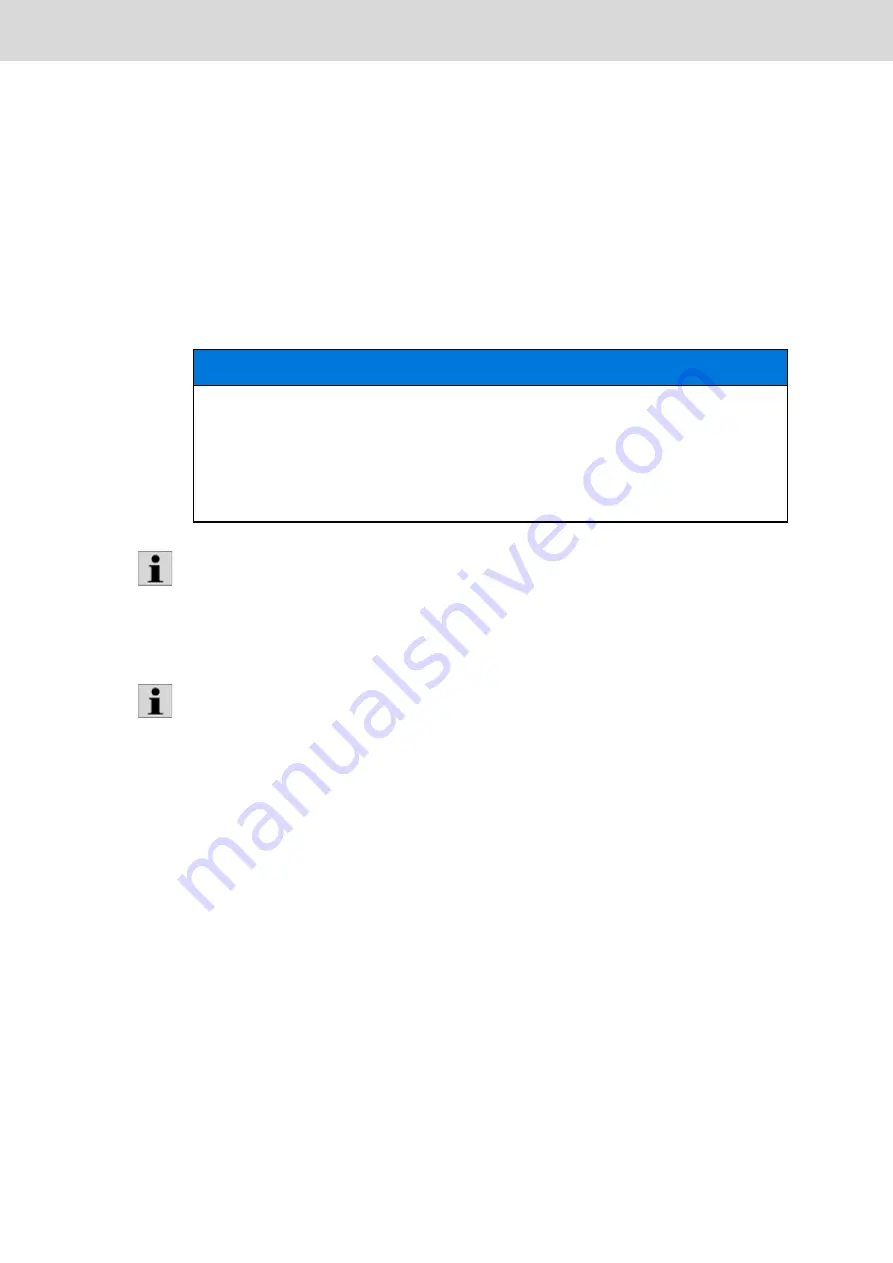
626
Bosch Rexroth AG
| Tightening Technology
3 608 878 300
System 350
| 3 608 878 300/2019-03
7.8
Special operating features of the hand-held nutrunner
ErgoSpin/CC-ErgoSpin
This section describes commissioning and the special features for operating an ErgoSpin hand-held
nutrunner.
7.8.1
Special features of ErgoSpin with open flat output drive with mechanical safety catch
In order to ensure perfect current feed of the motor, the motor of the ErgoSpin hand-held nutrunner is
adjusted after every switch-on of the
Rexroth Tightening System
. The alignment process takes one motor
rotation. This corresponds to an angle of turn at the output drive of 8° to 15°.
7.8.2
Special features of ErgoSpin with open flat output drive without safety catch
This section describes special features for the configuration of ErgoSpin VarioLine with open flat output
drive without safety catch. Flat output drives without safety catch are applied if bolts are also to be
loosened. For example, for fitting brake lines.
For flat output drives without safety catch, the controller must ensure precise running in open position by
means of internal angle measurement. The operating sequences are to be stored and executed by the
tightening controller.
On "opening" the flat output drive, the nutrunner automatically runs to open position of the flat output drive
from every position. The flat output drive is "opened" in tightening direction (clockwise). Before opening,
the flat output drive has to be removed from the tightening position. If the user is still at the tightening
position when "opening", undesired loosening of tightening is prevented by opening in tightening
position.
The tightening/loosening sequence (Prgx/Prg99) and opening of the flat output drive ("opening"
program) is realized alternatively by operating the start button at the hand-held nutrunner.
For referencing the open position, teaching of the tightening system is required. This is required after
switching on the system or if the position is insufficient due to accumulated inaccuracies.
The open position is referenced in tightening direction in the teach-in process.
To recognize potential manipulation at the flat output drive outside of a tightening operation, the position
of the flat output drive (angle measurement) is continuously measured by the tightening system.
NOTICE
Damage to the flat output drive
When open flat output drives with mechanical safety catch are in zero position, i. e. when they are
open, they can only be moved in output drive spin direction. If the output drive direction of an open flat
output drive with mechanical safety catch does not comply with the alignment spin direction of the
hand-held nutrunner, the flat output drive may be damaged.
Always use the latest firmware (for version V2.400 as of version 1V08) of the servo amplifier
(LTU350/1 or CS351) that is adjusted to the flat output drive.
In the
Rexroth Tightening System 350
the alignment spin direction is directly adjusted by specifying the
output drive spin direction and the reverse spin direction, see
Channel configuration of open flat output
.
This application is supported as of BS350 V2.400.
For application, the special firmware
esfw-22B2.mhx
for ErgoSpin is required.
Summary of Contents for Rexroth Tightening System 350
Page 4: ...4 641 Bosch Rexroth AG Schraubtechnik System 350 3 608 878 300 2019 03 ...
Page 120: ...120 641 Bosch Rexroth AG Tightening Technology 3 608 878 300 System 350 3 608 878 300 2019 03 ...
Page 194: ...194 641 Bosch Rexroth AG Tightening Technology 3 608 878 300 System 350 3 608 878 300 2019 03 ...
Page 638: ...638 641 Bosch Rexroth AG Tightening Technology 3 608 878 300 System 350 3 608 878 300 2019 03 ...