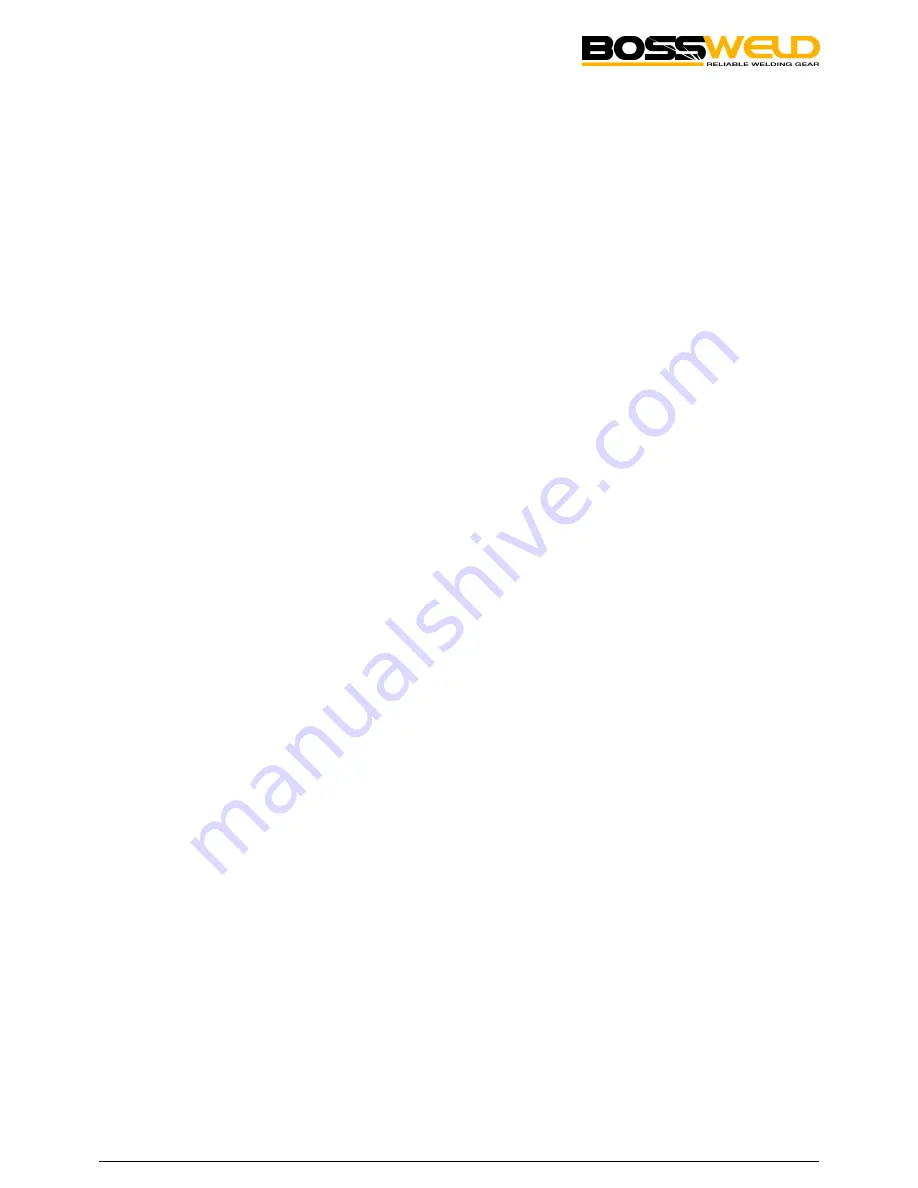
STATEMENT OF WARRANTY
LIMITED WARRANTY:
“Dynaweld” warrants to customers of its authorised distributors hereafter “Dynaweld” that
its products will be free of defects in workmanship or material. Should any failure to conform to this warranty
appear within the time period applicable to the Dynaweld products as stated below, Dynaweld shall, upon
notification thereof and substantiation that the product has been stored, installed, operated, and maintained in
accordance with Dynaweld’s specifications, instructions, recommendations and recognized standard industry
practice, and not subject to misuse, repair, neglect, alteration, or accident, correct such defects by suitable repair or
replacement, at Dynaweld‘s sole option, of any components or parts of the product determined by Dynaweld to be
defective.
THE DYNAWELD COMPANY MAKES NO OTHER WARRANTY, EXPRESS OR IMPLIED. THIS WARRANTY IS
EXCLUSIVE AND IN LIEU OF ALL OTHERS, INCLUDING, BUT NOT LIMITED TO ANY WARRANTY OF
MERCHANTABILITY OR FITNESS FOR ANY PARTICULAR PURPOSE.
LIMITATION OF LIABILITY:
Dynaweld shall not under any circumstances be liable for special, indirect or
consequential damages, such as, but not limited to, lost profits and business interruption. The remedies of the
Purchaser set forth herein are exclusive and the liability of Dynaweld with respect to any contract, or anything done
in connection therewith such as the performance or breach thereof, or from the manufacture, sale, delivery, resale,
or use of any goods covered by or furnished by Dynaweld whether arising out of contract, negligence, strict tort, or
under any warranty, or otherwise, shall not, except as expressly provided herein, exceed the price of the goods
upon which such liability is based. No employee, agent, or representative of Dynaweld is authorized to change this
warranty in any way or grant any other warranty.
PURCHASER’S RIGHTS UNDER THIS WARRANTY ARE VOID IF REPLACEMENT PARTS OR ACCESSORIES
ARE USED WHICH IN DYNAWELD’S SOLE JUDGEMENT MAY IMPAIR THE SAFETY OR PERFORMANCE OF
ANY DYNAWELD PRODUCT. PURCHASER’S RIGHTS UNDER THIS WARRANTY ARE VOID IF THE
PRODUCT IS SOLD TO PURCHASER BY NON-AUTHORIZED PERSONS.
WARRANTY PERIODS
The warranty is effective for the time stated below beginning on the date that the authorized distributor delivers the
products to the Purchaser. Notwithstanding the foregoing, in no event shall the warranty period extend more than
the time stated plus one year from the date Dynaweld delivered the product to the authorized distributor.
2
YEAR
2
YEAR
2
YEAR
2
YEAR
POWER SUPPLIES & WIRE FEEDERS
MAIN POWER MAGNETICS (STATIC
& ROTATING)
ORIGINAL MAIN POWER RECTIFIER
POWER SWITCHING SEMI-CONDUCTORS & CONTROL PC BOARD
ALL OTHER CIRCUITS AND COMPONENTS INCLUDING
2
YEAR
BUT NOT LIMITED TO, CONTACTORS, RELAYS, SOLENOIDS, PUMPS, SWITCHES, MOTORS
Warranty repairs or replacement claims under this limited warranty must be submitted to Dynaweld by an
authorised Dynaweld repair facility within thirty (30) days of purchaser’s notice of any Warranty Claim. No
transportation costs of any kind will be paid under this warranty. Transportation charges to send products to an
authorised warranty repair facility shall be the responsibility of the Purchaser. All returned goods shall be at the
Purchaser’s risk and expense. This warranty supersedes all previous Dynaweld warranties.