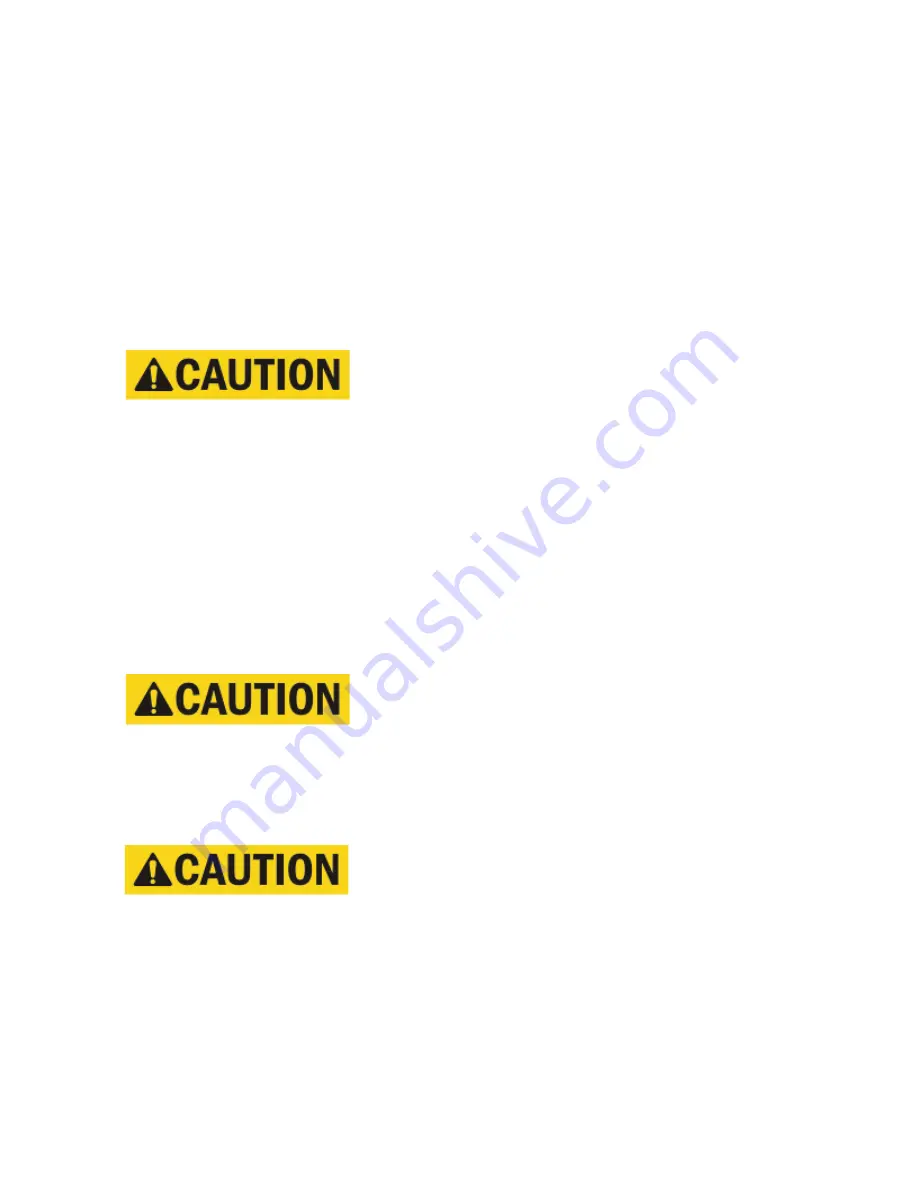
29
309416
01/31/2012
Maintenance
V. Prior to cleaning an element, check the element for damage. Damaged air filter elements must be
replaced.
A. Place a bright light inside the element to inspect for damages or leaks.
B. Inspect all seals and seal contact surfaces on the housing. Should faulty seals be evident, correct
the condition immediately.
VI. If element is undamaged, clean the air filter element.
A. The maximum number of times that an element should be cleaned is twice; however, the element
should be used no longer than a period of 1 year without changing.
C. If the cleaned element is to be stored for later use, it must be stored in a clean container.
VII. Install the air filter element.
VIII. Install the rear cover and tighten clamp.
IX.
Reset the air filter restriction indicator and the machine will be ready for operation.
B. When cleaning the element with compressed air, never let the air pressure exceed 30 PSI.
Reverse flush the element by directing the compressed air up and down the pleats in the filter
media from the inside of the element. Continue reverse flushing until all dust is removed. Should
any oil or greasy dirt remain on the filter surface, the element should be replaced.
Do not strike the element against any hard surfaces for clean-
ing as it may possibly rupture the element. Do not oil element.
When cleaning an element, the element will be damaged if you
exceed the recommended maximum air pressure of 30 PSI.
I.
Loosen the clamps that secure the engine air filter’s rear cover to the filter housing.
II. Remove and clean the rear cover.
III. Remove the air filter element.
IV. Clean the canister with a damp cloth inside and out. DO NOT blow dirt out with compressed air.
Never blow dirt out of the interior of the filter housing. This
may introduce dust downstream of the filter. Instead, use a
clean damp cloth.
8.7 Engine Air Filter Replacement