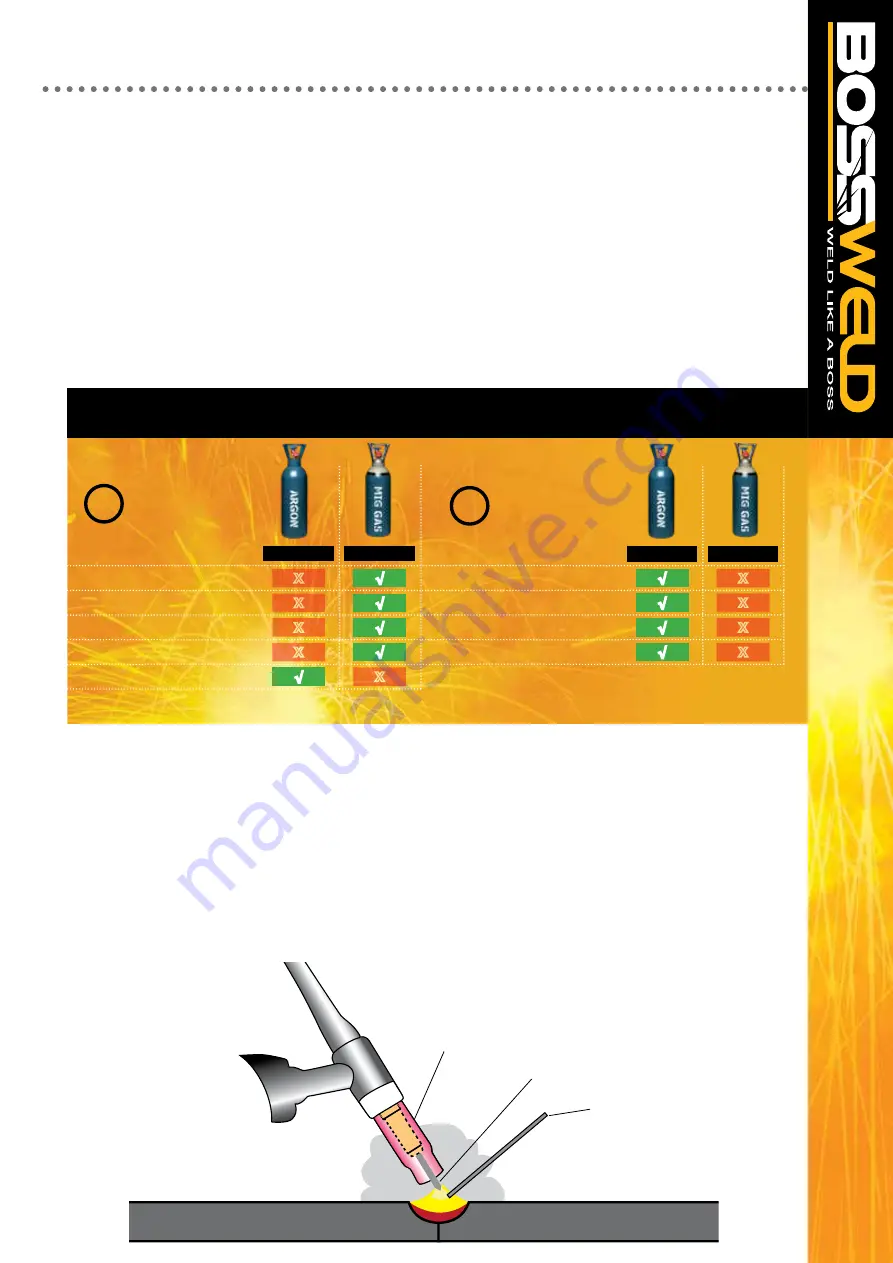
MIG WELDING
ARGON
Ar-CO
2
-O
2
MILD STEEL
√
√
√
√
X
√
X
X
X
X
STAINLESS STEEL
LOW ALLOY STEEL
GALVINISED STEEL
ALUMINIUM
M
MIG
T
TIG
X
X
X
X
√
√
√
√
TIG WELDING
MILD STEEL
STAINLESS STEEL
LOW ALLOY STEEL
ALUMINIUM
ARGON
Ar-CO
2
-O
2
WELDING
GAS SELECTION CHART
GUIDE
35
TIG WELDING - CONTINUED
This risk can be minimised using the ‘lift arc’ technique where the short-circuit is formed at a very low
current level. The most common way of starting the TIG arc is to use HF (High Frequency). HF consists of
high voltage sparks of several thousand volts which last for a few microseconds. The HF sparks will cause
the electrode - workpiece gap to break down or ionise. Once an electron/ion cloud is formed, current can flow
from the power source.
Note: As HF generates abnormally high electromagnetic emission (EM), welders should be aware that its
use can cause interference especially in electronic equipment. As EM emission can be airborne, like radio
waves, or transmitted along power cables, care must be taken to avoid interference with control systems and
instruments in the vicinity of welding.
HF is also important in stabilising the AC arc; in AC, electrode polarity is reversed at a frequency of about 50
times per second, causing the arc to be extinguished at each polarity change. To ensure that the arc is
reignited at each reversal of polarity, HF sparks are generated across the electrode/workpiece gap to
coincide with the beginning of each half-cycle.
APPLICATIONS
TIG is applied in all industrial sectors but is especially suitable for high quality welding. In manual welding,
the relatively small arc is ideal for thin sheet material or controlled penetration (in the root run of pipe welds).
Because deposition rate can be quite low (using a separate filler rod) MMA or MIG may be preferable for
thicker material and for fill passes in thick-wall pipe welds.
TIG is also widely applied in mechanised systems either autogenously or with filler wire. However, several
‘off the shelf’ systems are available for orbital welding of pipes, used in the manufacture of chemical plant or
boilers. The systems require no manipulative skill, but the operator must be well trained. Because the welder
has less control over arc and weldpool behaviour, careful attention must be paid to edge preparation
(machined rather than hand-prepared), joint fit-up and control of welding parameters.
TRIGGER
WELDING WIRE
FLUX COATING
ROD
ARC
CONTACT TIP
DROPLETS
SHIELDING GAS
ARC
MOLTEN WELD METAL
SHROUD
WORK PIECE
WORK PIECE
WORK PIECE
WORK PIECE
WORK PIECE
WORK PIECE
WORK PIECE
WORK PIECE
STRAIGHT GROUND
CORRECT PREPERATION
- STABLE ARC
INCORRECT PREPERATION
- STABLE ARC
RADIAL GROUND
ARC WANDER
TUNGSTEN ELECTRODE
GAS LENS
STABLE ARC
FLAT TIP
POINTED TIP
GRINDING WHEEL
GRINDING WHEEL
FILLER WIRE
Note: Do not use wheel for other jobs or tugsten can become contaminated and cause lower weld quality