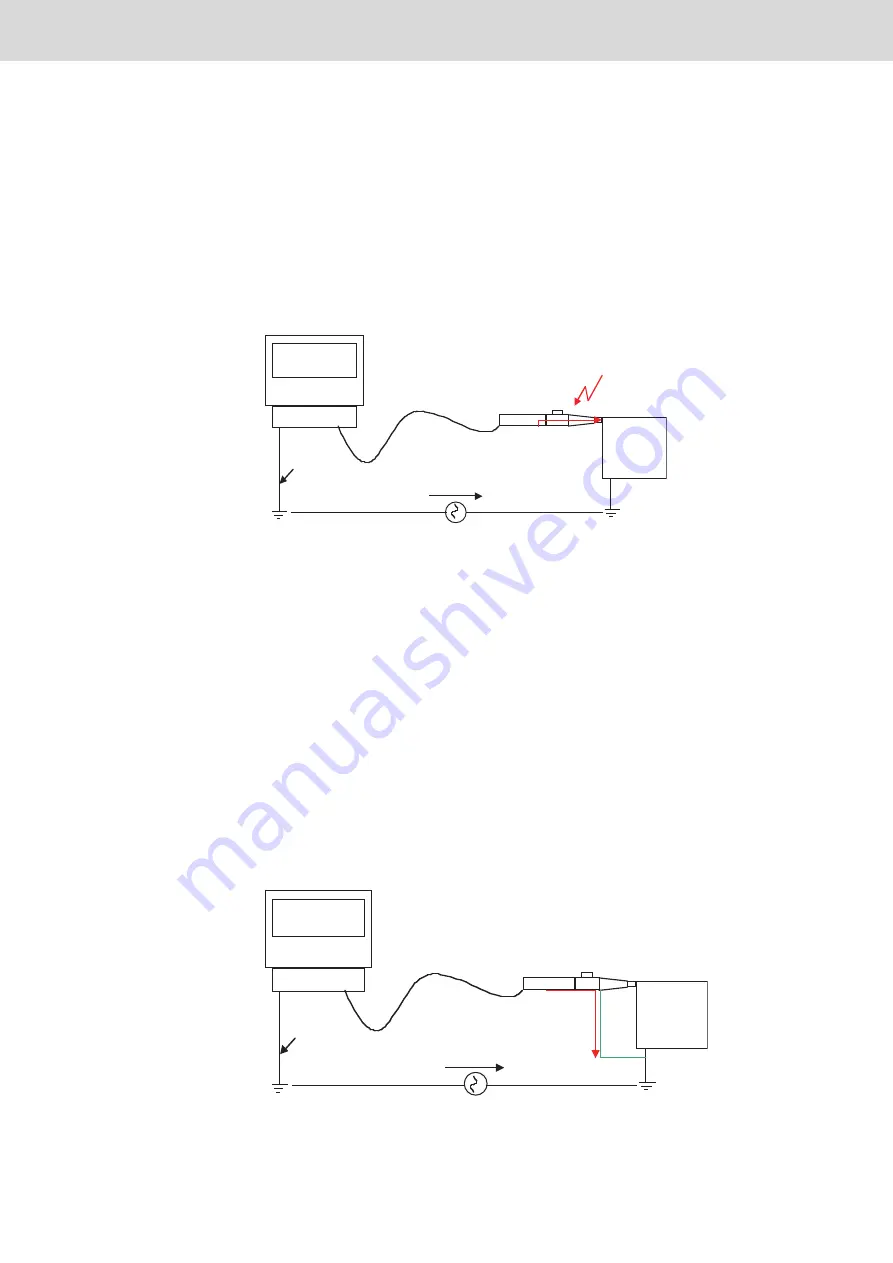
3 608 878 300
Tightening Technology |
Bosch Rexroth AG 101
System 350
| 3 608 878 300/2019-03
Please note here that not only large distances may cause these potential differences, but also other
consumers. In particular, power electronics equipment is suitable for inputting fast, pulsed currents in the
ground wire with switching processes. With such currents, cable leads are an obstacle even over a short
distance and lead to potential shifts. The same applies to workpieces on roller conveyors or other
transport equipment where the grounding of the workpiece is not ensured in a defined manner.
If such differences in voltages occur between the workpiece and tightening spindle, the potential will be
equalized via the output drive shaft when the nutrunner is placed on the workpiece. As the current has to
find a path via the output drive shaft bearing and the monitoring units, this may also influence the
transducer.
The extremely sensitive monitoring electronics for torque detection may in some cases be influenced by
this current. This influence can only be avoided if no leakage currents flow over the spindle output drive.
Fig. 4–28:
Parasitic current
The disrupting potential differences cannot be completely avoided, as the electric equipment and
installation is implemented according to the various customers’ demands. Here, an optimum grounding
(even in the high frequency range) cannot always be taken into account.
A potential equalization between the tightening spindles and workpiece would be a recommended
solution for the tightening system. A gn-ye cable with a 10 mm
2
gn-ge cross-section is recommended. A
braided copper cable that conducts any resulting workpiece stray currents over the spindle housing to
the cable shield is ideal.
In general, the distance of the connection between the workpiece and spindle should be kept to a
minimum.
Fig. 4–29:
Additional potential equalization
(1) 10 mm
2
gn-ge
(2) Connection cable for ErgoSpin/tightening spindle
(3) ErgoSpin / spindle
(4) I
STR
(5) Workpiece
(6) U
STR
(6)
(4)
(1)
(2)
(3)
(5)
(7)
(4)
(3)
(6)
(1)
(2)
(5)
Summary of Contents for Rexroth Tightening System 350
Page 4: ...4 641 Bosch Rexroth AG Schraubtechnik System 350 3 608 878 300 2019 03 ...
Page 120: ...120 641 Bosch Rexroth AG Tightening Technology 3 608 878 300 System 350 3 608 878 300 2019 03 ...
Page 194: ...194 641 Bosch Rexroth AG Tightening Technology 3 608 878 300 System 350 3 608 878 300 2019 03 ...
Page 638: ...638 641 Bosch Rexroth AG Tightening Technology 3 608 878 300 System 350 3 608 878 300 2019 03 ...