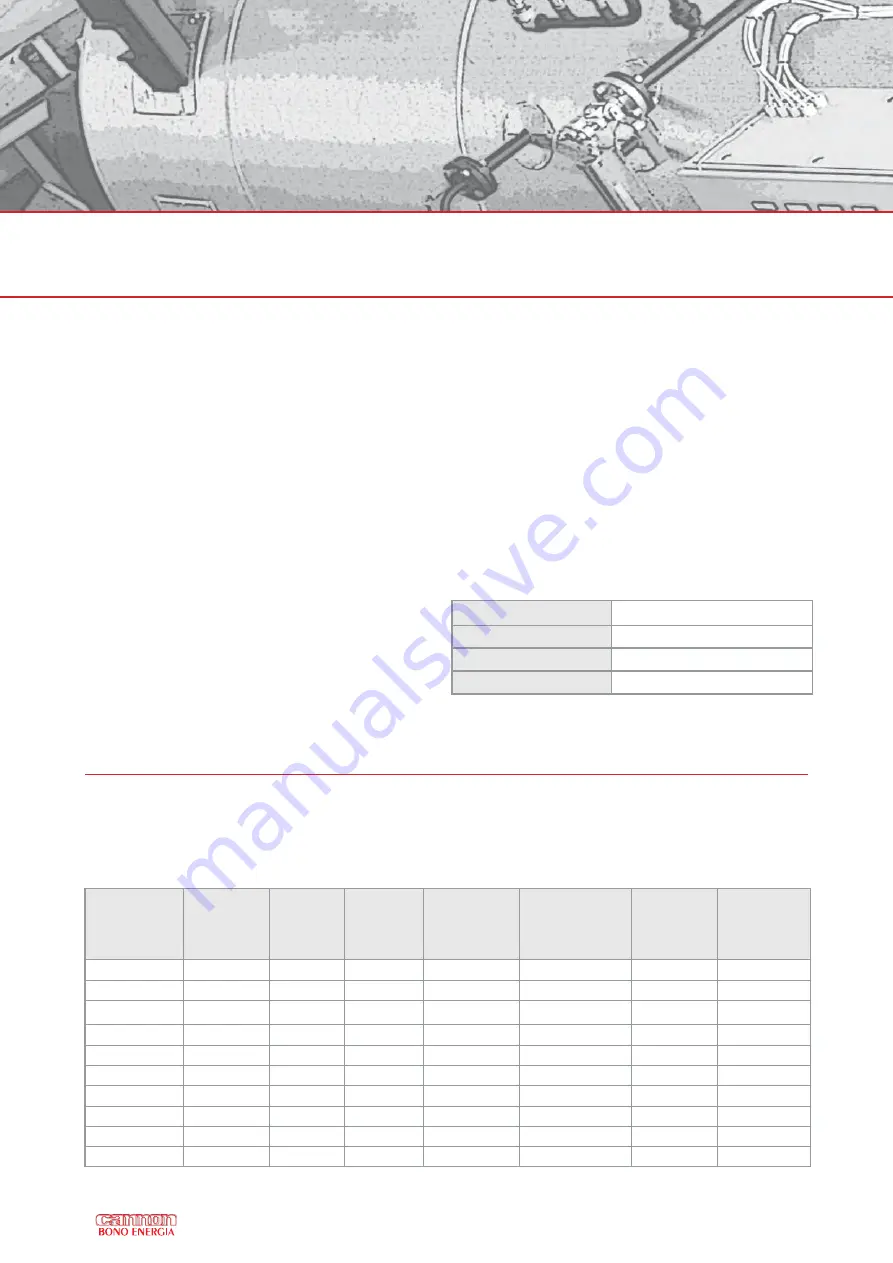
10
The generator must be supplied with water with
hardness less than 0.1° F made up of the condensation
recovery and the make-up water softened by a
purifier (cation resin) or demineralised. The water
supply must always come from the supply tank; a
direct connection to the mains water or to the purifier
is not allowed.
The suction piping must be as straight as possible
and its diameter must be larger than that of the
connection on the pump (see connection diagram).
The supply water must be at a temperature of at least
70° C
as lower temperatures cause deterioration in
the generator coils.
If the water temperature is lower than the value
indicated above the supply water must be heated.
The tank capacity must be adequate for the boiler
capacity and normally at least the same as the
consumption of an hour operation at maximum load.
The tank must be fitted with a drainage tube with
cock direct to the sewers for regular drainage and to
empty the tank for cleaning.
Water pump must not suck from the bottom of the
tank but slightly higher to avoid the entry of impurities.
If the
oxygen scavenger
is required please refer to
the technical specifications of the product in use.
Total hardness
Less than 0,05 °F
pH
8.5-10.0
Alkalinity
Max 1000 ppm
Silicone (Si O
2
)
Max 100 ppm
Table 2
Water supply specifications.
In order to maintain
its best performance the steam generator must
be supplied with water conforming to the below
specifications.
Table 3
Minimum pressure / suction head for water.
The tank must be raised up and have sufficient head for correct
pump operation and to avoid phenomena of cavitation due to insufficient supply
Temperature
°C
Had Height
mH
2
O
Pressure
bar
Pressure
MPa
Temperature
°C
Liquid Column
Height
mH
2
O
Pressure
bar
Pressure
MPa
0
0.00
0.00
0.00
50
1.25
0.12
0.012
5
0.00
0.00
0.00
55
1.75
0.17
0.017
10
0.00
0.00
0.00
60
2.00
0.20
0.02
15
0.20
0.02
0.002
65
2.50
0.25
0.025
20
0.20
0.02
0.002
70
3.00
0.29
0.029
25
0.25
0.02
0.002
75
4.00
0.39
0.039
30
0.50
0.05
0.005
80
5.00
0.49
0.049
35
0.80
0.08
0.008
85
6.00
0.59
0.059
40
0.90
0.09
0.009
90
7.00
0.69
0.069
45
1.00
0.10
0.01
95
9.00
0.88
0.088
3. TECHNICAL SPECIFICATIONS - WATER SUPPLY REQUIREMENTS