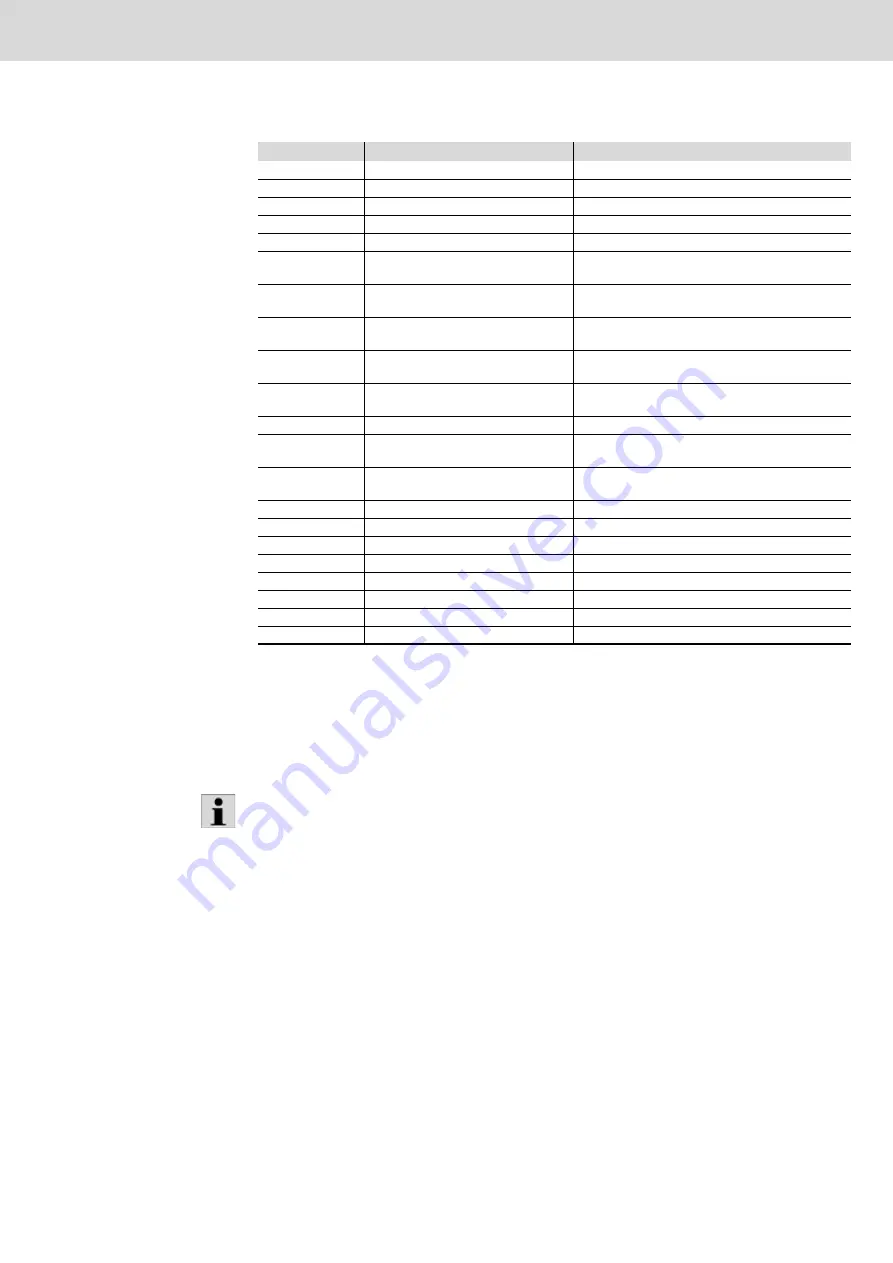
3 608 878 300
Tightening Technology |
Bosch Rexroth AG 175
System 350
| 3 608 878 300/2019-03
For an explanation of these signals, see chapter
Description of all PLC signals
.
5.5.2
Sequence
The following flow chart provides an overview of the sequence of the individual control signals and the
subsequent switching conditions between the beginning and end of a tightening process of a tightening
controller. Use of the individual PLC signals depends on the individual case of application, e.g. Setting of
CHxyPrg0...7.
CwLockAck
Clock wise lock acknowledge
Acknowledges that start is disabled
CwAck
Clock wise acknowledge
Acknowledges a start
CcwAck
Counter clock wise acknowledge
Acknowledges the Loosen program
SpDckAck
Spindle docking acknowledge
Acknowledges nutrunner replacement
AppOut 0-15
Application out bit 0-15
Application-specific output signal bit 0-15
ES LED Gr Ack
ErgoSpin LED Green acknowledge
Acknowledges that the green ErgoSpin LED has been
set.
ES LED Re Ack
ErgoSpin LED Red acknowledge
Acknowledges that the red ErgoSpin LED has been
set.
ES LED Ye Ack
ErgoSpin LED Yellow acknowledge
Acknowledges that the yellow ErgoSpin LED has
been set.
InCyEv
In cycle evaluation
Time period elapsing while tightening is active,
including completed evaluation
InCyCm
In cycle complete
Time period elapsing while tightening is active,
including evaluation and completed results output
CS ILOut
Compact System Indra Logic Out Bit
IL-specific output signal
ScanRxID IL
Scan ID Received (only with CS351…
IL)
Scanner ID recorded
Boxnut SelAck
Box nut selected acknowledge
Acknowledges selection of socket 0-7 from the
socket tray
Boxnut LEDAck
Box nut LED acknowledge
Acknowledges switchon of LED 0-7 in the socket tray
Job Ack 0-7
Job acknowledge
Acknowledges the selected job
Job CyCmp
Job finished
The job is finished
Job InCy
Job running
Activate job
Job Nok
Job Not Ok
The job results output is not okay
Job Ok
Job Ok
The job results output is okay
Job Rdy
Job ready
The job is ready
JobOut0-31
Job out bit
Job-specific output signal
1
As of version V2.600 of the Rexroth Tightening System 350, this signal is replaced by the MntTool signal.
Table 5–6:
PLC output signals for the tightening process of SE/CS
Signals
Function
Description
The following flow diagrams only apply to one tightening program. If tightening programs are linked, the
flow diagram is run through for every program.
Summary of Contents for Rexroth Tightening System 350
Page 4: ...4 641 Bosch Rexroth AG Schraubtechnik System 350 3 608 878 300 2019 03 ...
Page 120: ...120 641 Bosch Rexroth AG Tightening Technology 3 608 878 300 System 350 3 608 878 300 2019 03 ...
Page 194: ...194 641 Bosch Rexroth AG Tightening Technology 3 608 878 300 System 350 3 608 878 300 2019 03 ...
Page 638: ...638 641 Bosch Rexroth AG Tightening Technology 3 608 878 300 System 350 3 608 878 300 2019 03 ...