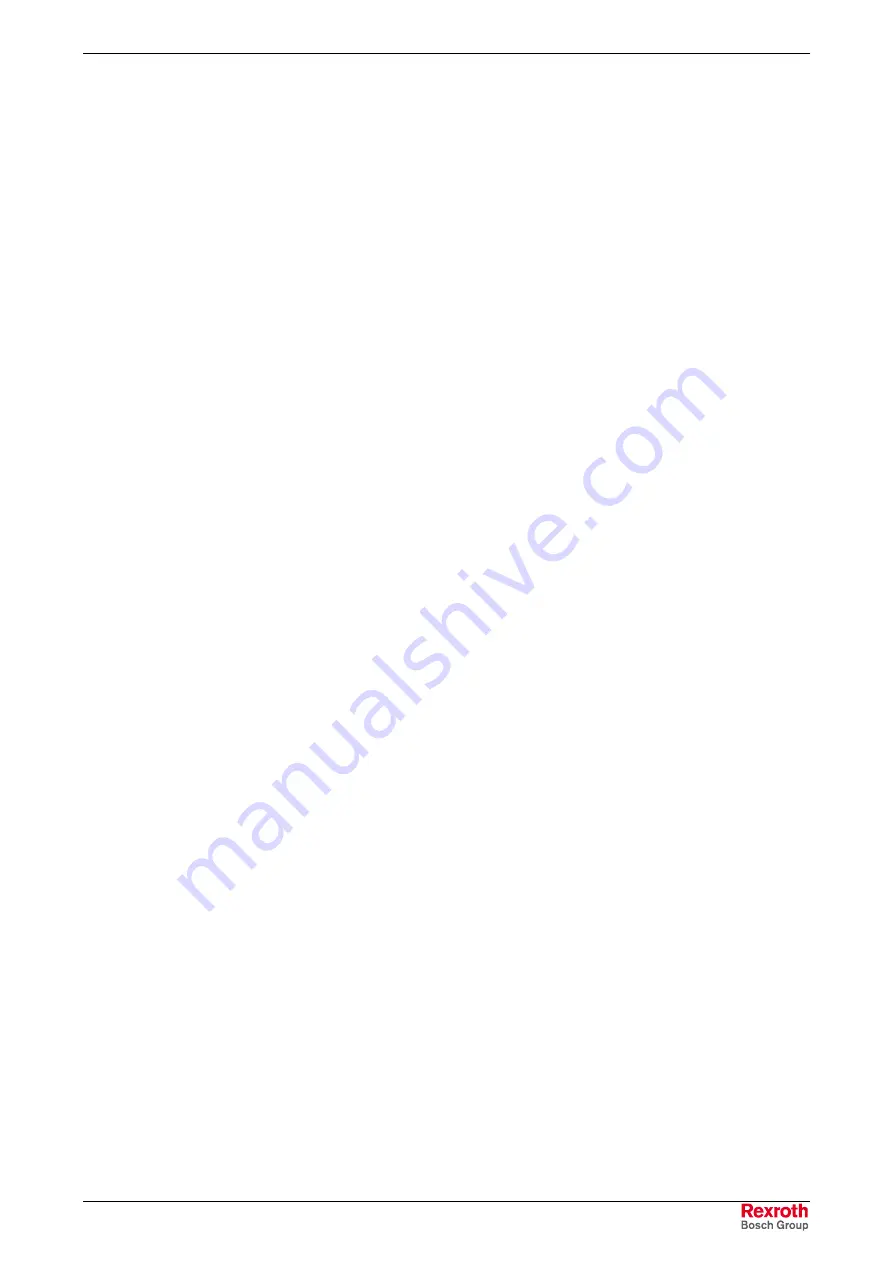
Rexroth IndraDrive
Electrical Installation
7-3
DOK-INDRV*-HMV-*******-PR01-EN-P
10 Rules for EMC-Correct Installation of Drives
The following 10 rules are the basics for designing drive systems in
compliance with EMC.
Rules 1 to 7 are generally valid. Rules 8 to 10 are especially important to
limit noise emission.
All metal parts of the cabinet should be connected with one another
through the largest possible surface area so that the best electrical
connection is established (not paint on paint!). If required, use serrated
washers which cut through the paint surface. The cabinet door should be
connected to the cabinet using the shortest possible grounding straps.
Signal, line supply, motor and power cables should be routed away from
another (this eliminates mutual interference!). The minimum clearance is:
10 cm. Barriers should be provided between power- and signal cables.
These barriers should be grounded at several locations.
Contactors, relays, solenoid valves, electromechanical operating hour
counters etc. in the cabinet must be provided with noise suppression
devices. These devices must be connected directly at the coil.
Non-shielded cables belonging to the same circuit (feeder and return
cables) should be twisted with the smallest possible distance between
them. Cores which are not used must be grounded at both ends.
Generally, interference injection can be reduced by routing cables as
close as possible to grounded sheet steel panels. For this reason, cables
and wires should not be routed freely in the cabinet, but as close as
possible to the cabinet itself and the mounting panels. This is also true for
reserve cables.
Incremental encoders must be connected using shielded cables. The
shield must be connected at the incremental encoder and at the drive
controller through the largest possible surface area. The shield may not
be interrupted, e.g. using intermediate terminals.
The shields of signal cables must be connected to ground at both ends
through the largest possible surface area to establish a good electrical
connection (transmitter and receiver). If the potential bonding between the
screen connections is poor, to reduce the shield current, an additional
potential bonding conductor with a cross-section of at least 10 mm²
should be connected in parallel with the shield. The shield can be
connected to ground (=cabinet housing) at several locations. This is also
true outside the cabinet. Foil shields are not recommended. Braided
screens provide a better shielding effect (factor of 5).
If the potential bonding is poor, analog signal cables may only be
grounded at one end to the drive controller in order to prevent low-
frequency noise being injected into the screen (50 Hz).
Always locate a radio interference suppression filter close to the noise
source. The filter should be connected through the largest possible
surface area with the cabinet housing, mounting panel etc. The best
solution is a bare metal mounting panel (e.g. manufactured from stainless
steel, galvanized steel), as the complete mounting surface can be used to
establish good electrical contact.
The incoming and outgoing cables of the radio interference suppression
filter should be separated.
Rule 1
Rule 2
Rule 3
Rule 4
Rule 5
Rule 6
Rule 7
Rule 8
Summary of Contents for Rexroth IndraDrive HMV01.1E-W0030
Page 30: ...5 2 Transport and Storage Rexroth IndraDrive DOK INDRV HMV PR01 EN P Notes ...
Page 40: ...6 10 Mechanical Mounting Rexroth IndraDrive DOK INDRV HMV PR01 EN P Notes ...
Page 88: ...9 8 Control Mains Contactor Rexroth IndraDrive DOK INDRV HMV PR01 EN P Notes ...
Page 122: ...13 22 Appendix Rexroth IndraDrive DOK INDRV HMV PR01 EN P Fig 13 25 HFD01 2 480 0026 ...
Page 123: ...Rexroth IndraDrive Appendix 13 23 DOK INDRV HMV PR01 EN P Fig 13 26 HFD02 2 480 0026 ...
Page 130: ...14 6 Index Rexroth IndraDrive DOK INDRV HMV PR01 EN P Notes ...
Page 131: ......