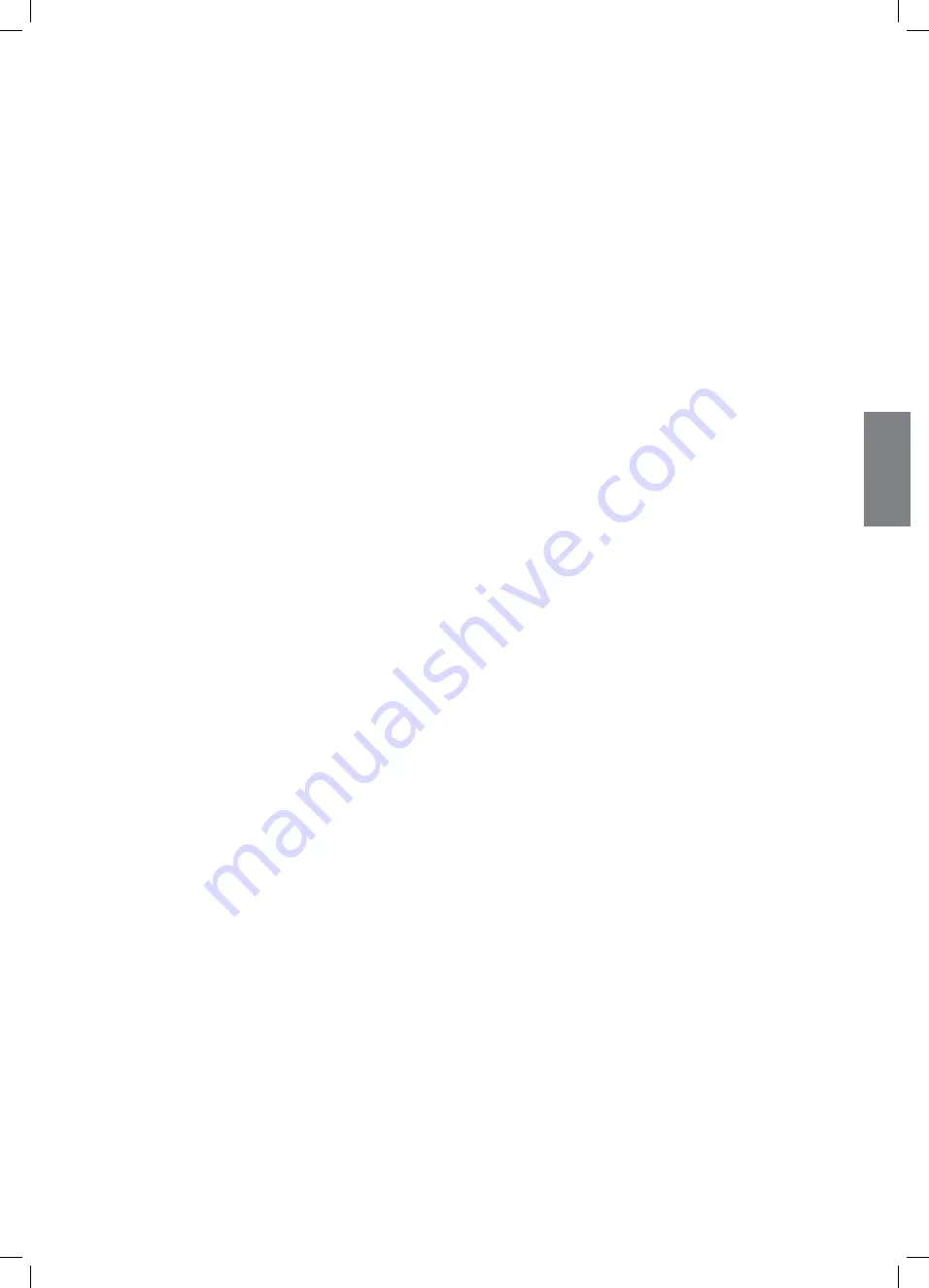
Operation 41/64
3 842 358 792/2016-12, Material and information fl ow technology: HQ 2/C-H, HQ 4,
Bosch Rexroth AG
9.1.4 Environmental
infl uences
• Our products are resistant to many media that are commonly found in manufacturing,
such as water, mineral base oil, grease and detergents. Contact your Rexroth
representative if you have any doubts about resistance to specifi c chemicals, such as
test oil, doped oils, aggressive cleaning agents, solvents or brake fl uid.
• Avoid prolonged contact with highly reactive acidic or alkaline materials.
• Contamination – specifi cally from abrasive media from the surrounding area, such
as sand and silicates, e.g., from construction as well as machining processes in
the transfer system (e.g., welding beads, pumice powder, glass shards, chips,
waste parts, etc.) – can greatly increase wear. Maintenance intervals should be
signifi cantly reduced under these circumstances.
• Resistance to media and contamination does not mean that functional safety is
guaranteed in every case.
– Liquids that thicken as they evaporate and become highly viscous or adhesive can
lead to malfunctions.
– If they get carried onto systems with rollers, media which have a lubricating effect
can lead to a reduction in the motor power that can be transmitted via friction.
In such instances, special care must be taken when planning the system, and the
maintenance intervals must be correspondingly shortened.
EN
GLISH
551261_2016_12_EN.indd 41
551261_2016_12_EN.indd 41
22.12.2016 10:26:36
22.12.2016 10:26:36