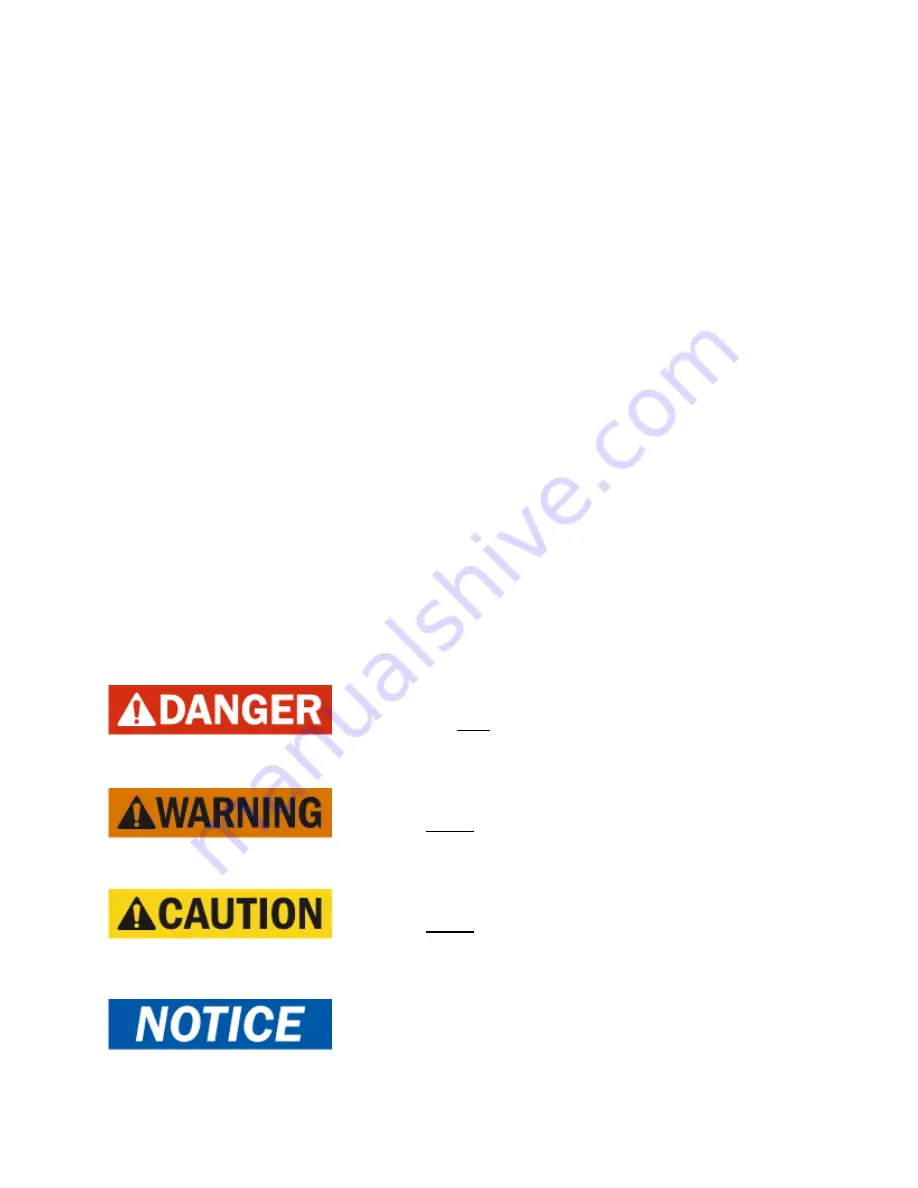
7
309395
IMPORTANT READ BEFORE OPERATING EQUIPMENT
Remember, safety is basically common sense. While there are standard safety rules, each situation has its
own peculiarities that cannot always be covered by rules. Therefore with your experience and common
sense, you are in a position to ensure your and others safety. Lack of attention to safety can result in:
accidents, personal injury, reduction in efficiency and worst of all – Loss of Life. Watch for safety hazards
and correct them promptly.
Understanding the proper operation of this equipment is critical to its safe operation. The owner, lessor or
operator of this equipment is hereby notified and forewarned that any failure to observe the safety and
operating guidelines may result in injury and/or damage. Boss expressly disclaims responsibility or liability
for any injury or damage caused by failure to observe these specified precautions or by failure to exercise
the ordinary caution and due care required while operating or handling this equipment, even though not
expressly specified.
In addition to following these safety guidelines, the operator should follow any company specific guidelines
and procedures. Consult your immediate supervisor for specific company safety guidelines and/or proce-
dures.
The following safety symbols are used throughout the manual to draw attention to important information. If
the information is not carefully read and the instructions are not followed, severe injury, death, and/or
damage to property and equipment may occur.
Indicate[s] an imminently hazardous situation, which, if
not avoided,
will
result in death or serious injury.
Indicate[s] a potentially hazardous situation, which, if not
avoided,
could
result in death or serious injury.
Indicate[s] a potentially hazardous situation, which, if not
avoided,
could
result in minor or moderate injury.
Indicate[s] a potentially unsafe situation or practice,
which, if not avoided can result in property and/or
equipment damage only.
Safety
Summary of Contents for BA435 PISTON
Page 2: ...2 309395 ...
Page 24: ...24 309395 ...
Page 25: ...25 309395 WARRANTY SECTION ...
Page 30: ...30 309395 ...
Page 31: ...31 309395 PARTS AND ILLUSTRATION SECTION ...
Page 33: ...33 309395 Frame System 15 2 16 8 10 11 16 6 14 6 9 4 5 6 3 7 1 3 13 12 ...
Page 39: ...39 309395 Air Inlet System 12 8 7 1 11 10 4 15 10 11 13 14 2 5 3 9 6 ...
Page 43: ...43 309395 Canopy System 7 2 6 3 3 5 4 6 7 2 1 ...
Page 45: ...45 309395 Oil Drain System 3 4 1 2 5 ...
Page 47: ...47 309395 Mounting System 1 2 3 ...
Page 49: ...49 309395 Decal System 1 11 1 10 2 1 1 1 11 1 3 1 4 1 5 1 6 1 7 1 2 1 1 1 9 1 8 ...
Page 50: ...50 309395 System Schematic ...