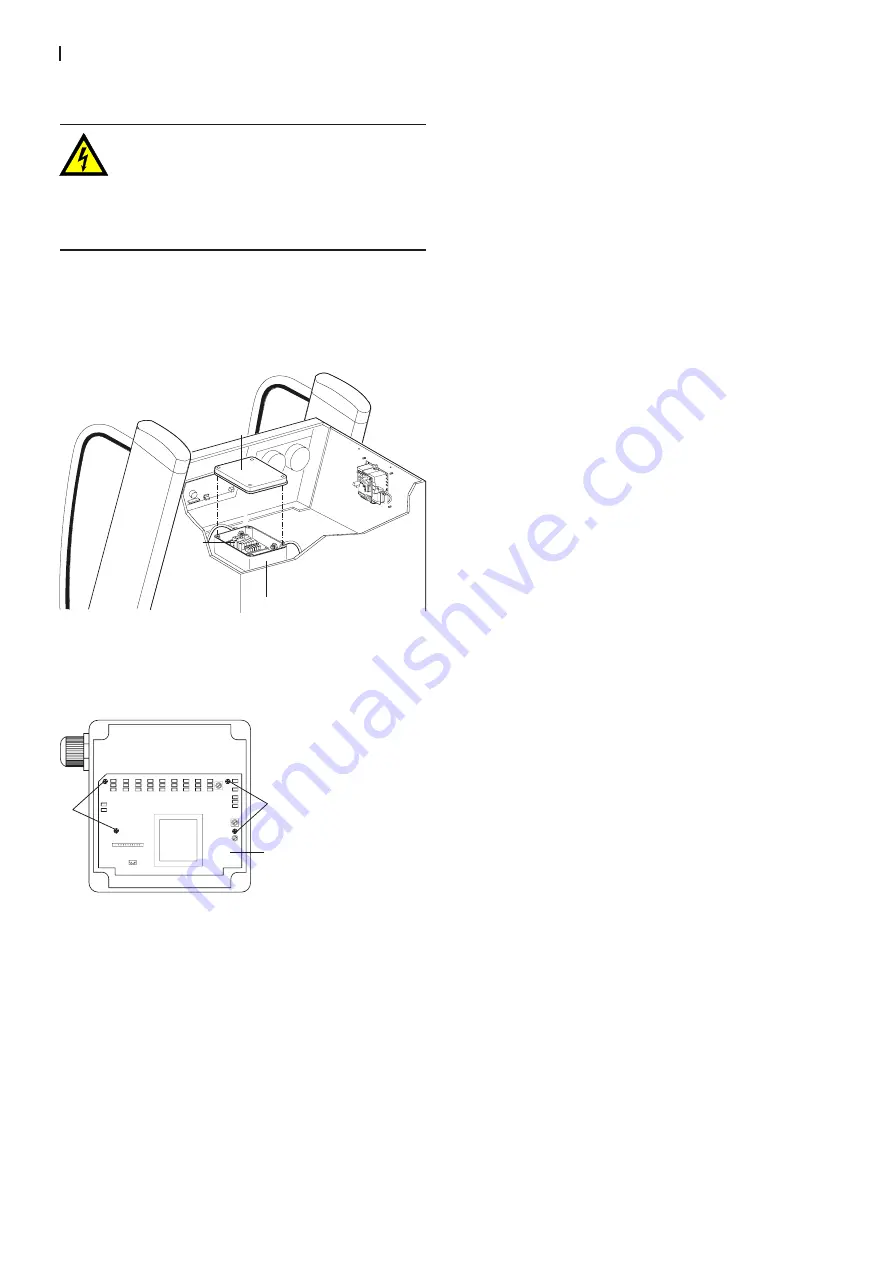
1 689 975 197 (2006-09-22)
Robert Bosch GmbH
en
16
ACS 500
9.
Replacing the actuation circuit board
Danger - Electric shock hazard
Touching live parts of the master switch or on the
actuation circuit board can result in serious injury
or death.
Remove mains connector.
Secure master switch with a padlock.
Procedure:
1. Turn off ACS 500 at master switch.
2. Remove mains connector.
3. Remove electronic compartment cover.
45
97
86
_1
8
1
2
3
Fig. 10: Connection box
4. Place housing cover (1) from connection box (2).
5. Disconnect all connecting leads from the actuation
circuit board (3).
459786_26
4
4
5
Fig. 11: Connection box
6. Remove bolts (4).
7. Take out actuation circuit board (5).
8. Install new actuation circuit board in connection box.
9. Secure actuation circuit board with bolts (4).
10. Connect connecting lead for control/display unit and if
necessary for printer. (See Section 12.1)
e
e
11. Connect wiring harness (see Section 12.2)
12. Place housing cover (1) on connection box and
secure.
13. Attach electronic compartment cover.