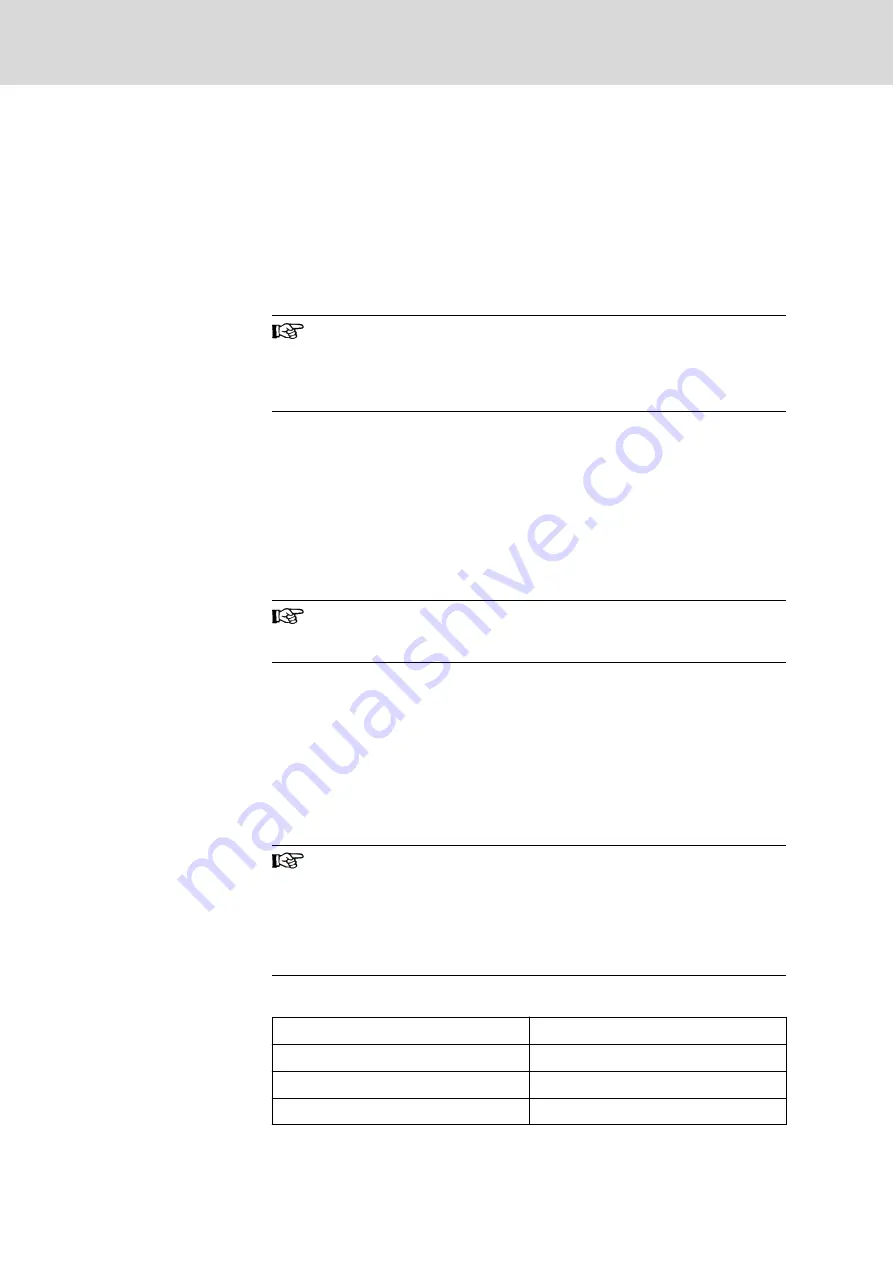
incremental and absolute, EnDat2.1, EnDat2.2, Hiperface) and SinCos
encoders also use these +5 Volt digital inputs. This means that a BLDC
motor with +5 Volt Hall sensors and a digital encoder cannot be used on the
same axis.
There is one exception. A SinCos encoder can be used together with a BLDC
motor with +5 Volt Hall sensors on axis0.
If the Hall sensors of the BLDC motor are connected to the +24 Volt digital
inputs, the digital encoders (Rexroth MSM incremental and absolute, SinCos,
EnDat2.1, EnDat2.2 and Hiperface) can always be used on either axis.
If a motor is connected on axis1 with an encoder that uses the
digital input lines (Rexroth MSM incremental and absolute
encoders, EnDat2.x or Hiperface), you cannot use a BLDC motor
on axis0. This combination will cause an error on axis0 ("invalid
Hall sensor").
The NYCe 4000 software includes functions to switch the encoder power
supply on and off per axis. However, the encoder power supply pin Enc5V0
and Enc5V1 are connected in parallel on the NY4120 drive module. This
means that whenever the encoder power supply for one of the axes is
switched on, the encoder power supply for the other axis is also switched on.
Only when the encoder power supply for both axes is switched off, pins
Enc5V0 and Enc5V1 are switched off.
For detailed connection information, see
.
Do not connect or disconnect the encoders while the system
power supply is switched on. This can destroy the encoder
electronics.
8.14
Drive Output
8.14.1
Characteristics
Two PWM amplifiers with four half H-bridges are used as current amplifiers
on the NY4120. During the active part of the PWM cycle, the drive power
voltage is applied to the motor connections. During the passive part of the
PWM cycle, the half H-bridges are in a freewheel mode and current
measurements are done.
When the logic power supply voltage drops below the required
minimum voltage while a motor is running, the NYCe 4000
system is designed to stop the motor. Stopping the motor is
achieved by creating a short circuit condition through the FETs of
the H-bridge. This will not cause problems with small motors, but
if the module drives a motor with a high amount of kinetic energy,
the FETs can be destroyed by this energy.
Characteristic
Description
PWM frequency
16 kHz … 96 kHz
PWM duty cycle
Minimum OFF time: 1 µs
PWM resolution
12 bits
78/233
NY4120 and NY4120/10: PWM Drive Module
NYCe 4000 Multi-axis motion control system Hardware Sys‐
tem Manual
Bosch Rexroth AG R911337671_Edition 18