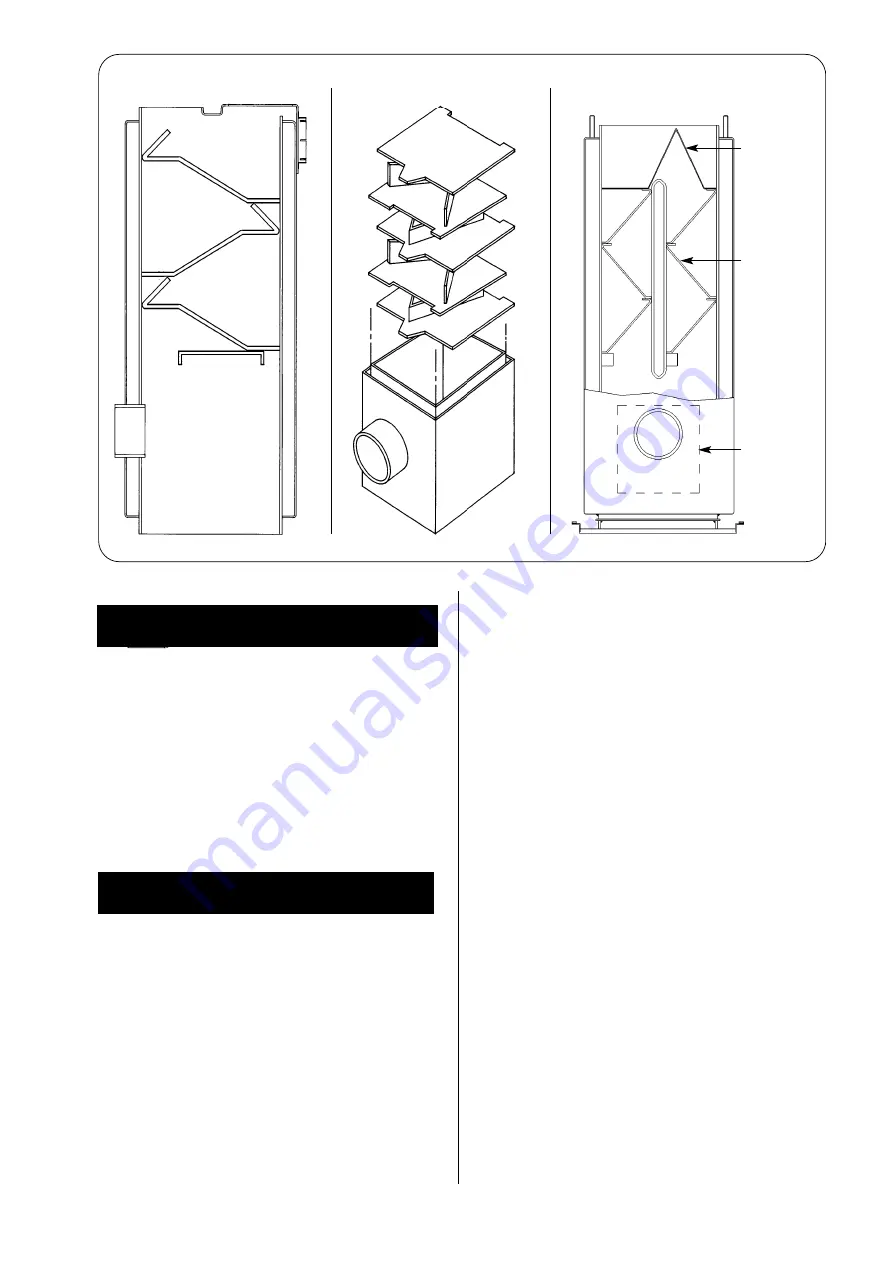
13.1
Hand the users instructions and Benchmark book-
let to the user or purchaser for retention and instruct them in
the efficient and safe operation of the appliance and the heat-
ing/hot water system.
13.2
Advise the user or purchaser of the precautions necessary
to prevent damage to the heating/hot water system and to the
building in the event of the heating system remaining
inoperative during frost conditions.
13.3
Finally advise the user or purchaser that for continued efficient
and safe operation of the appliance it is important that adequate
servicing is carried out by a qualified engineer at least once per year.
Worcester Heat Systems Limited will be pleased to discuss and
offer a comprehensive maintenance contract.
13.4
Set the system controls to the users requirements.
14.1
The following should be carried out at least once per year
to ensure efficient, trouble free operation.
1.
Carry out a pre-service check noting any operational faults.
2.
Check and clean the burner.
3.
On the CF model check and clean the air intake grille located
in the boiler room.
4.
On the RS balanced flue model check and clean the air intake
ducts at the rear and underneath the boiler and the air intake
grille at the end of the terminal.
5.
Check and clean the baffle retainer (20-25 model only).
6.
Check and clean the baffles.
7.
Check and clean the heat exchanger surface.
8.
Check the heat shield (on 20-25 model only).
9.
Check the combustion chamber insulation board.
10.
Check that the flue system is unobstructed and clean as
necessary.
11.
If the appliance has been installed in a compartment check
that the ventilation areas are clear.
12.
Clean all oil filters.
Some of the servicing points are covered more fully in the
following instructions:-
14.2 Pre-Service Check
1.
Remove the cabinet front and top panels as described in
Section 5.
2. On the RS balanced flue model remove the burner cover box
as described in Section 5.5.
3.
Operate the appliance and system, noting any faults which
may need to be corrected during the service.
14.3 Cleaning the Burner
IMPORTANT
– Disconnect the electrical supply at the mains before
commencing any servicing. Turn off the oil at the service cock.
1.
Remove the burner.
(a)
Isolate the oil supply at both the oil tank and the isolating valve
situated above the burner on the right-hand side. (See Figs. 2 and 3).
(b)
On the RS balanced flue model remove the burner box cover
by pulling forwards to release the ball studs. This will be found
easier by pulling on one side of the handle first to release two of
the ball studs and then repeating on the other side. Take care
not to pivot the remaining two ball studs too far around as this
will cause damage to the spring clips.
(c)
Disconnect the electrical lead from the control box by depress-
ing the two locking ears on the plug and pulling downwards.
(d)
On the RS balanced flue model feed the electrical lead back
through the grommet seal to give sufficient play to allow with-
drawal and inspection of the burner.
(e)
Slacken the two M6 burner locking screws, using a 5mm
allen key, and remove the burner.
2.
Clean the fan impeller using the following procedure:
Electro-oil Inter B9 Burner
(a)
Remove the two screws holding the combustion head in
position and withdraw the combustion head and air guide collar
(where fitted).
(b)
Remove the three remaining screws holding the front cover
plate in position and withdraw the cover to expose the fan impeller.
14. Routine Cleaning and Inspection
13. Instructions to the User
23
Fig. 23.
Location of Boiler Flueway Baffles.
(a) 12-14
(b) 15-19
(c) 20-25
ENSURE THAT ALL BAFFLES ARE FIRMLY SEATED IN POSITION
Baffle
retainer
Baffle
Heat shield
All manuals and user guides at all-guides.com