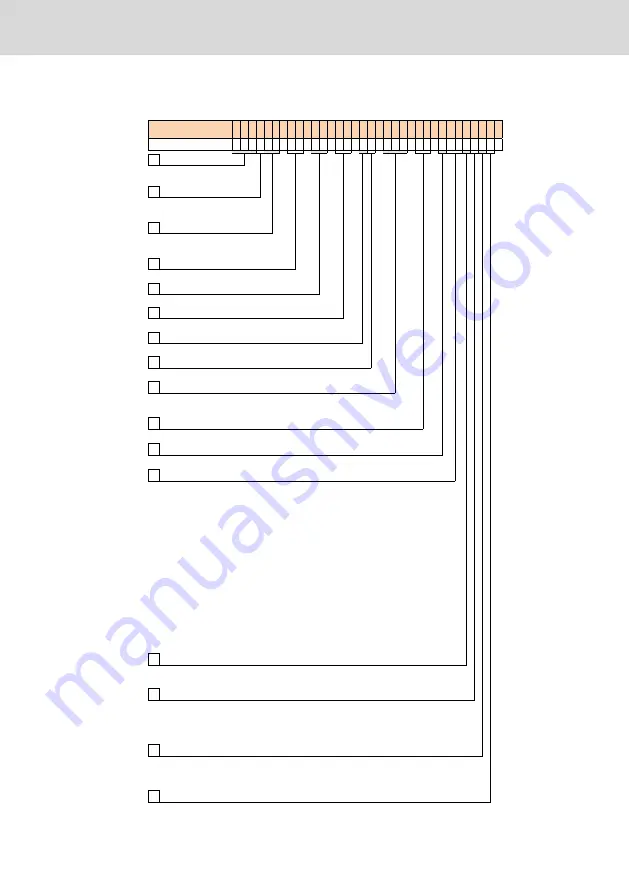
15.1 Type code
Type
1 2 3 4 5 6 7 8 9
1
0 1 2 3 4 5 6 7 8 9
2
0 1 2 3 4 5 6 7 8 9
3
0 1 2 3 4
Example: X M 2 2 0 0 . 0 1 - 0 1 - 3 1 - 3 1 - 0 0 1 - N N - 1 0 1 N 3 N N
Product
IO Box, modular,
Perf.class.........= XM2
CPU
Basic............................ = 1
Standard ...................... = 2
Variant
BR Standard ....................= 00
Extended certifications.....= 01
Design
FPGA / Memory 512 MB............. = 01
Feldbus on-board
Sercos Master (MultiEthernet) .............. = 01
Interfaces (ETH, USB)
ETH 1 GBit, USB Host and Device ..................= 31
Remanent Memory
Min. 128 kB ................................................................= 3
Mass storage
Min. 1 GB ...................................................................... = 1
Hardware expandability
0 x Extension-Module S20-IO............................................... = 001
3 x Extension-Module S20-IO............................................... = 301
Housing design
Standard..............................................................................................= NN
System configuration
IndraMotion MLC ............................................................................................ = 1
Basic system (Function package)
PLC ....................................................................................................................= 00
PLC + MOT ........................................................................................................= 01
PLC + MOT + TEC .............................................................................................= 02
PLC + MOT + ROCO..........................................................................................= 03
PLC + MOT + TEC + ROCO...............................................................................= 04
PLC + MOT + HYD.............................................................................................= 05
PLC + MOT + TEC + HYD..................................................................................= 06
PLC + MOT + ROCO + HYD ..............................................................................= 07
PLC + MOT + TEC + ROCO + HYD ...................................................................= 08
PLC + MOTB ......................................................................................................= 11
PLC + MOTB + TEC...........................................................................................= 12
PLC + MOTB + ROCOB.....................................................................................= 13
PLC + MOTB + TEC + ROCOB..........................................................................= 14
PLC + MOTB + HYD ..........................................................................................= 15
PLC + MOTB + TEC + HYD ...............................................................................= 16
PLC + MOTB + ROCOB + HYD .........................................................................= 17
PLC + MOTB + TEC + ROCOB + HYD ..............................................................= 18
Field bus prot. f. MultiEthernet
None........................................................................................................................ = N
EtherCAT - Master................................................................................................... = 1
Communication (Function package)
None.............................................................................................................................= N
OPC UA........................................................................................................................= 1
OCI...............................................................................................................................= 2
OPC UA + OCI .............................................................................................................= 3
Application (Function package)
None...............................................................................................................................= N
JAVA ..............................................................................................................................= 1
JAVA + WebConnector...................................................................................................= 2
Reserve
None...................................................................................................................................= N
Remanent Memory
Min. 128 kB ............................................................... = 3
short description
01
02
03
04
05
06
07
08
09
10
11
12
13
14
15
16
Fig. 15-1: Type code
IndraControl XM21, XM22 Controls
61/69
Ordering information
R911340667_Edition 04 Bosch Rexroth AG
Summary of Contents for Rexroth IndraControl XM21
Page 1: ...IndraControl XM21 XM22 Controls Operating Instructions R911340667 Edition 04 ...
Page 6: ...IV IndraControl XM21 XM22 Controls Bosch Rexroth AG R911340667_Edition 04 ...
Page 70: ...64 69 IndraControl XM21 XM22 Controls Bosch Rexroth AG R911340667_Edition 04 ...
Page 73: ...IndraControl XM21 XM22 Controls 67 69 R911340667_Edition 04 Bosch Rexroth AG ...
Page 74: ...68 69 IndraControl XM21 XM22 Controls Bosch Rexroth AG R911340667_Edition 04 ...