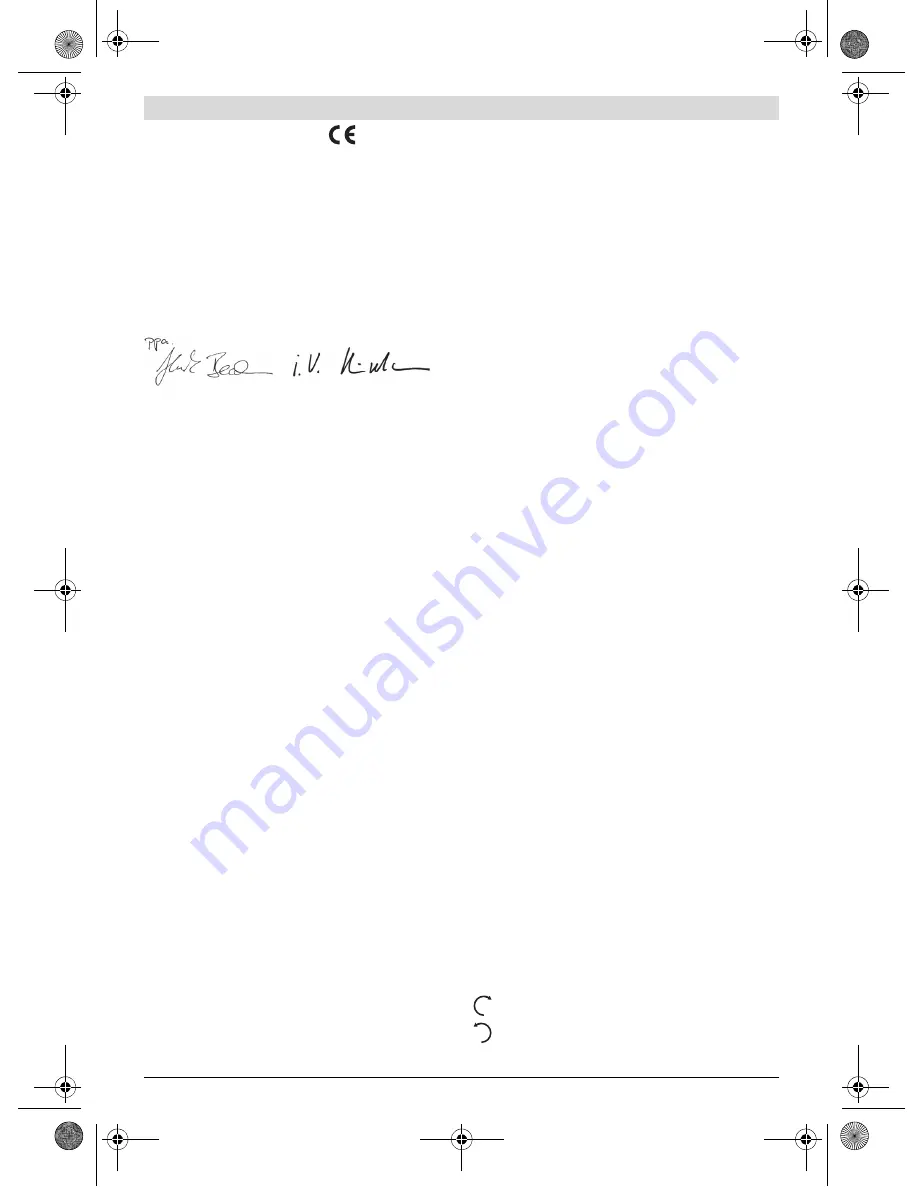
English |
17
Bosch Power Tools
3 609 929 C44 | (6.12.13)
Declaration of Conformity
We declare under our sole responsibility that the product de-
scribed under “Technical Data” is in conformity with the fol-
lowing standards or standardization documents:
EN ISO 11148 according to the provisions of the directive
2006/42/EC.
Technical file (2006/42/EC) at:
Robert Bosch GmbH, PT/ETM9,
D-70745 Leinfelden-Echterdingen
Robert Bosch GmbH, Power Tools Division
D-70745 Leinfelden-Echterdingen
Leinfelden, 01.07.2013
Assembly
Devices for Safe Handling
If you want to operate the pneumatic tool in a suspen-
sion device or a clamping fixture, take care to fasten it
in the device/fixture first before connecting it to the air
supply.
This measure prevents accidental starting of oper-
ation.
Suspension Device
With the utility clip
3
, you can fasten the pneumatic tool to a
suspension device.
– Screw the upper, front screws
1
with an Allen key (see
“Technical Data”) in an anticlockwise direction from the
housing of the pneumatic tool. Remove the washers
2
and
place them onto the screws
1
. Firmly screw the utility clip
3
with the screws and washers in a clockwise direction on
the housing of the pneumatic tool.
Regularly check the condition of the utility clip and the
hook of the suspension device.
Connecting the Air Supply
Ensure that the air pressure is not lower than 6.3 bar
(91 psi) because the pneumatic tool is designed for
this operating pressure.
For maximum performance, the values for the inner hose di-
ameter as well as the connection threads must be adhered to
as listed in the “Technical Data” Table. To maintain the full
performance, only use hoses with a maximum length of 4 m.
The compressed air supplied should be free of foreign materi-
al and moisture to protect the tool from damage, contamina-
tion, and the formation of rust.
Note:
The use of a compressed-air maintenance unit is neces-
sary. This ensures proper function of the pneumatic tools.
Observe the operating instructions of the maintenance unit.
All fittings, connecting lines and hoses must be dimensioned
for the pressure and the required air volume.
Avoid restrictions in the air supply, e.g., from pinching, kink-
ing, or stretching!
When in doubt, check the pressure at the air inlet with a pres-
sure gauge with the pneumatic tool switched on.
Connecting the Air Supply to the Pneumatic Tool
(see figure A)
– Remove the closing cap
6
from the connection socket at air
inlet.
– Screw hose fitting
7
into the connection socket at air inlet
5
.
To avoid damage to interior valve components of the pneu-
matic tool when screwing hose fitting
7
in or out, it is rec-
ommended to counter-hold the projecting connection
socket of air intake
5
with an open-end wrench (size
22 mm).
– Loosen hose clamp
13
of supply-air hose
14
, mount the
supply-air hose to hose fitting
7
and retighten the hose
clamp.
Note:
Always mount the supply-air hose to the pneumatic tool
first, then to the maintenance unit.
Changing the Tool
When working with an application tool, pay attention
that the application tool is firmly seated on the tool
holder.
When the application tool is not firmly connected
with the tool holder, it can come loose again and not be
controlled.
Inserting
– Slide the application tool
12
over the square drive of the
tool holder
10
. Pay attention that the snap ring
11
locks in
the groove of the application tool.
Use only application tools with an appropriate shank end (see
“Technical Data”).
Do not use adapters.
Removing
– Pull off the application tool
12
from the tool holder
10
. A
seized application tool can be loosened by applying light
blows with a rubber hammer.
Operation
Starting Operation
The pneumatic tool works optimally at a working pressure of
6.3 bar (91 psi), measured at the air inlet when the pneumat-
ic tool is switched on.
Pay attention to the direction of rotation that is set, be-
fore switching on the pneumatic tool.
For example,
when a screw is to be loosened and the direction of rota-
tion is set so that the screw is tightened, this can lead to a
strong uncontrolled movement of the pneumatic tool.
Setting the Direction of Rotation and the Torque
(see figure B)
The rotational direction switch
4
is used both for setting the
direction of rotation as well as for setting the torque.
Henk Becker
Executive Vice President
Engineering
Helmut Heinzelmann
Head of Product Certification
PT/ETM9
“Forward” stands for right rotation.
“Reverse” stands for left rotation.
F
R
OBJ_BUCH-275-003.book Page 17 Friday, December 6, 2013 3:12 PM