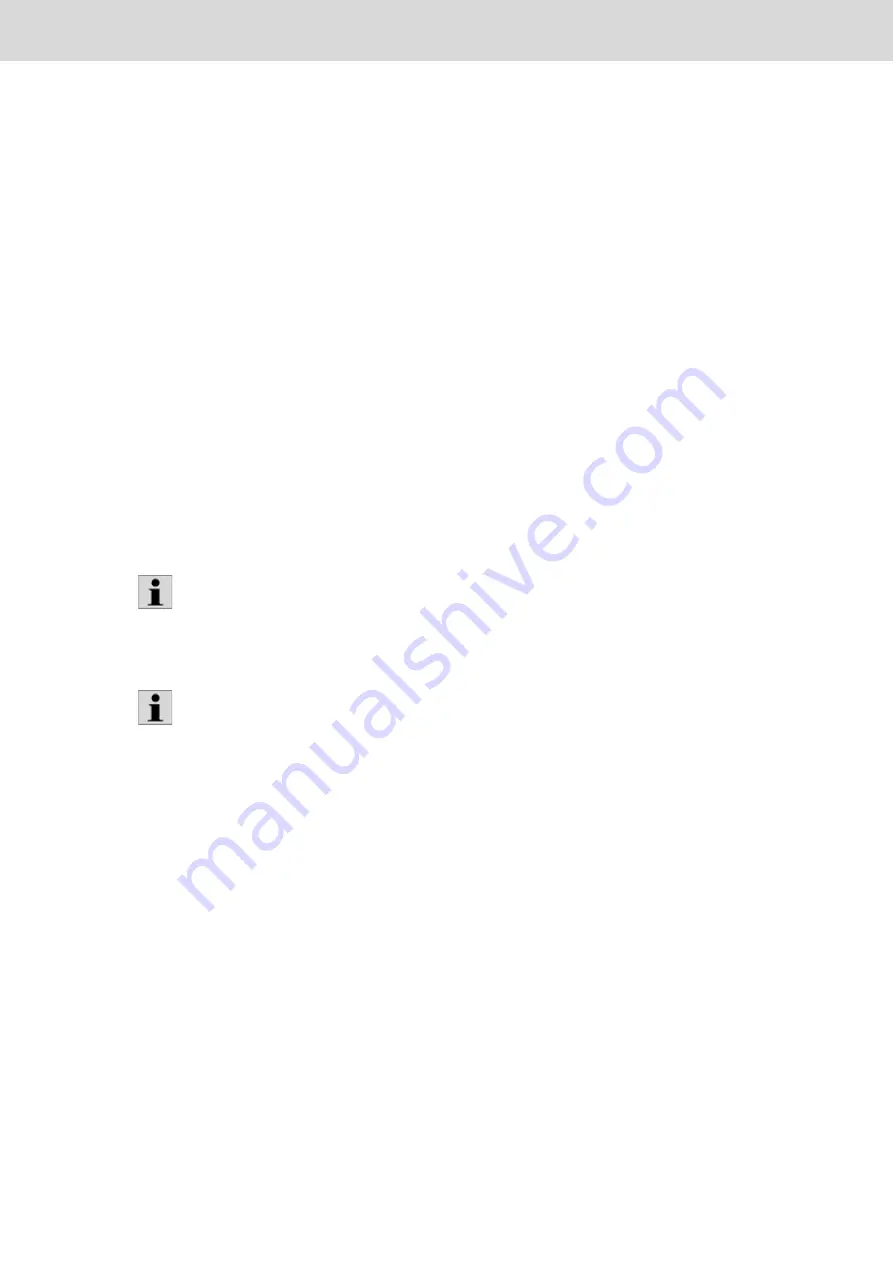
480
Bosch Rexroth AG
| Tightening Technology
3 608 878 300
System 350
| 3 608 878 300/2019-03
6.12.5
Settings for Integra 6 standard PLC interface
For the use with the Daimler Integra 6 standard PLC interface, an IL function block for communication
with the customer system PLC is required. For use of the IL block, the following settings have to be made.
6.12.5.1
ID codes
The ID codes for component/tightening are transferred via the Profinet interface. The ID codes read in via
Profinet are distributed internally on the tightening applications and to provide additional position
information.
The source of the ID codes is defined in the BS350 operating system under
System
Tightening
cell data
ID code
.
Under
Device selection
, select
IL
.
The checkboxes
Delete ID code after start
,
Extend ID code with sequence number
und
Use channel-
specific ID code in application operation
must not be enabled.
Configuration
In the Integra 6 standard, it was defined for the interface between PLC and tightening system that the ID
code has to be transmitted from the PLC to the tightening system in the following format:
<PartsID>_<Position>
The
<PartsID>
corresponds to the 20 characters transmitted by the PLC in bytes 32-51 (see below).
The
<Position>
is generated from the respective position number (
FOx_PosNo
) as two-character ASCII
string. A leading zero is automatically added to the position number < 10 transmitted by the PLC.
Otherwise, the number is converted directly.
To correctly establish assignment between application ID and PLUS configuration, the PLUS
configuration in BS350 of the
ID filter
and the
ID-PosMask
have to be set as follows:
For all QI quality identifiers, the position number (
Pos
) has to be entered with two digits (with leading zero,
"00" if not used).
•
The permissible value range for
FOx_PosNo
is 0…99.
•
The PartsID transmitted by the PLC must always have 20 ASCII characters. If a shorter PartsID is
required, it has to be filled up by a valid (7-bit/US) ASCII character (e.g. space or underscore). Binary
data is not permitted.
Here, it is important that the component series number and the position information match the tightening
system configuration; in this connection, please refer to section
connection in the BS350 operating system
:
ID PosMask
and
ID filter.
The position transmitted by the PLC is compared character after character (ASCII, not as number); in the
preparation of the position number by the PLC, this has to be observed!
Position:
1
2
3
4
5
6
7
8
9
10 11 12 13 14 15 16 17 18 19 20 21 22 23
ID filter:
P
P
P
P
P
P
P
P
P
P
P
P
P
P
P
P
P
P
P
P
P
P
P
ID PosMask:
*
*
*
*
*
*
*
*
*
*
*
*
*
*
*
*
*
*
*
*
*
P
P
Summary of Contents for Rexroth Tightening System 350
Page 4: ...4 641 Bosch Rexroth AG Schraubtechnik System 350 3 608 878 300 2019 03 ...
Page 120: ...120 641 Bosch Rexroth AG Tightening Technology 3 608 878 300 System 350 3 608 878 300 2019 03 ...
Page 194: ...194 641 Bosch Rexroth AG Tightening Technology 3 608 878 300 System 350 3 608 878 300 2019 03 ...
Page 638: ...638 641 Bosch Rexroth AG Tightening Technology 3 608 878 300 System 350 3 608 878 300 2019 03 ...