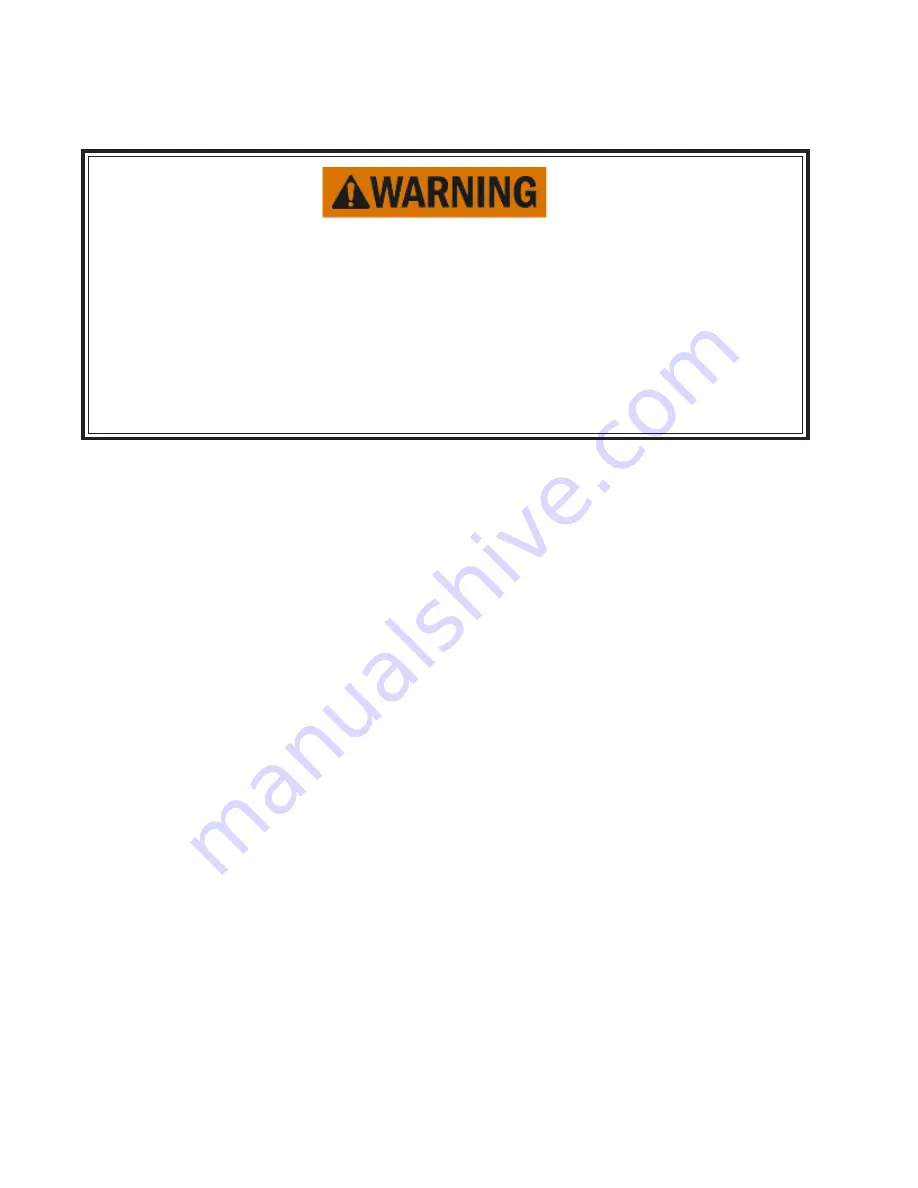
14
309150
This inspection should be done prior the compressor test.
I.
Check all assemblies, clamps, fittings, hose connections, nuts, and bolts to ensure they are properly
tied and secured to the vehicle. This is a very critical area of inspection. The vehicle should not be
moved until this inspection has been completed.
II.
Remove all tools, rags, and installation equipment from the area.
III.
Check compressor oil level and hydraulic fluid level. Check all valves to ensure they are in correct
operating position.
IV.
Apply decals to proper location. Make sure that the area is cleaned prior to applying decals. All
decals should have a professional appearance upon application.
V.
Vacuum all areas that have metal or plastic shavings. Wipe all fingerprints off unit and vehicle.
Installation & Operation
5. Pre-Start-up Inspection Checks
A compressor service valve should be located at the hose reel inlet or the customer’s air connection
port when a hose reel is not used. Typical plumbing from the machine’s air outlet port occurs in the
following order:
1. Air tank
2. OSHA valve.
3. Service valve.
4. Moisture trap/gauge/oiler combination (when used).
5. Hose reel (when used).
Summary of Contents for 36 BHP PISTON
Page 2: ...2 309150 ...
Page 28: ...28 309150 ...
Page 29: ...29 309150 WARRANTY SECTION ...
Page 34: ...34 309150 ...
Page 35: ...35 309150 PARTS AND ILLUSTRATION SECTION ...
Page 37: ...37 309150 16 15 13 14 10 1 2 5 11 12 8 6 7 9 4 3 Frame System ...
Page 43: ...43 309150 13 6 5 3 7 1 4 4 2 10 11 12 9 8 16 14 15 16 Cooler System ...
Page 45: ...45 309150 3 1 10 7 2 4 6 5 13 12 11 9 8 Hydraulic Drive System ...
Page 47: ...47 309150 2 3 4 6 5 1 7 Discharge System ...
Page 49: ...49 309150 Canopy System 11 13 4 6 7 1 12 2 2 8 3 4 10 9 5 ...
Page 51: ...51 309150 2J 2B 2C 2D 2J 2H 2E 1 2I 2G 2A 2F Decal System ...
Page 52: ...52 309150 System Schematic ...