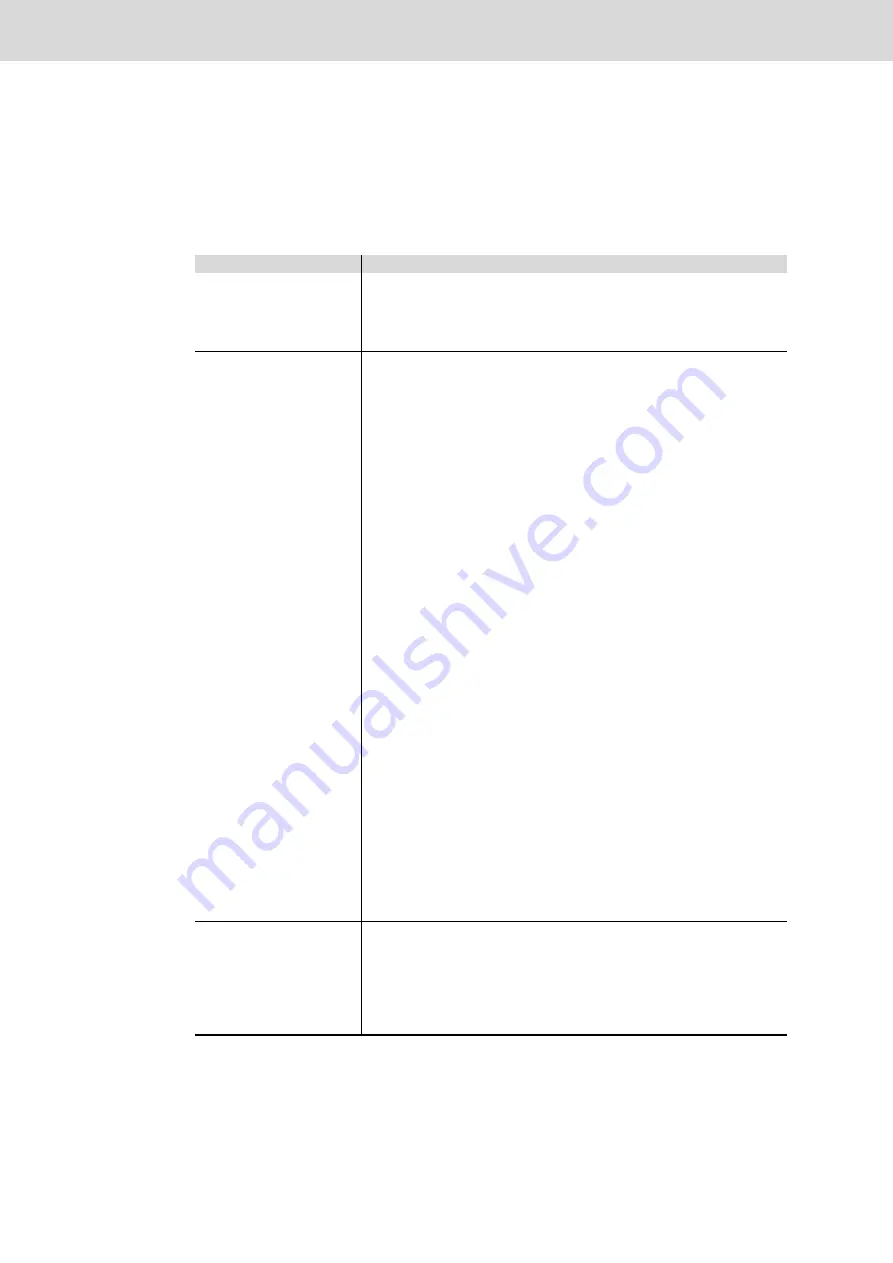
558
Bosch Rexroth AG
| Tightening Technology
3 608 878 300
System 350
| 3 608 878 300/2019-03
Tool
As of version V2.600 of the
Rexroth Tightening System 350
, the
Tool
option is supported. Via
Tool
, you
can configure the maintenance interval for tightening spindle and ErgoSpin and make settings for
ErgoSpin SlimLine/GripLine for a new angle head. Click the
Options
button to start the configuration.
The button is active if a measurement transducer DMC, VMC...-SD/-QC/-SP, 3WMC090 / 4WMC220
or ErgoSpin has been configured. The
ErgoSpin hand-held nutrunner options
/
DMC options
/
VMC
options
/
WMC options
dialog is displayed:
Table 7–15:
ErgoSpin hand-held nutrunner options/ DMC options/ VMC options/ WMC options dialog
Element
Description
Info hand-held nutrunner
(for ErgoSpin) /
Info tightening spindle
(for DMC, VMC...-SD/-QC/-SP
and 3WMC090/ 4WMC220)
–
ID number:
Number to identify the hand-held nutrunner or the tightening spindle.
–
Comment:
For entry of a comment, a max. of 400 characters is available.
–
MCT protocol document ID
: Here, you can save a comment for the MCT
protocol document identification.
Maintenance interval
monitoring
–
Options / settings
: Opens the
Maintenance settings
dialog. In this dialog, at
least one of the following options
Next maintenance after cycles
and/or
Next
maintenance by date
can be selected to define performance of the next
maintenance:
–
Write protection
: The checkbox can only be selected if your are logged in as
system administrator. If the write protection is active, users can only change
the values for the maintenance information.
–
Next maintenance after cycles
:
Fixed with
: User is free to determine after which number of tightening cycles
the maintenance is to be performed.
Load-dependent with
:
The tightening cycles for the maintenance are automatically determined by
the system in a load-dependent manner.
Information
:
Here, you can define the number of tightening cycles before the maintenance
information is to be provided.
Remaining tightening cycles
: Here, the remaining tightening cycles until the
maintenance are displayed.
–
Next maintenance by date
:
Maintenance on
:
Here, the date for the next maintenance is set.
Information, upcoming maintenance
:
Here, it can be defined when information on the upcoming maintenance is to
be provided.
–
Confirm maintenance
: If you want to confirm the maintenance, you have to
activate the
Confirm maintenance
checkbox.
– The settings are accepted by means of
OK
. You can exit the dialog without
changes using
Cancel
. To accept the settings made, the channel
configuration has to be sent to the controller.
– The settings for the maintenance interval will be displayed above the button.
– If in active monitoring/information, the limit set for the next maintenance/
information is reached, the controller will set the
MntTool/InfoTool
PLC output
signal and enter a class 5 system error. The PLC signal is reset if one of the
following events occurs:
– Maintenance is deactivated.
– The maintenance is confirmed and the settings are adjusted accordingly.
Exchanging the angle head
(only for ErgoSpin SlimeLine/
GripLine)
–
new serial number:
Number of the next output drive to be used. By default, the
serial number of the last angle head exchanged is displayed.
–
Number of cycles
: Cycles that have already been run by the angle head to be
used. By default, 0 is entered.
– The settings are accepted by means of
OK
. If no entries have been made, a
warning diagnosis with corresponding information will be shown when you try to
accept the settings.
Summary of Contents for Rexroth Tightening System 350
Page 4: ...4 641 Bosch Rexroth AG Schraubtechnik System 350 3 608 878 300 2019 03 ...
Page 120: ...120 641 Bosch Rexroth AG Tightening Technology 3 608 878 300 System 350 3 608 878 300 2019 03 ...
Page 194: ...194 641 Bosch Rexroth AG Tightening Technology 3 608 878 300 System 350 3 608 878 300 2019 03 ...
Page 638: ...638 641 Bosch Rexroth AG Tightening Technology 3 608 878 300 System 350 3 608 878 300 2019 03 ...