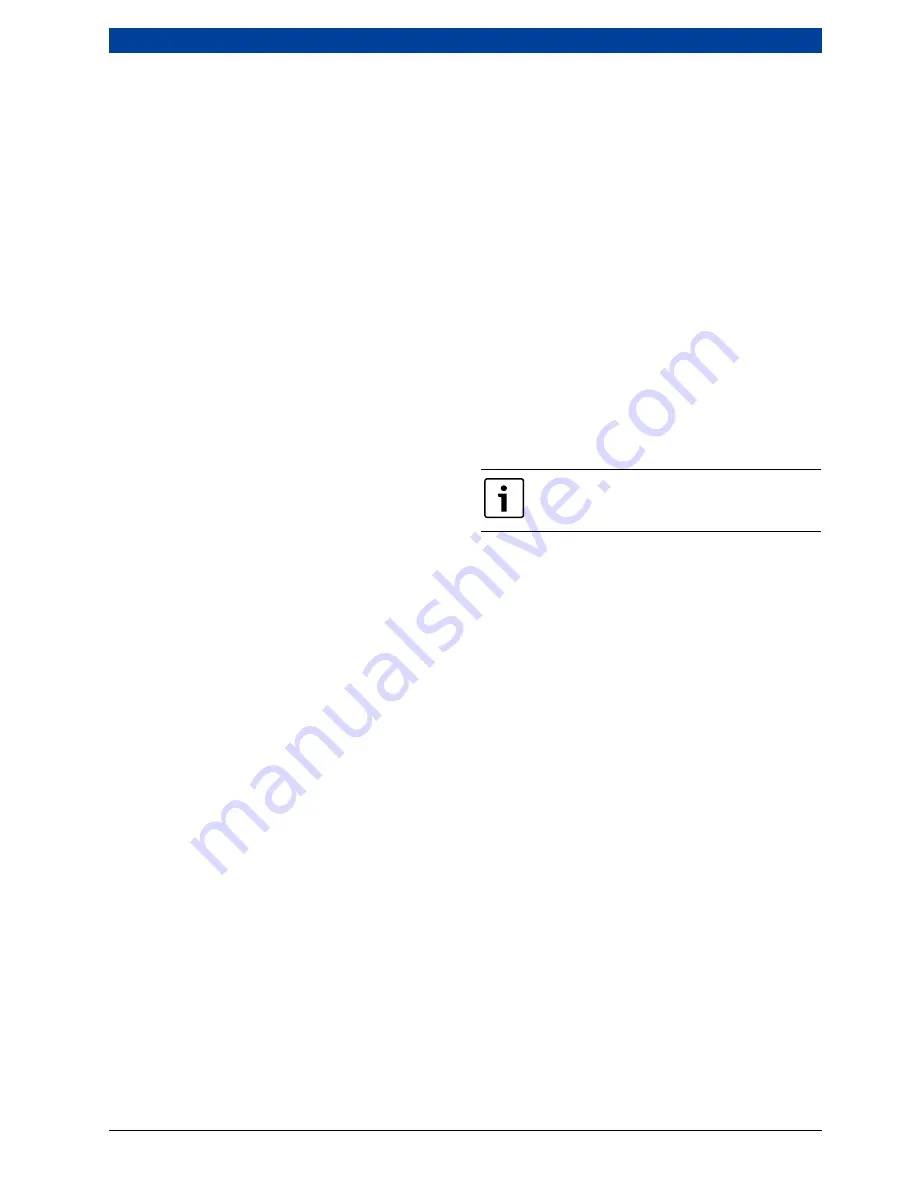
Regulations and operating conditions
|
39
6 720 807 794 (2013/04)
UNIMAT
Always observe the following:
• The max. rated output of the boiler is reduced when
antifreeze is used (individual design).
• Use tested types of antifreeze that are approved for
use in hot water systems.
• Antifreeze must contain corrosion inhibitors so that
the addition of antifreeze does not increase the
system's susceptibility to corrosion.
• Ratio of antifreeze to water: maximum 50 %
• Use desalinated water with a conductivity of < 10 μS/
cm as fill and top-up water.
• Do not use additional dosing agents. Prevent
corrosion from occurring as a result of reactions
between these additional agents and the antifreeze.
• In the first year of operation, perform a quarterly
inspection on the water side of the boiler. In the event
of a positive result, the inspection periods can be
increased to the legal limits.
5.3.4
Corrosion protection if system out of use for
long periods
Airborne oxygen that enters the system causes corrosion
in a cooled and depressurised boiler. Suitable
preventive measures should therefore be taken. Suitable
protective measures should be taken whenever a boiler
has been idle for longer than three days. Bosch
recommends the following options:
1. Preservation on the water side through pressure
maintenance (any time period)
If one or more boilers in a boiler system are shut down
and it is ensured that one boiler or at least the pressure
maintaining system remains operational, no further
preservation measures on the water side are required.
Ensure that the boiler remains connected to the mains
via the open flow shut-off device so that the gas supply
pressure builds up. This prevents oxygen entering the
boiler as a result of positive pressure.
As an alternative, the return shut-off device can also be
opened. However, do not have both shut-off devices
open at the same time as this can result in heat losses
due to unwanted circulation.
2. Wet preservation on the water side for shutdowns of
up to 3 months
The boiler is completely filled with water, an excess of
oxygen binders is added and the boiler water capacity is
circulated at defined intervals. For more information on
wet preservation, please see the operating instructions
“G012 Wet and dry preservation”.
Carrying out preservation
Regular circulation is necessary to ensure the metered
additive is evenly mixed with the boiler water. For this,
install a pump that is connected to the outlet connection
downstream of the outlet shut-off valve via a tee on the
inlet side, and to the return between the boiler and
return shut-off device on the pressure side. The additive
can be topped up via the dosing station on the pressure
side of the pump. After this, tightly seal all boiler valves
to prevent the ingress of airborne oxygen during the idle
time. To ensure the preservative solution is thoroughly
mixed in, the water must be circulated 5 times every 3
days using the pump.
For more information, please see the operating
instructions “G012 Wet and dry preservation”.
3. Dry preservation on the water side for shutdowns of
longer than 3 months
The system is fully drained, filled with a special drying
agent, and then resealed. Compared to wet
preservation, it takes around 1-2 days to prepare the
system for operation. We recommend involving a Bosch
service engineer.
For precise information on carrying out dry preservation,
please see the operating instructions “G012 Wet and dry
preservation”.
5.3.5
Guidelines for water quality
Chemical additives in the heating water
If plastic pipes that are permeable to oxygen are
installed in an underfloor heating system, the corrosion
process can be prevented by adding chemical additives
to the heating water. In this case, request certification
from the manufacturer of the chemical additives as to
the effectiveness and harmlessness to other system
components and materials in the heating system.
Water treatment
Boiler operators must take account of the fact that there
is no such thing as pure water as a heat transfer medium.
For this reason, particular attention should be paid to
the water quality. Constant monitoring of the water
quality is an important factor in achieving economical
and trouble-free operation of the heating system. Water
treatment also makes a contribution to energy savings
and to preserving the value of the entire system. It is an
essential factor for increasing the economic viability,
functional reliability, service life and, last but not least,
the maintenance of the constant operational availability
of the heating system.
Prevention of damage through limescale formation
Scaling means that stubborn calcium carbonate
deposits occur in the boiler. These deposits can cause
local overheating and a limited formation of cracks in the
boiler. The impaired heat transfer caused by scaling can
lead to a significant drop in boiler output and to an
increase in flue gas loss. Boiling noises may also occur
under certain circumstances.
Minimum requirements of water analyses for designing a
water treatment system
page 41.
Chemical additives that are not certified as
harmless by the manufacturer must not be
used.