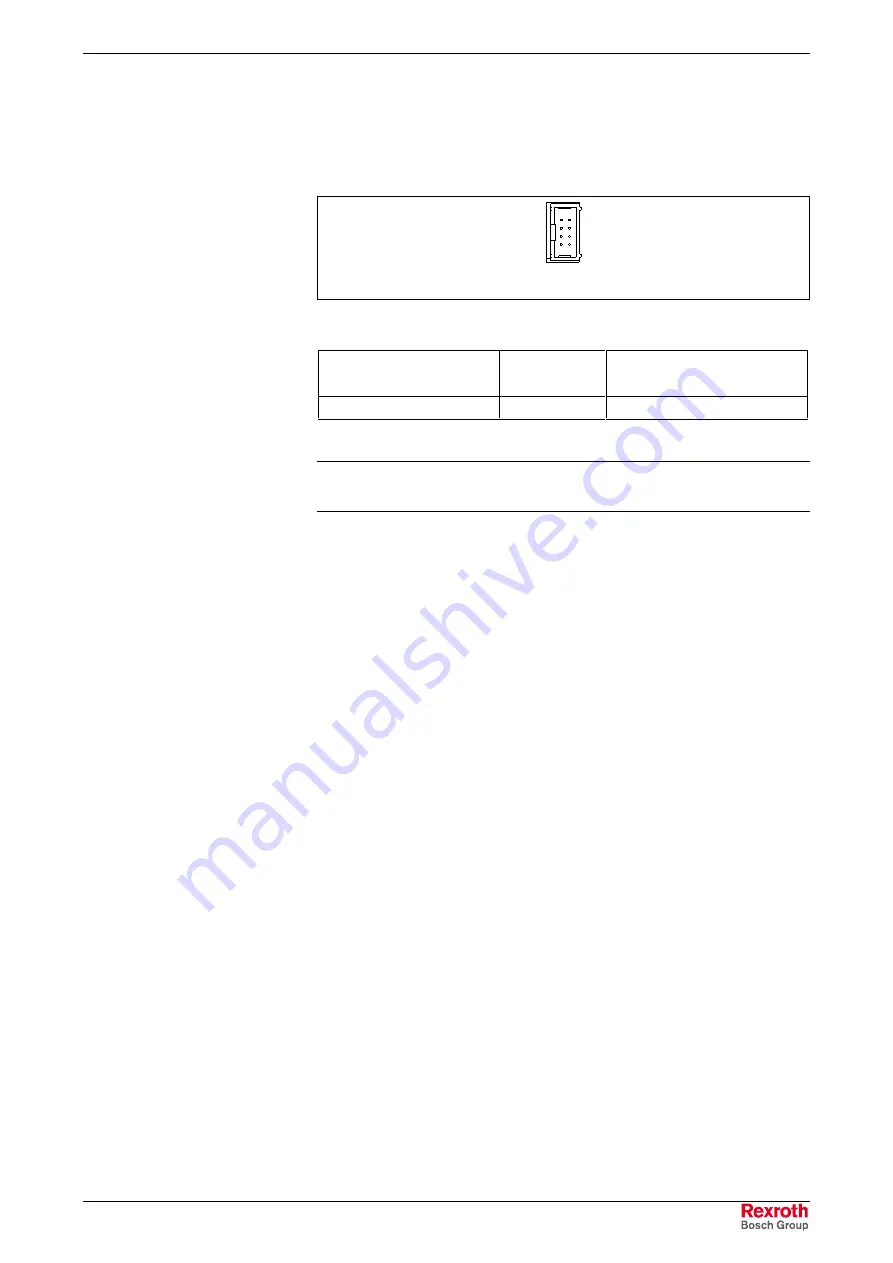
Rexroth IndraDrive
Electrical Installation
7-21
DOK-INDRV*-HMV-*******-PR01-EN-P
X1, Bus Module
The bus module permits data exchange between the supply unit and the
drive controllers.
X1_hmv
Fig. 7-15:
X1
Type
Number of
poles
Type of design
Flat line connector
8
Connector on device
Fig. 7-16:
Design
Note:
If extension leads are used the leads must be shielded. Their
total length must not exceed a maximum of 40 m.
Graphic Representation
Design
Summary of Contents for Rexroth IndraDrive HMV01.1E-W0030
Page 30: ...5 2 Transport and Storage Rexroth IndraDrive DOK INDRV HMV PR01 EN P Notes ...
Page 40: ...6 10 Mechanical Mounting Rexroth IndraDrive DOK INDRV HMV PR01 EN P Notes ...
Page 88: ...9 8 Control Mains Contactor Rexroth IndraDrive DOK INDRV HMV PR01 EN P Notes ...
Page 122: ...13 22 Appendix Rexroth IndraDrive DOK INDRV HMV PR01 EN P Fig 13 25 HFD01 2 480 0026 ...
Page 123: ...Rexroth IndraDrive Appendix 13 23 DOK INDRV HMV PR01 EN P Fig 13 26 HFD02 2 480 0026 ...
Page 130: ...14 6 Index Rexroth IndraDrive DOK INDRV HMV PR01 EN P Notes ...
Page 131: ......