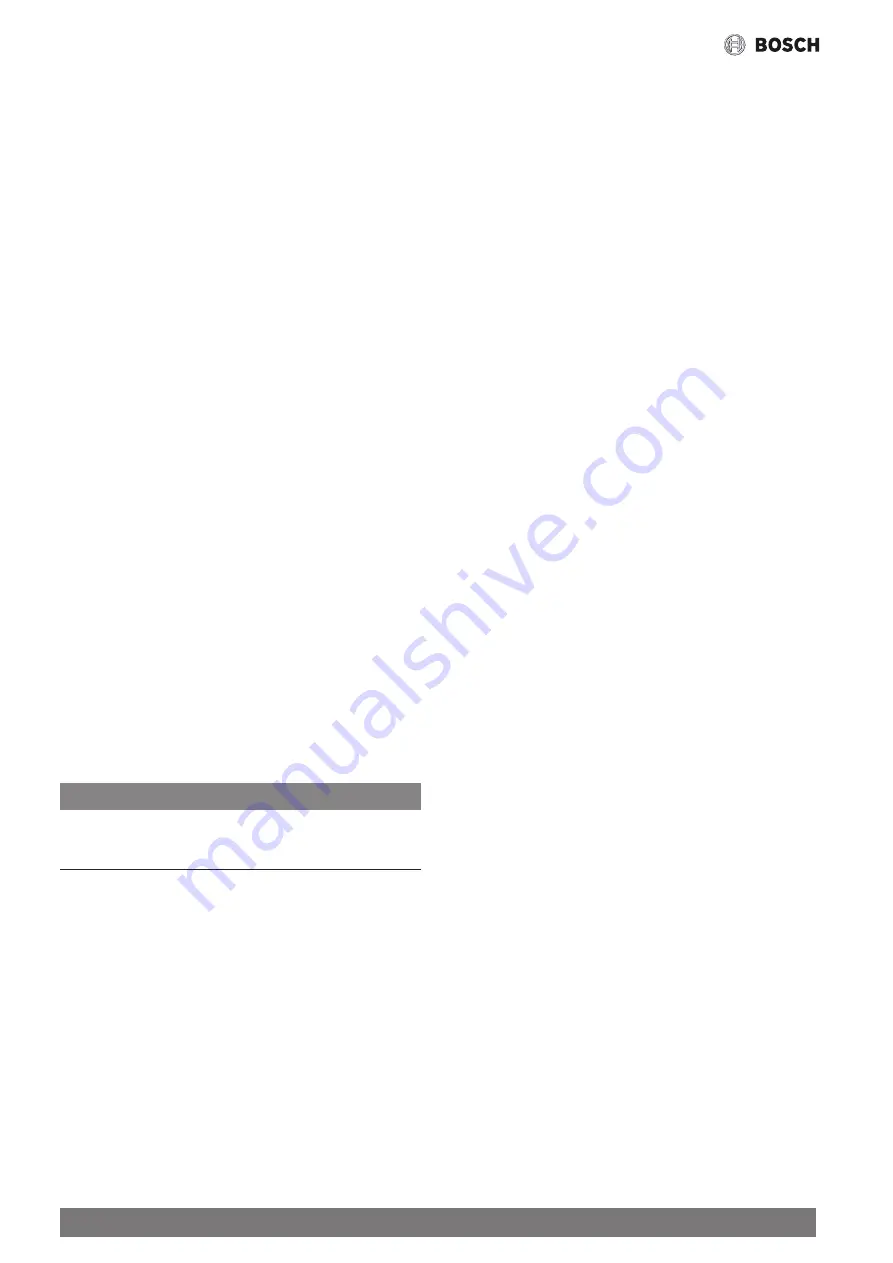
22
Climate 5000 MS – 6720887246 (2018/04)
Information on Servicing
•
labelling and signs that are illegible shall be corrected;
•
refrigeration pipe or components are installed in a position where
they are unlikely to be exposed to any substance which may corrode
refrigerant containing components, unless the components are
constructed of materials which are inherently resistant to being
corroded or are suitably protected against being corroded.
9. Checks to electrical devices
Repair and maintenance to electrical components shall include initial
safety checks and component inspection procedures. If a fault exists that
could compromise safety, then no electrical supply shall be connected
to the circuit until it is satisfactorily dealt with. If the fault cannot be
corrected immediately and it is necessary to continue operation, an
adequate temporary solution shall be used. This shall be reported to the
owner of the equipment so that all parties are advised.
Initial safety checks shall include:
•
that capacitors are discharged: this shall be done in a safe manner
to avoid possibility of sparking
•
that there no live electrical components and that wiring is not
exposed while charging, recovering or purging the system;
•
that there is continuity of earth bonding.
10. Repairs to sealed components
10.1 During repairs to sealed components, all electrical supplies shall
be disconnected from the equipment being worked upon prior to
any removal of sealed covers, etc. If it is absolutely necessary to
have an electrical supply to equipment during servicing, then a
permanently operating form of leak detection shall be located at
the most critical point to warn of a potentially hazardous situation.
10.2 Particular attention shall be paid to the following to ensure that
when working on electrical components, the casing is not altered in
such a way that the level of protection is affected. This shall include
damage to cables, excessive number of connections, terminals not
made to original specification, damage to seals, incorrect fitting of
glands, etc.
•
Ensure that the apparatus is mounted securely.
•
Ensure that seals or sealing materials have not degraded such
that they no longer serve the purpose of preventing the ingress
of, flammable atmospheres. Replacement parts shall be in
accordance with the manufacturer s specifications.
NOTE:
The use of silicon sealant may inhibit the effectiveness of some types of
leak detection equipment. Instrinsically safe components do not have to
be isolated prior to working on them.
11. Repair to intrinsically safe components
Do not apply any permanent inductive or capacitance loads to the
circuit without ensuring that this will not exceed the permissible voltage
and current permitted for the equipment in use. Intrinscially safe
components are the only types that can be worked on while live in the
presence of a flammable atmosphere. The test apparatus shall be at the
correct rating.
Replace components only with parts specified by the manufacturer.
Other parts may result in the ignition of refrigerant in the atmosphere
from a leak.
12. Cabling
Check that cabling will not be subject to wear, corrosion, excessive
pressure, vibration, cutting by sharp edges or any other adverse
environmental effects. The check shall also take into account the effects
of aging or continual vibration from sources such as compressors or
fans.
13. Detection of flammable refrigerants
Under no circumstances shall potential sources of ignition be used in the
search for or detection of refrigerant leaks. A halide torch (or any other
detector using a naked flame) may not be used.
14. Leak detection methods
The following leak detection methods are deemed acceptable for
systems containing flammable refrigerants. Electronic leak detectors
shall be used to detect flammable refrigerants, but their sensitivity may
not be adequate, or may need re-calibration. (Detection equipment
shall be calibrated in a refrigerant-free area.) Ensure that the detector
is not a potential source of ignition and is suitable for the refrigerant.
Leak detection equipment shall be set at a percentage of the LFL of the
refrigerant and shall be calibrated to the refrigerant employed and the
appropriate percentage of gas (25% maximum). Leak detection fluids
are suitable for use with most refrigerants, but the use of detergents
containing chlorine shall be avoided. Chlorine may react with the
refrigerant and corrode the copper pipe-work.
If a leak is suspected, all naked flames shall be removed or extinguished.
If a leakage of refrigerant is found which requires brazing, all of the
refrigerant shall be recovered from the system, or isolated (by means of
shut off valves) in a part of the system remote from the leak. Oxygen-free
nitrogen (OFN) shall then be purged through the system both before and
during the brazing process.
15. Removal and evacuation
When breaking into the refrigerant circuit to make repairs for any
other purpose, conventional procedures shall be used. However, it is
important that best practice is followed since flammability needs to be
considered. The following procedure shall be adhered to:
1) remove refrigerant;
2) purge the circuit with inert gas;
3) evacuate;
4) purge again with inert gas;
5) open the circuit by cutting or brazing.
The refrigerant charge shall be recovered into the correct recovery
cylinders. The system shall be flushed with OFN to render the unit safe.
You may have to repeat this process several times. Compressed air or
oxygen shall not be used for this task.
Flushing shall be achieved by breaking the vacuum in the system with
OFN and by continuing to fill until the working pressure is achieved. Then
vent to atmosphere, and finally pull down to a vacuum. This process
shall be repeated until no refrigerant is within the system anymore.
When the final OFN charge is used, the system shall be vented down
to atmospheric pressure so that work can take place. This operation is
absolutely vital if brazing operation on the pipe-work is to take place.
Ensure that the outlet for the vacuum pump is not closed to any ignition
sources and that ventilation is available.
16. Charging procedures
In addition to conventional charging procedures, the following
requirements shall be adhered to:
•
Ensure that contamination of different refrigerants does not occur
when using charging equipment. Hoses or lines shall be as short as
possible to minimise the amount of refrigerant contained in them.
•
Cylinders shall be kept upright.
•
Ensure that the refrigeration system is earthed prior to charging the
system with refrigerant.
•
Label the system when charging is complete (if not already).
•
Extreme care shall be taken not to overfill the refrigeration system.