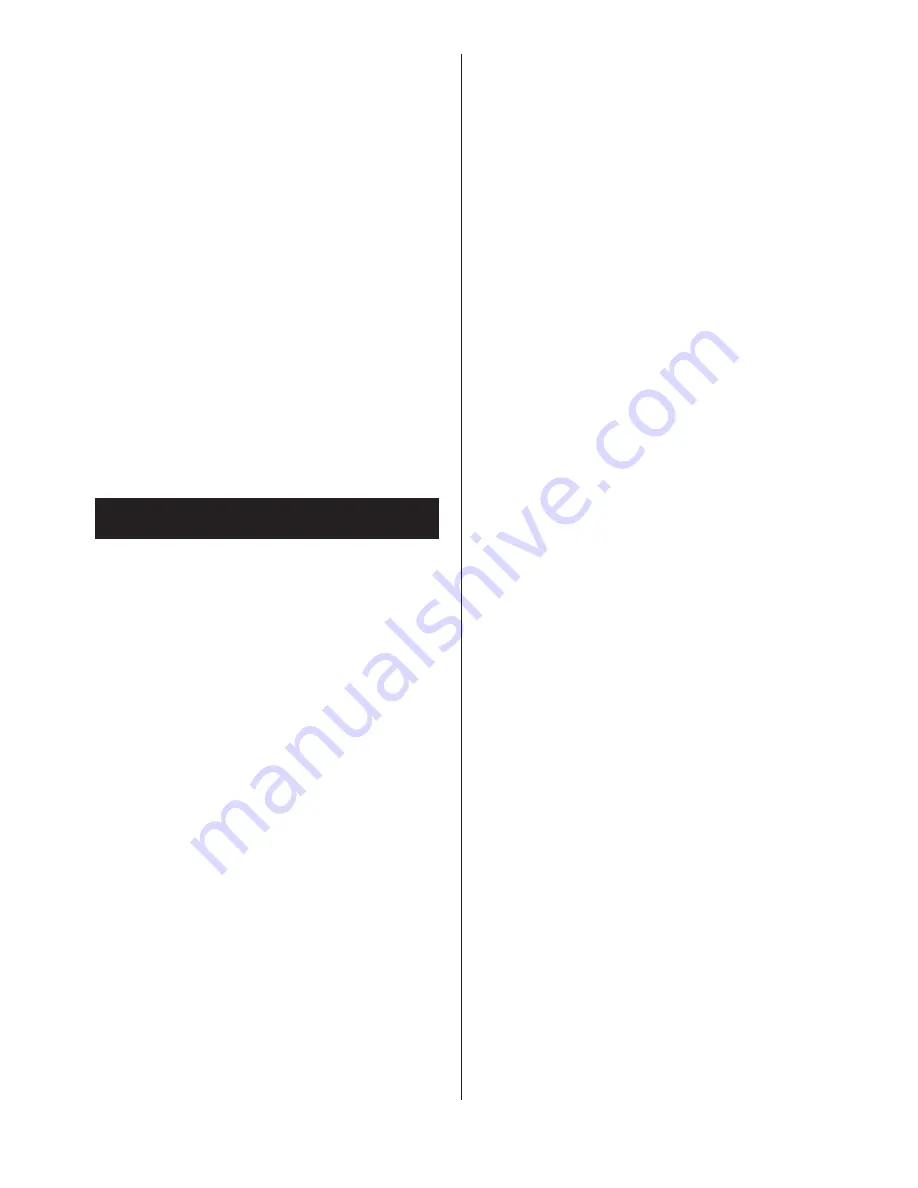
Connect a drain to the relief valve outlet ensuring that it does not
discharge onto electric components or where it might be a
hazzard. The pipe must be not less than 15mm in diameter.
Make the electrical connections to the appliance through the
cable clamps in the base of the appliance.
Remove the drop-down facia cover by lowering it to the
horizontal position and pushing firmly upwards at the rear
supports to release the cover. Lift the cover from the appliance.
Remove the clipped on-cover and unscrew the inner cover to
expose the connectors. Refer to Fig.16.
Remove the automatic air vent cap. See Fig. 14.
Check that all the gas and water connections on the manifold are
tight.
Final Installation.
Replace the cabinet front panel.
Refer to Section 13 Commissioning, for a full discription of the
filling, venting and pressurisation of the system.
If the appliance is not to be commissioned immediately then
check that the gas supply, the electrical supply and all the water
connections are turned off.
If the premises are to be left unoccupied in very frosty conditions
then drain any water from the appliance and the system
Test the gas supply for soundness as described in BS 6891.
If the appliance is not to be commissioned immediately replace
the cabinet. Turn off the gas, electrical and water connections.
The appliance is adjusted at the factory to give the settings
shown in table 7.
If any changes are made to these settings they must be recorded
on the commissioning label to be fixed to the appliance and in
the relevant booklet.
The domestic hot water discharge temperature and the central
heating flow temperature may be adjusted on the facia to satisfy
different conditions.
Domestic Hot Water
Confirm that the mains water supply has been flushed out at
installation. If not it will be necessary to disconnect the cold
water inlet pipe at the appliance and thoroughly flush.
Central Heating
Confirm that the central heating system has been fully
flushed out at installation. If not then thoroughly flush the
system using clean water if possible. Any additives must be
compatible with aluminium heat exchangers.
The system water must not have a pH greater than 8 or the
appliance guarantee will be rendered invalid. If any system water
treatment is required then only products suitable for use with
Aluminium shall be used i.e. Fernox-Copal or Sentinel X100, in
accordance with the manufacturers instructions. The use of any
other substances will invalidate the guarantee.
Gas Service
The complete system, including the meter, must be inspected
and tested for soundness and purged as described in BS 6891.
Check that the gas and electrical supplies to the appliance are
turned off.
Check that any controls are in the off position.
Check that all the water connections throughout the system are
tight.
Remove the cabinet by unclipping the two clips and lifting away.
Refer to Fig.12.
Remove the automatic air vent caps. Refer to Fig.14.
Open the heating system valves on the manifold and all the
radiator valves. Fill the system through the WRc approved filing
connection to a pressure of about 1.5 bar and check for water
soundness. Refer to Fig.6 and 7. The automatic air vents on the
appliance will remove air from the appliance but each radiator
must be vented separately. The manual air vent must be open to
allow the venting of the appliance. Tighten the screw when
venting is complete. Refer to Fig.15.
Fill the condensate trap by opening the manual air vent/siphon
fill connection until water is discharged showing that the siphon
is full. Refer to Fig.15.
Check that the pressure relief valve operates by, after removing
the cap, turning the knob anti-clockwise until it releases and
water is expelled from the discharge pipe. The relief valve is
located beneath and behind the pump at the right-hand side.
Remove the plated cap from the pump and turn the shaft about
half a turn using a flat blade screwdriver. Replace the cap. Refer
to Fig.15.
Set the system pressure to 1bar by releasing water from the relief
valve and, if necessary, the expansion vessel pressure.
The 10 L expansion vessel, supplied with a charge pressure of
0.75 bar (static head 7.5 metres), must not be at a pressure less
than the static head of the system. A schraeider type valve is
provided on top of the vessel if it is necessary to increase the
charge pressure.
Refer to BS7074:1 and Table 9 for details of the allowable system
capacity.
If the system volume is greater than that which can be
accomodated by the expansion vessel on the appliance then an
extra vessel must be fitted as close to the appliance as possible
in the central heating return. It must be charged to the same
pressure as the vessel in the appliance.
Connect a pressure gauge to the gas valve inlet pressure test
point and open the gas tap. See Fig. 19.
Set all the external system controls to on or maximum.
Set the central heating and domestic hot water control knobs to
minimum. Check that the condensate trap and syphon are full
(to prevent flue gas spillage).
The appliance must NOT be operated without the siphon
being full.
The instructions following describe the operation of the
appliance.
13. Commissioning
15
Summary of Contents for Greenstar ZWBR 11-25 A31
Page 31: ...31 ...