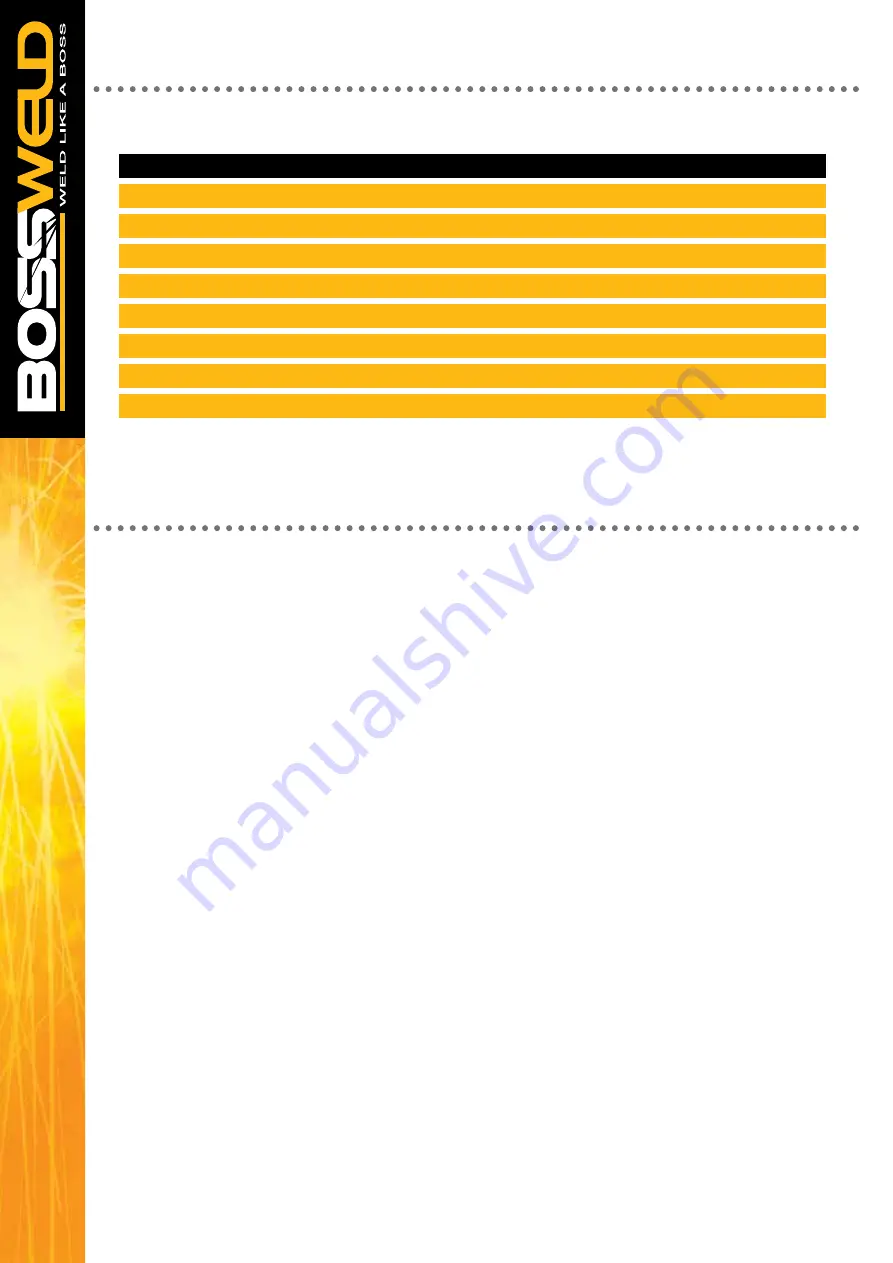
30
Welding current
Welding Volt
Wave control Wire Speed
(Wire Size)
0.6mm
0.8mm
1.0mm
40A
13~15V
1-2
2--3
60A
14~16V
2-4
3--5
2--3
80A
15~17V
3-5
6--8
3--5
2--3
100A
16~19V
3-5
8--10
3--6
3-5
120A
17~20V
4-6
4--7
3--5
140A
19~21V
5-10
5--8
3--5
160A
20~22V
5-10
6--9
4--7
180A
21~23V
5-10
6--9
GMAW (MIG) WELDING
Metal inert gas (MIG) welding is an attractive alternative to MMA (stick welding), offering high deposition
rates and high productivity.
PROCESS CHARACTERISTICS
MIG welding is a versatile technique suitable for both thin sheet and thick section components. An arc is
struck between the end of a wire electrode and the workpiece, melting both of them to form a weld pool.
The wire serves as both heat source (via the arc at the wire tip) and filler metal for the joint. The wire is fed
through a copper contact tube (contact tip) which conducts welding current into the wire. The weld pool is
protected from the surrounding atmosphere by a shielding gas fed through a nozzle surrounding the wire.
Shielding gas selection depends on the material being welded and the application. The wire is fed from a
reel by a motor drive, and the welder moves the welding torch along the joint line. Wires may be solid (simple
drawn wires), or cored (composites formed from a metal sheath with a powdered flux or metal filling).
Consumables are generally competitively priced compared with those for other processes. The process
offers high productivity, as the wire is continuously fed.
Manual MIG welding is often referred as a semi-automatic process, as the wire feed rate and arc length are
controlled by the power source, but the travel speed and wire position are under manual control. The process
can also be mechanised when all the process parameters are not directly controlled by a welder, but might
still require manual adjustment during welding. When no manual intervention is needed during welding, the
process can be referred to as automatic. The process usually operates with the wire positively charged and
connected to a power source delivering a constant voltage. Selection of wire diameter (usually between 0.6
and 1.6mm) and wire feed speed determine the welding current, as the burn-off rate of the wire will form an
equilibrium with the feed speed.
MIG WELDING SETTING GUIDES