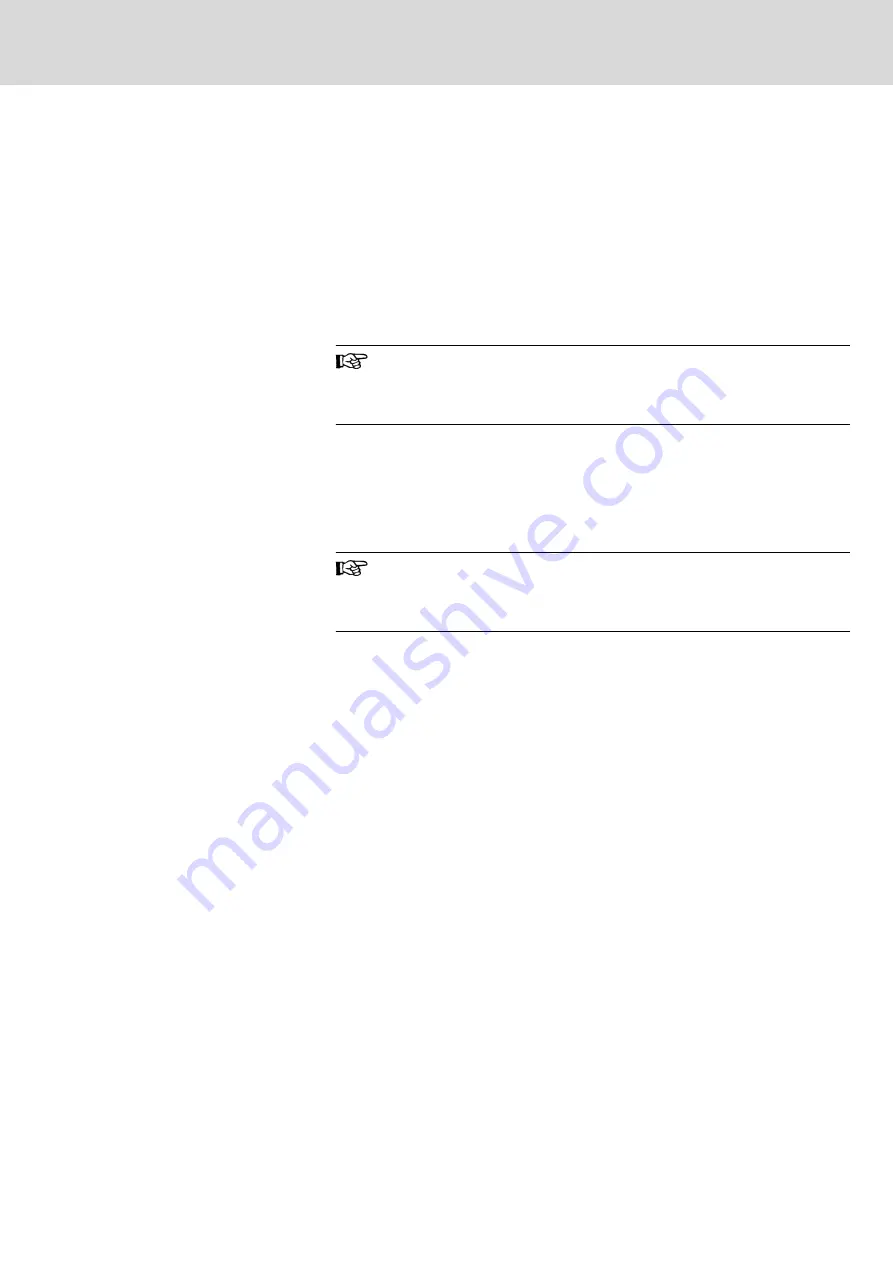
Special mode “Safe motion”
If special “Safe motion” modes are configured, they can be accepted accord‐
ing to the documentation mentioned above.
The following checks have to be carried out according to the configuration:
●
Transition into the special “Safe motion” mode
●
Individual activation time of enabling control
●
“Safely limited speed”
●
“Safely-monitored transient oscillation”
●
“Safe direction”
●
“Safely limited increment”
Please note that the monitoring functions refer to the externally
connected, safety-capable linear encoder, since it provides the
feedback in the case of a hazardous situation of the self-con‐
tained servo-hydraulic linear axis.
Error reaction
The error reaction of the self-contained servo-hydraulic linear axis can be ac‐
cepted according to the documentation mentioned above.
It must be checked, whether in the case of a safety technology fault the self-
contained servo-hydraulic linear axis can be stopped as configured and the
Safe Motion does not change to the escalation process, see
Please note that the monitoring functions refer to the externally
connected, safety-capable linear encoder, since it provides the
feedback in the case of a hazardous situation of the self-con‐
tained servo-hydraulic linear axis.
Safety zone and safe door locking
The acceptance can be carried out according to the documentation men‐
tioned above, if the self-contained servo-hydraulic linear axis is configured as
zone node or zone master and zone errors are generated or reactions to
zone errors take place.
In this dialog it can be checked whether the self-contained servo-hydraulic
linear axis generates a zone error or reacts to zone errors as configured.
Signal control of outputs
If the function of safe outputs is used, the documentation mentioned above
can be used for acceptance.
8.4.4
Escalation
Stopping of the self-contained servo-hydraulic linear axis in the last escala‐
tion level is carried out by the following actions:
●
Switching the motor torque off by activating the safety function "Safe tor‐
que off" (STO)
The connected motor is no longer supplied with energy and a pressure
buildup is thus prevented.
●
Closing of the two safety-related valves in the hydraulic retaining branch
by the safety function "Safe brake controller" (SBC)
By activating the SBC function the two valves are reliably deactivated
via the decentralized brake control module (HAT02.1-002).
●
De-energizing the switching outputs (closing of the functional valves)
Since the self-contained servo-hydraulic linear axis may only be stopped from
the safe functions of STO and SBC, the acceptance of the escalation level
has to be checked without use of the functional outputs. For this purpose the
enable valves such as, for example, A1 (valve of chamber 1) have to be kept
Operating Instructions
Bosch Rexroth AG
53/91
Self-contained servo-hydraulic linear axis Type SHA...
Commissioning