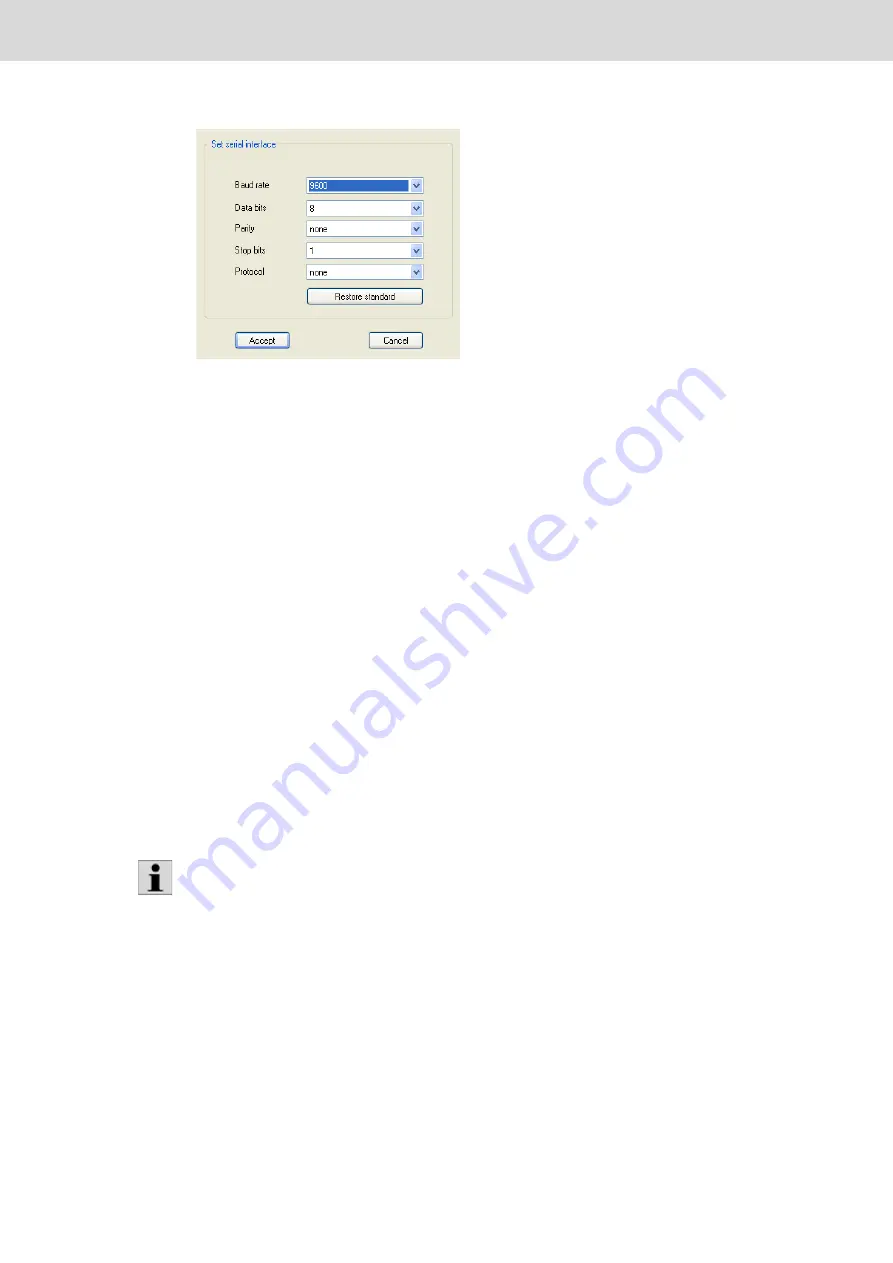
588
Bosch Rexroth AG
| Tightening Technology
3 608 878 300
System 350
| 3 608 878 300/2019-03
Fig. 7–30:
Parameter dialog X3C1
You can make the following settings in the
Set up serial interface
group:
•
Baud rate
(300, 1200, 2400, 4800, 9600, 19200, 38400, 57600, 115200)
The standard value is 115200 Baud. Use this value, if the partner controller allows so. Otherwise,
delays during results output may occur, which limits the availability of the system.
•
Data bits
(7, 8)
•
Parity
(none, odd, even)
•
Stop bits
(0, 1, 2) and
•
Protocol
(none, X-On/X-Off, RTS/CTS).
Click
Accept
to store these data in the program.
7.6.2.3
Setting up additional interfaces
Type A interface
This interface is intended for inserting type A interface modules from Rexroth. A tightening system is
controlled by this interface.
Open the associated parameter dialog by double clicking the parameter field in line A (see Figure
).
In the
Select interface module
field, select the desired module from the drop-down list and set its
parameters.
General parameters for all interfaces
Physical interface
The physical characteristics of the interface depend on the field bus module used. They can only be
partially configured via the operating system.
Number of I points /
Number of O points
This parameter determines how many control signals should be processed via the field bus interface.
Receive data / Send
data
Setting of the remaining data width. These settings depend on the set scope of the I/O points. If the
maximum available bandwidths are exceeded, the settings will be automatically corrected to correspond
to the maximum data width. Make sure that the receipt range for ID codes is also set here.
The allocation of the data buffer is shown in tables in section
Layout of the data buffer for transferring
.
Receive IL data /
Send IL data
Only with KE350G IL and CS351x-IL: Setting of the remaining data width. These settings depend on the
set scope of the I/O points. If the maximum available bandwidths are exceeded, the settings will be
automatically corrected to correspond to the maximum data width.
This setting only reserves the memory space for the logical control signals (1 bit per input or output).
Control signal assignment is implemented using the PLC assignment table.
Summary of Contents for Rexroth Tightening System 350
Page 4: ...4 641 Bosch Rexroth AG Schraubtechnik System 350 3 608 878 300 2019 03 ...
Page 120: ...120 641 Bosch Rexroth AG Tightening Technology 3 608 878 300 System 350 3 608 878 300 2019 03 ...
Page 194: ...194 641 Bosch Rexroth AG Tightening Technology 3 608 878 300 System 350 3 608 878 300 2019 03 ...
Page 638: ...638 641 Bosch Rexroth AG Tightening Technology 3 608 878 300 System 350 3 608 878 300 2019 03 ...