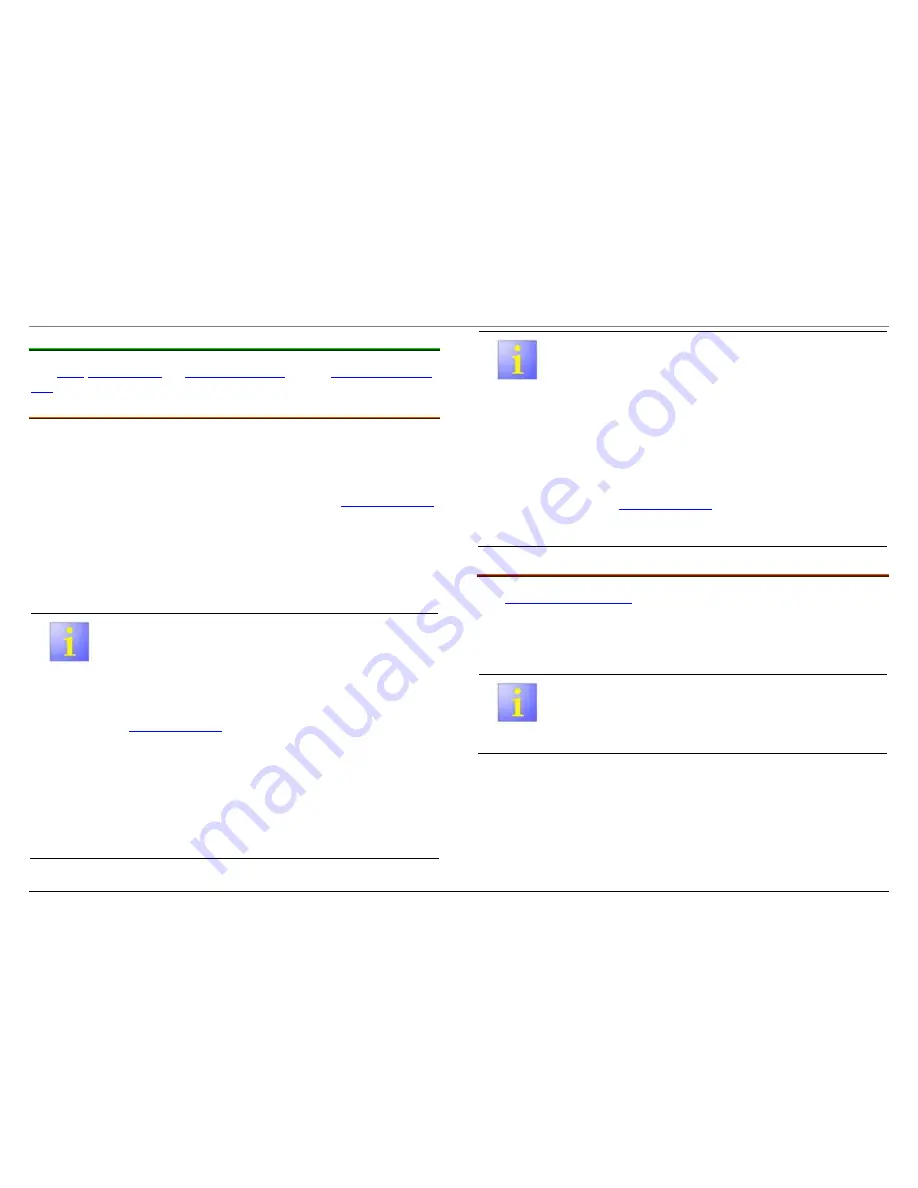
3.6.2
NTC air temperature
The
NTC
dryer heater
(1),
condenser outlet
(2) and
washing machine
tub
(5) control the temperatures for the drying programmes.
3.6.2.1 NTC washing machine tub (5)
The NTCs at the condenser inlet and outlet are used to obtain a better
drying result. If one of the two NTCs fails, the customer does not
receive an error on the display. The appliance continues functioning
“normally” even if the drying time is a little longer.
The NTC washing machine tub (NTCD1) controls the
warm spin cycle
and the switching on of the condensation water valve:
►
Warm spin cycle:
Start at 54 °C
►
Cottons/Coloureds: 77.5
°C
►
Easy care:
65 °C
NTCD1 defective.
The NTC water heater (4) is used instead of
NTCD1 (5) for monitoring the temperature difference
in the condenser. On account of its lower precision
the safety temperature is reduced from 68 °C to
50 °C. The drying programme is executed without
warm spin cycle
!
►
Temperature NTC water heater > 50 °C:
If the user stops the drying programme and
selects “Drain/Spin” or “Drain”, a cool down is run
before the drain cycle until the air temperature
NTC < 45 °C is reached.
If NTC < 45 °C is not reached within 10’, only the
drain cycle is run.
Air temperature NTCD1 > 68 °C (N0)
►
If the user stops the drying programme and
selects “Drain/Spin” or “Drain”, a cool down is run
before the drain cycle until the air temperature
NTCD1 < 60 °C (max. filling time 10') is reached.
If NTCD1 < 60 °C is not reached within 10’, only
the drain cycle is run.
►
If the user stops the drying programme and
immediately starts a new drying programme,
the
warm spin cycle
is not run. Otherwise the
programme will run normally.
(does not apply to programme reset)
3.6.2.2 NTC condenser outlet (2)
The
NTC condenser outlet
switches the condensation valve off:
►
Cottons/Coloureds: 74
°C
►
Easy care:
62 °C
NTCD2 defective.
►
The condensation valve is activated after 20 min.
from the start of the drying cycle and remains on
until the cycle ends.
815_58300000146136_ara_en_b.doc – 12.04.10
Seite 13 von 32